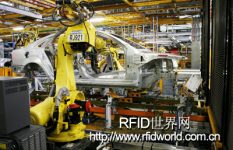
Car manufacturer Continental uses RFID to track parts inventory
[ad_1]
Continental Automotive uses an RFID system to track warehousing in its 80,000-square-foot manufacturing plant in Huntsvillein stock.This global auto parts manufacturer uses RFID technology to track reusablecontainer. The manufacturing plant receives the parts, assembles them into interior and power train components, and then ships them to the automobile company.
The system is built on Microsoft BizTalk Server 2006 R2 platform and SQL server, using Xterprise Clarity Automated Goods Receipts (AGR), AGR is responsible for managing the relevant data of Benshi’s raw materials, and Clarity Reusable Transport Items (RTI) software, RTI tracks reusable parts boxes.
Continental receives more than 5000 types of automotive electronic components, such as transmission control, from 158 suppliers (80% of which are overseas)Devices, airbag controllers, GPS devices, car audio and other electronic equipment. One of the factory’s three third-party logistics service providers first receives these materials, unpacks the items, and puts them into reusable plastic containers.These containers are transported to the Continental factory (in a certainIn some cases, plastic containers are placed on reusable plastic pallets), factory workers unload the containers and use a forklift to deliver themIn the factory.
Before adopting the RFID system, Continental Automotive employees scanned the barcode labels on the containers when they received the goods.also, The company’s logistics project manager Gokhan Sarpkaya said that the logistics service provider will issue an advance delivery notice, and then Continental Staff records manually. This process sometimes causes delays in the recording of advance shipping notices.
Therefore, the company seeks an automated cargo receiving system that can reduce inventory inaccuracies caused by delays in early delivery notifications and human errors.Reduce the time required to scan the barcode label of each container, allowing managers to track 80,000 reusable containers (total priceWorth about 3 million U.S. dollars).
This set of RFID solutions reduces losses and container hoarding, which can lead to excess parts boxes in some locations, and assembly in other locationsShortage of boxes, etc. With each reading, Continental can track the location of the container and its contents.By reducing the reading of barcodesTime, the new system is expected to increase the processing speed by 70%.
After careful research, Sarpkaya chose Xterprise. Xterprise once provided RFID software and system integration for iGPS, and obtainedIn addition, the RFID system provided by Xterprise uses Microsoft BizTalk Server, which is exactly theWhat Continental’s IT department needs. BizTalk server integrates a variety of business processes required for receiving, quality assurance and storage processes,, And realize real-time information communication in the business process, eliminate errors and reduce manual intervention, Enrique Andaluz, Microsoft Industry Market Development Manager say.
At the factory, Continental installed Motorola RD500 RFID readers for five forklifts.Every third-party logistics provider is equipped withMotorola handheld reader provided by Continental.All reusable containers and pallets are affixed with EPC Gen 2 RFID tags, And has a unique ID number.
At first, Continental sent a delivery request for a certain item to its logistics provider.The order is in the Continental’ SAP ERP system withCorrespond to the ID number of the specified container.The employees of the third-party logistics provider take the ordered goods and put them in a specific part boxinside.When the container is filled with parts boxes, a handheld reader scans the container label, and the unique ID number of the label is sent through the wireless connectionFor SAP system using Clarity RTI software.
Once the parts box label is scanned, Continental knows that the item is loaded into the container and is in transit.When the container was delivered to Continental’s Huntsville factory, workers used RFID forklifts to unload the goods.In the process, the forkliftThe reader reads the ID number of the container tag and sends it to Clarity AGR software via Wi-Fi connection, which in turn combines the ID number with the materialThe order corresponds and is sent to the SAP system to indicate that the parts box has been sent to the factory.
The SAP system not only stores the container data, but also stores the location where the container should be stored in the manufacturing plant-whether it is in the selected rack or smallAutomatic load storage and retrieval system (AS/RS). The Clarity AGR software then sends the location information to the forklift reader and displaysOn the forklift screen for the forklift driver to read. In this way, the driver greatly saves the search time for each container.
When a parts box is placed in a small load AS/RS system, it is sent to a conveyor belt and flows through the Alien ALR-9900 Enterprise RFID reader, the reader reads the tag ID number of the container and forwards it to Clarity RTI software to confirm that the part box is correctIt is sent to the small load AS/RS system. When the parts box is used up, the empty parts box is cleaned and flows through another ALR-9900 Enterprise Reader. This prompted the system to change its status to idle and then send it back to the third-party logistics provider.
According to Xterprise account manager Rick Koskella, the challenges faced by this system include finding an accurate reading on plastic containers.In order to reduce the electrostatic charge generated by the internal electronic products, the container contains carbon fiber. Koskella says fiber is similar to goldGenus, it will affect the reading of the tag.To solve this problem, Xterprise adopted a custom label from William Frick and Co.’s, The tag adds a layer of foam between the parts box and the UPM RFID inlay in the tag. The read rate of the entire system reaches 100%.
[ad_2]