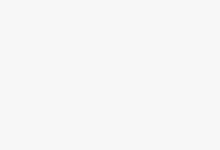
RFID-based manufacturing execution system (RFID-MES)
[ad_1]
1. Company profile
Chongqing Loncin Industry (Group) Co., Ltd. (hereinafter referred to as Loncin Industry Group) was established in 2002. It is a large-scale private enterprise specializing in motorcycles, motorcycle engines and closely related thermal power products across regions, large-scale and specialized group. The group has three business divisions, Loncin, Jinlong, and Special Machinery, and a technical center. It has an annual production capacity of 1.5 million motorcycles and 3 million motorcycle engines. The company has assets of more than 3 billion yuan and employees 7000 There are more than 1,000 people, including more than 1,000 senior technical management talents. Loncin Industrial Group is one of the largest motorcycle and motorcycle engine production bases in China. Its production and sales, revenue, exports and profit contribution are all in the leading position in the industry. The group mainly produces motorcycles under the “Loncin” and “Jinlong” brands and motorcycle engines under the “Loncin” brand. The group also produces recreational off-road vehicles, four-wheeled ATVs, electric bicycles, general gasoline engines, chainsaw machines, aluminum ladders, motorcycle cylinder heads, crankcase covers, cylinder blocks, aluminum alloy wheels, covers, lamps and other products. The products are exported to more than 80 countries and regions including the United States, Germany, France, Australia, Vietnam, India, Iran, the Philippines, Laos, Nigeria and so on.
2. The overall status of informatization applications
1. Current status of informatization application
In recent years, Loncin has invested a total of 78 million yuan in the construction of information technology. It has built a metropolitan area network in the three major industrial parks in Chongqing, and established a data dedicated line network with the Guangdong base and the Zhejiang base through VPN (virtual private network) to realize all parts of the company. Highly secure sharing of information between the two, and through the firewall to achieve intercommunication with the Internet, and covering suppliers and distributors.
In accordance with the 24-character policy of informatization “strategic orientation, demand traction, overall planning, step-by-step implementation, benefit-driven, and key breakthroughs”, Loncin’s informatization construction focuses on demand analysis and makes key breakthroughs in two aspects: management systems and innovation platforms. Since the implementation of ERP in June 2003 and the official launch in May 2004, Loncin has completely eliminated manual accounting, including procurement, sales, warehouse, and production. In order to meet the new management requirements of the company, Loncin introduced more advanced ERP systems from foreign suppliers in 2006. In 2006, the SCM (Supply Chain Management) collaborative business management system was successfully implemented, and 389 suppliers now use the system. In order to meet the needs of sales and dealer management, Loncin implemented a distribution management (DRP) system in 2008, realizing the unified management of the two brands of Loncin and Jinlong, and realizing sales, channel logistics, capital flow, and information Stream three synchronization.
In the construction of the enterprise technology innovation platform, Loncin strengthened the information management of the design and production process. In terms of new product development, three-dimensional modeling design software is used to realize virtual modeling, simulation testing, and data sharing, which reduces the time and cost of using physical tests to open molds in product development. In order to improve basic technology management, control product specification changes, increase the success rate of product development, systematize and standardize product development data management, and improve information sharing between production and sales, Loncin’s leadership decided to establish PLM The (product life cycle management) system allows Loncin’s management, technicians, and R&D personnel to quickly obtain the company’s basic technical management information through this platform, and at the same time improve the efficiency of teamwork. In addition, the system integration was realized between PDM and ERP, which eliminated the blind spots of information sharing from design to manufacturing, and achieved satisfactory results.
At the same time, the company’s informatization project has received strong technical support and assistance from government departments and experts from Chongqing University. At present, the company has established a long-term strategic partnership with experts from Chongqing University, and has cooperated on a number of projects, which has achieved good results, such as supply chain business platform, motorcycle RFID (electronic tag) production process management, and general-purpose production Execution (MES) system, etc.
Through several years of informatization construction, Loncin has initially realized the integration of industrialization and informatization, basically realized the integration of production, supply and marketing, and the informatization management of financial accounting, and basically realized the effective management of ERP, PLM, SCM and other systems. Through continuous deepening of the role of informatization in promoting management and continuous improvement, significant implementation results have been achieved in sales, manufacturing, procurement, product research and development, financial management, etc., and the “three-fold” of enterprise information flow, capital flow, and logistics has been achieved. Unification” has built a management support platform based on information technology.
Loncin’s informatization construction also has some shortcomings, such as: insufficient system integration, insufficient PLM and ERP integration, only the integration of unified coding, failed to achieve the linkage between specification changes and production BOM; ERP systems are not integrated, due to history The reasons for this include customized ERP and QAD (world famous ERP software company) ERP; human resources and ERP, DRP have not been integrated, and performance evaluation cannot be achieved; the application width is not enough, and the group’s decision support system has not yet been established; management process optimization is not enough, Some managers have insufficient knowledge of informatization, do not have a global view to consider problems, and repeatedly modify requirements in the system implementation process; the integration of industrial automation and ERP is not enough, mainly because the application depth of production process control and quality control is not enough.
2. Informatization development plan
In the next step of informatization planning, the overall goal is to build digital Loncin. Horizontally realize the integration of supply chain, namely: supplier-Loncin-distributor. Open up all links of logistics, reduce logistics costs, and maximize the overall profit of the supply chain. Vertically realize the integration of design, manufacturing and sales, namely: design-manufacturing-sales-after-sales service. Shorten the development cycle of new products and improve the core competitiveness of enterprises.
In the future, the focus of Loncin’s informatization construction is to seize the opportunity of Chongqing as a pilot zone for the integration of industrialization and industrialization to deepen the support of enterprise informatization for production and operation activities. With the theme of digital Loncin, through the integration of systems and data, Further accelerate the response to market demand and the speed of meeting it, based on KPI (Key Performance Indicators), to achieve online evaluation and performance appraisal. In terms of production process control, implement lean thinking, further improve asset turnover efficiency, reduce process occupancy, increase production process monitoring and quality control information and industrialization investment, so as to enhance the differentiated competitive advantage of products and services in the market. Further strengthen the Loncin brand.
3. Detailed introduction of participating informatization projects
1. Project background introduction
(1) Enterprise production management needs
The production scale of Loncin Motorcycles continues to expand, and refined and visualized production has increasingly become the need to improve the manufacturing level.
The following problems existed before the implementation of the project:
. Insufficient ability to monitor the status of the production site;
. Poor coordination between workstations;
. Lack of effective guidance on site operations and ingredients;
. Quality data entry lags behind, etc.
(2) National science and technology project support
In combination with the National 863 Plan, advanced RFID technology will be introduced into the execution and management of the production process of motorcycles.
2. Project goals
(1) The overall goal: to improve the level of on-site management, improve the pass rate and production efficiency of finished vehicles, promote the refinement of production organization and management, improve the quality of product manufacturing, reduce the consumption of manufacturing resources, and enhance the competitiveness of enterprises in the market.
(2) Focus on solving problems: Focus on solving the problems of insufficient ability to monitor the status of the production site, poor coordination between stations, lack of effective guidance for on-site operations and ingredients, and lag in quality data entry;
(3) Technical measures: Take RFID technology as the core, compatible with barcode technology, set up interactive operation control terminals at key stations, and establish an RFID-based motorcycle manufacturing execution system (RFID-MES).
3. Detailed introduction of project implementation and application
(1) System implementation
. The first production line of small-batch, multi-variety motorcycles is the object of implementation;
. Manage and control 22 key stations on the production line, and realize the whole process management and on-site paperless operation guidance of the complete production process of motorcycles from ingredients, partial assembly, final assembly, complete inspection, packaging, etc.;
. RFID technology with automatic identification function is used to identify material baskets, finished vehicles, and some workers. Combining existing barcodes to realize the tracking of the entire motorcycle production process, provide stable and reliable information for enterprise production management, and support management decision-making;
. A total of 23 quality collectors are installed on both sides of the final assembly line, and quality information collection points are set up in the repair area, so that the assembly quality problems of the finished car can be feedback in time.
Layout of production line control points (22 control stations in the entire production line)
A. There are 3 control points in the inspection, repair and certificate printing area: repair entrance, repair exit, and certificate printing.
B. The packaging (oil seal) line part has 4 control points: packaging on-line, bumper installation, packing box, and packaging off-line.
Production resource object ID
A. RFID tag identifies the material basket
B. RFID tag to identify the finished car: use the finished car electronic tag to track the entire production process of the finished car, and remove the electronic tag for recycling when the finished car is packaged off the line.
C. Control point equipment configuration
. Operation control terminal, reader, function button, sound and light alarm;
. Some stations are also equipped with audible and visual alarms, barcode guns and other equipment.
Assembly line quality acquisition device
23 quality collectors are installed on both sides of the final assembly line: workers enter the quality problems found in the finished car in time; timely feedback of quality information is shared within the enterprise, which provides effective support for the management to deal with, analyze and predict the quality problems of the finished car.
(2) RFID-MES system function
Remote control of production process
① Batch execution status of dispatching work order: master the execution process of batch production plan and the distribution of each batch on the production line;
② Production line status: work-in-progress information in different areas of the production line;
③ Work-in-process status: the status of each work-in-process on the production line;
④ Production cycle: master the production cycle of each key station and the entire production line.
Production process quality information management
①Statistics on the pass rate of finished vehicles offline: the pass rate of production lines can be counted by day, month, year and custom time period;
② Statistic quality failure information according to batches, models, series, parts, failure types, etc.;
③ Qualified rate and information query for the first and second repairs of finished vehicles;
④ Workload statistics: statistics on the workload and efficiency of quality inspectors and repair workers;
⑤ Data export: According to requirements, data can be exported to Excel.
Delivery plan execution management
.The dispatch plan is delivered directly to the production site
① Automatically download the ERP dispatch plan to the MES system every day;
② Send the dispatch plan and finished vehicle status configuration information to the on-site workstation;
③ Replace the original paper dispatch order.
. The production notice can be issued according to the production status of the workshop, and the workshop order can be issued.
Work station production coordination
① The production schedule is shared in the workshop in real time, and workers coordinate the ingredients and assembly: the planned implementation progress of the tire on-line station at the beginning of the production line is shared across the enterprise, effectively coordinating the engine assembly, engine ingredients, frame lettering and other station ingredients and production;
② After the adjustment of the dispatch plan order, notify the whole enterprise in time: the tire on-line station adjusts the dispatch plan execution order, and promptly and automatically informs the production line control stations to replace the previous team leader’s notice.
Batching and assembly management
① Visual guidance of electronic billboards: Each station is equipped with electronic billboards, which mainly display the status of the current vehicle model, craftsmanship and various operating prompts to assist workers in timely knowing the changes in production status and guide workers in their operations to avoid mistakes.
② Engine batching counting: Provide engine lowering counting function for engine batching station workers, instead of relying on worker memory counting, reducing manual counting errors and improving worker efficiency.
(3) Completion of RFID-MES system
. The project team has implemented the RFID-MES system on the first production line;
. The system application functions in the overall plan have been completed;
. Related documents delivered;
. Project implementation progress (2008.5-2009.12)
(4) Prospects for the later work of the project
RFID-MES system optimization (Goal: to create a more practical RFID-MES system)
① Optimize the layout of control points: evaluate and summarize the application effects of control points on the overall production line, and optimize the layout of control points.
② Optimization of application functions of control points: add electronic billboards at some control points.
③ Production process inspection data integration: In the inspection area, the finished vehicle label scanning is used to replace the original barcode scanning, and the inspection data is integrated into the RFID-MES system to build a complete vehicle production process quality data platform.
RFID-MES system extends upward
① Material logistics management: Use relevant technologies (RFID, barcode, etc.) to identify important materials, bins, etc.; synchronize logistics and information flow, support production scheduling decision-making, and reduce decision-making errors.
② Ingredients management: the integration of the execution process of the production line dispatching plan and the material information of the product accessories, on the one hand, supports the ingredients through real-time production information; on the other hand, guides the material transportation workers to feed materials and monitors the consumption of materials at the workstations.
③ Real-time adjustment of dispatching plan sequence: According to the real-time information of product accessories, support the real-time adjustment of dispatching plan execution sequence, avoiding production line lagging and overstocking of semi-finished products due to lack of parts.
RFID-MES system extends downward
① Garage operation management: On the basis of the finished car RFID identification, use RFID technology to identify the storage space and other resources in the finished garage, and support through the vehicle-mounted terminal (installed on the forklift), mobile handheld terminal and other equipment: inventory of the finished garage; forklift workers Management of outbound and inbound operations; application functions such as finding goods to improve the efficiency of warehouse operations.
② Product life cycle information management: RFID tags enter an open-loop environment after the product leaves the factory, collect information on distribution, use, and maintenance, and integrate with related systems such as product design and production process management, so as to build products covering product design, parts procurement, Production, warehouse, distribution, use, maintenance, recycling, destruction or reuse of the entire life cycle information management platform.
[ad_2]