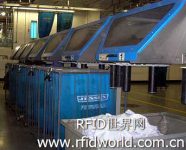
Clothing washing company uses RFID guided sorting system to promote production
[ad_1]
Canadian Linen and Uniform Service is an 82-year-old linen product and work clothes sales, rental and cleaning service company in Toronto, Canada. The company has more than 80,000 customers in multiple industries.
As early as 10 years ago, the company began to use the low-frequency passive RFID tags of Swiss company DataMars to track the life cycle of rented clothing and linens. This year, the company merged its two laundry factories in the same place; taking this opportunity, Canadian Linen uses an RFID automatic system to replace the manual sorting of laundry to speed up the application of RFID technology.
The use of an automatic sorting system can reduce labor by 17% and increase the capacity of the laundry system by 50%, said Dave Sweeney, operations manager of Canadian Linen.
Previously, workers had to process the laundry piece by piece, using a fixed RFID reader to read the DataMars T-BH7550-S tags sewn into the clothing, and then put the clothing into the sorting box according to the type (shirts, pants, etc.). Now, Sweeney says, the clothes are placed on a conveyor belt with 3,000 embedded “pockets.” When the conveyor belt conveys the clothing through a reading area, the clothing label is read. The tag data is sent to the back-end software. The software identifies the clothing according to the ID number of the tag, sends a command to the conveyor belt, and throws the clothing into the appropriate sorting box.
According to Sweeney, the merger of the two factories provides an opportunity for Canadian Linen to upgrade its clothing sorting system. Sweeney declined to disclose the company’s expected return on investment, but said the company usually only invests in projects that receive a return within two years.
Clothes sorting system
The company’s existing RFID lifecycle tracking system provides Canadian Linen and Uniform Service with historical visibility of each piece of clothing, including when and who worn it, the number of times it was washed and repaired, and the location of the clothing at any time during the service. In the past ten years, Sweeney claims that the system eliminates errors in order and inventory counting and improves the quality of customer service.
A few years ago, many of the company’s competitors used barcodes instead of reading labels with the naked eye. Sweeney said that Canadian Linen has never used barcodes. “For our competitors who use barcodes,” he said, “if they want to start using RFID, they will have to run two systems at the same time for a longer period of time.”
Ultimately, Canadian Linen hopes to use a high-frequency system to read clothes in batches.
[ad_2]