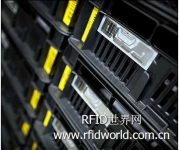
Dutch retail chain Schuitema’s two-year RFID fresh chain test results are good
[ad_1]
Dutch retail chain and wholesaler Schuitema said that its two-year fresh product supply chain testing project showed that RFID technology can provide multiple benefits. However, Schuitema also said that the participants in this project, including logistics and agricultural product providers, have not yet decided when to further test or fully adopt the RFID system.
This test project is called “Vers Schakel (Fresh Chain)”, and the purpose is to study how RFID technology can ensure the quality of fresh food in the supply chain. Participants assessed whether RFID applications can improve the on-shelf rate of goods, reduce losses and errors, and improve the visibility of the supply chain, thereby improving overall efficiency. The project ended in April this year, proving that RFID technology can improve efficiency in all areas of the supply chain, said Erik Hess, Schuitema project manager.
For the transportation of fresh produce from the place of production to the retail store, the Dutch Food Safety Law has a set of procedural requirements, including visual inspection and temperature detection. At the beginning of the entire supply chain, manufacturers, wholesalers and retailers require inspection of the appearance of fruits and vegetables, monitor the temperature of agricultural products, and manually record data using paper or PC.
This manual method, Rene Bakker, Schuitema’s retail director and chairman of the “Vers Schakel” project steering committee, said that it involves many processes and is prone to errors (such as incorrect transportation routes or excessive storage of products in the cold room).
The RFID system can collect data automatically and accurately, reducing manual errors. Bakker said that with manual systems, there is no real-time connection between cargo flow and cargo flow data records. In other words, the staff must record, enter and upload data to the database before the supply chain partners can see the results. The result of this delay usually results in damage and loss of goods.
In the test, 2500 reusable plastic crates were affixed with NXP Semiconductors’ EPC Gen 2 UHF RFID tags (chip manufacturers include several manufacturers including UPM Raflatac).
More than 2500 plastic crates are equipped with RFID electronic tags
Agricultural product distributor W. Heemskerk puts the packaged vegetables into crates at the production site. When the truck loaded with crates passes the factory exit, the RFID portal reader reads the crate tags. The reader is provided by Intellident and tested and configured by RFIQ Solutions. The crates are then shipped to one of Schuitema’s six distribution centers in Breda en Woerden. In the receiving area, a fixed reader reads the crate tags again.
W. Heemskerk staff label the crates
At the Schuitema distribution center, a fixed reader reads the crate tags.
Schuitema is responsible for delivering goods to 450 C1000 supermarkets in the Netherlands. One of the supermarkets, C1000 store Mario de Veij, participated in this test. When the C1000 store places an order to buy vegetables, the crates in the distribution center are loaded into the truck, and when they leave the center, the exit reader reads the tags. When the goods are delivered to the C1000 store, the tags are read again before being transported into the cold storage room. Similarly, when the goods leave the cold room, the tags will also be read. Finally, the empty crates are returned to the Schuitema distribution center.
The crates are read before they enter the cold room
In each shipment, several crates are equipped with temperature recorders designed by Wageningen University and Research Center. Every 5 minutes, the recorder saves the temperature reading data. The recorder is manually read after each transportation process. If an inappropriate temperature is found, RFID supply chain data is used to track where the problem occurred through time and location. The data of the recorder and RFID data will be downloaded to the EPCIS system.
If the crates loaded with agricultural products leave the cold storage room for more than 15 minutes, the system will automatically send a voice message or email to notify the staff. The system has two alarm time periods: one is the interval time period from when the product arrives in the store to when it enters the refrigerated room, and the other is the interval time period from when the product leaves the refrigerated room to when the crate is emptied or returns to the refrigerated room.
Bakker said that the use of RFID technology makes information more transparent and allows all parties in the supply chain to share information; ensure better product quality; reduce product loss by 10%; promote sales and reduce transportation errors.
Taking into account all the benefits brought by the RFID system, Bakker said it is estimated that a return on investment can be obtained within 2.7 years. However, Schuitema has not yet decided when it will officially adopt the system.
[ad_2]