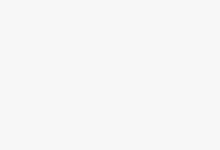
Hong Kong Crystal Group uses RFID system to trace garment production
[ad_1]
Hong Kong woollen company Crystal Group uses passive 13.56MHz RFID tags to trace the garments they produce. The group has established 15 processing plants in Sri Lanka, Vietnam, China, Hong Kong, and Macau. These processing plants can produce 90 million pieces of clothing each year. Crystal Group’s customers include Gap, Old Navy, Wal-Mart, Marks and Spencer, JC Penney, Ann Taylor and other companies.
Currently, 3 of Crystal Group’s 15 processing plants are using RFID technology to track the number of products produced by workers during working hours.
Due to the large production volume, Crystal Group attaches great importance to the speed and quality of the production process. In order to achieve this goal, the company pays close attention to the work process from sewing the newly cut fabrics to shipping the finished garments. At the same time, they also pay close attention to the work plan and salary of the workers.
Until now, Crystal Group still only relied on the barcode system to track the production process of the processing plant. Every time shift, workers use the barcode scanner installed in the sewing workshop to read the barcode number printed on their ID, and then scan the barcode number printed on them. Barcodes are placed on each bundle of items. Use this data to count working hours and track the production efficiency of a specific production line. However, the barcode system has several shortcomings: it is difficult to read data, it creases clothes, and errors often occur. The company wants a faster and more accurate scanning system, which can also make the back-end management system more complete. Therefore, in the past three years, Crystal Group has installed the RFID system provided by Malaysia’s GPRO Technology Company.
Crystal Group now uses GPRO’s SDT system. The RFID reader installed in the sewing workshop provides all the hardware facilities: including ID cards, clothing labels, label printing barcodes and readers. These all comply with the ISO 15693 RFID standard.
In 2004, the garment manufacturing company tested the system in its processing plant in China. Since then, the company has adopted this system in several production plants: two in Dongguan, China, and one in Hanoi, Vietnam. Crystal Group installed RFID readers in 8,000 sewing positions in three processing plants. In the next few months, Quek Kar Loon, CEO and founder of GPRO, said that Crystal Group plans to install readers in 4,500 positions in other production locations.
Using this new system, workers use their post RFID readers to read passive 13.56MHz RFID tags embedded in their IDs when they start to change shifts. The ID number of each worker shows the person’s name and position in the rear system of Crystal Group.
Every piece of clothing or every bundle of clothes has a plastic tag embedded with a passive 13.56MHz RFID tag. With it, every single product or bundle of clothes will be identified. Some clothes are transported as a single piece, they are hung on the hangers of the conveyor belt system, the rest are bundled and transported, and some are transported directly from the production line with rollers. In the sewing process, workers use their RFID readers to read the marked items or bundles of clothes, and they can also record the number of clothes they sew.
The data obtained by the RFID reader is transmitted to the back-end enterprise resource planning system and salary system of Crystal Group via the WAN. At the same time, these data are also transmitted to a password-protected web server hosted by GPRO. Workers can inquire about the progress of their RFID terminal, click the send message button, and they can know the production quantity, efficiency, and remuneration of their last shift.
The RFID tag of the clothes and the ID number of the worker are converted into a set of numbers printed on the cloth in the cloth cutting department. Old labels can be reused-re-encoded, re-attached to a bundle of clothes or a hanger, and then put back into production.
The SDT system also provides customized reports containing production data. Managers of processing plants can use these reports to identify and solve problems that occur in the workshop, and can monitor the number of products transferred from one production department to another, thereby minimizing product accumulation. The SDT system is presented on the computer screen in the form of an instrument.
Loon said that Crystal Group can recoup its investment in RFID within a year because the work flow has accelerated. The cost of a system like this mainly depends on how many RFID sites you have installed. In addition, Crystal Group will install RFID systems in all its processing plants by 2008.
[ad_2]