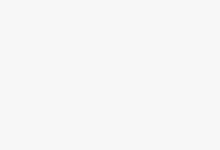
Hong Kong Li’an Electric Light Source uses RFID to improve material tracking and inventory visibility
[ad_1]
Hong Kong energy-saving light bulb manufacturer Neonlite Electronic & Lighting (whose Megaman products are sold in more than 80 countries around the world) is using RFID and ERP systems at one of its manufacturing plants to manage the production, inventory and shipping of products. This system-installed at Neonlite’s Xiamen factory in China in January 2009-provided by software company Infor, uses Intermec Technologie’s RFID hardware to track the flow of pallets containing bulb parts on the assembly line. GlobeRanger provides software for this application.
“Over the years, Neonlite has developed a series of energy-saving lamp products to meet the needs of different customers,” said David Fan, the company’s senior IT and system operations manager. With the expansion of business, the scale of the factory has continued to expand. In response to these growth, Fan stated that Neonlite decided to establish a single integrated management system to improve the visibility of internal logistics, parts management and processing.
“The vast majority of RFID applications are used in the supply chain or finished products,” Fan said. “Neonlite uses RFID throughout the production environment to improve product material tracking and real-time inventory visibility.”
Neonlite has adopted Infor’s ERP Syteline warehouse management software to manage internal parts and their consumption in production. The new RFID system greatly improves the visibility of the existing system and extends the visibility into the production process by tracking the movement of labeled parts pallets in factories and warehouses. Before adopting the RFID system, employees must fill in the transaction slip after receiving the parts or before the product is shipped, and then enter the data into the ERP system.
After using the RFID system, an Intermec 900 MHz passive EPC Gen 2 RFID tag is attached to the parts tray. When a pallet is full of parts and can be sent to a container, workers use Interme handheld RFID readers to read the pallet tags. When the pallet is sent to the production site or sent to the warehouse for storage, it will pass through an RFID portal reader (including Intermec IF5 fixed reader), and each tag will be read again. The door reader includes a motion sensor, which prompts the reader to approach the tray and the reader starts to read the tag.
When the pallet of labeled parts moves from one processing stage to the next processing stage, employees use a handheld reader to read the tags to upgrade its status. Managers can use the Infor SCM management software integrated into the company’s ERP system to view the exact location of the tray and determine when it is in that location. Once processing is complete, the finished bulb is placed in a labeling carton and placed on a labeling pallet. Then, the goods pass through the RFID portal reader multiple times before being shipped.
“SCM warehouse management system and Infor SCM RFID play a key role in Neonlite’s internal logistics operations,” Fan said. The former lets the company manage the parts when they move into the warehouse or send to another location. Infor SCM RFID compiles the reader data so that Neonlite can locate and manage product inventory in the factory. This system ensures that materials are delivered to the right place at the right time, thereby increasing the factory’s production capacity by 15-20%, Fan estimates.
Using SCM software, managers can determine the consumption time of parts, when new parts need to be purchased, how long it takes to process the product, how long the finished product needs to be stored before shipping, and their delivery time. GlobeRanger’s iMotion software platform is used to develop and test RFID business processes, including embedding motion sensors in Intermec readers.
If a pallet full of processed products passes through the wrong door reader at the wrong time or through the wrong door reader, the GlobeRanger software will issue an alarm and notify the manager via email or mobile phone. In addition, if the label of the box is missing, or the label of the carton does not correspond to the label of the pallet, the iMotion software will also generate an alarm.
The installation of this RFID solution has gone through multiple stages, Fan said. First, Neonlite, Infor, and GlobeRanger spent four weeks on conceptual design, evaluating Neonlite’s needs and the technology used. The development team tested physical containers (pallets and pallets) to determine the best labeling for them, and also studied the physical environment and the flow of materials and products at the production site.
At present, this system has not been fully applied, and some minor adjustments can be made. Neonlite plans to install this system in three other factories and hopes to receive a return on investment within two years.
[ad_2]