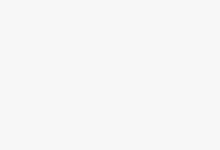
Bosch uses RFID technology to optimize manufacturing processes and internal manufacturing processes
[ad_1]
Robert Bosch is a subsidiary of the Bosch Group of Companies and is a leading global supplier of services and technologies in the fields of automotive and industrial technology, consumer goods and construction technology. The company has decided to choose noFilis, one of the world’s leading suppliers of device management technology software, to use their automatic identification technology to optimize manufacturing and logistics processes.
One of Bosch’s strategic goals is to slim down the production process and to innovate and optimize logistics processes.
Thomas Reitelbach, director of the production logistics application software development department of Robert Bosch, said: “If companies can straighten out the relationship between work processes, manufacturing and logistics processes, in the medium and long term, their business operations will definitely become very cost-effective. RFID is in Helping us to realize the concept of weight-loss production has been fulfilled on many occasions. “In two cities in Germany, Bosch has realized the use of RFID to collect data through the CrossTalk of noFilis and the Auto-ID Enterprise software system of SAP.
Two German factories, Bad Homburg and Bamberg, are the first to implement the RFID Kanban operation process (purchase on demand principle)
The Bosch factory in Homburg first adopted IT technology to realize the concept of slimming in the manufacturing process. In this diesel engine production plant, the Kanban principle is used for the purchase of production process parts. Initiating production planning and implementation according to the needs of the recipient is the basis of the Kanban principle. Reitelbach said: “We see that RFID has great potential. The first phase of the slimming plan aims to eliminate manual barcode data scanning and input, and use an automated logistics control system to make the production process run as required. Everyone sees Manual scanning is time-consuming and resource-consuming. RFID can help us receive real-time and transparent manufacturing process and internal logistics process information. When workers in the Bamberg factory receive semi-finished parts boxes at the end of each production line, and stack them in another container, all relevant Information such as the owner of the equipment, the number of equipment, date and time will be automatically collected through 32 HF RFID reading points and the enterprise reporting system, without manual scanning and data input. In the Homburg factory, the so-called smart mailbox: empty container Kanban card is scanned by UHF RFID in 36 mailbox locations, thereby automatically triggering the action of replenishing equipment from the neighboring warehouse and SAP system. Because Bosch can reduce inventory, the production area of the production workshop is greatly reduced, and the equipment The planning and implementation of the supplementary logistics process have been optimized. These improvements have saved Bosch a lot of money. The congestion of the workshop area has been greatly improved, and there has never been a production line shutdown because the equipment supplement cannot keep up.”
NoFilis’ CrossTalk and SAP’s Auto-ID Enterprise are combined into a scalable solution
Reitelbach said: “After Bosch decides to use RFID to optimize business processes, we need to evaluate the application prospects of the most suitable IT system. The new software level should be able to support the configuration, management and monitoring of scattered AutoID automatic reading points. It can temporarily store the read data in the event of a failure. The solution we seek should be able to process and integrate the new AutoID technology, and it is very stable, convenient and reliable. It can be seamlessly integrated into the end of the existing SAP system and the system’s availability Upgradability is another very important criterion that we chose. Because after the positive results of two exploratory factory slimming plans, Bosch is determined to launch the world’s first RFID automated production factory. Through extensive and in-depth selection of system manufacturers, we Finally, it was decided to adopt the CrossTalk of noFilis company and the Auto-ID Enterprise system of SAP company. Because the integration of these two systems best meets our needs and goals. The future-oriented software level is composed of the best device management software and data acquisition software. Of course There is also a standard natural SAP system integration function. NoFilis’s software can just fill up the deficiencies of the SAP software system. The total time from the decision to choose SAP and noFilis to the completion and commissioning of the Homburg plant is less than 4 months. The Homburg plant The installation of the system started in April, and the system was put into operation in July.”
Patrick Hartmann, global sales director of noFilis, said: “The project can be completed in such a short time mainly because Bosch has assigned a very skilled and professional project team from various departments, with leaders and technicians. A large number of existing SAP The cooperation project with noFilis is also very helpful. Based on the successful experience of the first project, I believe that Bosch’s second project at the Bamberg plant will be completed within two months, that is, August.” (Text/Zhuang Biao) micro)
[ad_2]