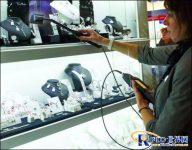
French jewelry retailer Cleory adopts RFID system in 50 stores
[ad_1]
French jewelry retailer Cleor said that since the company installed an RFID system in 10 (50 in total) stores a year ago, the inventory count time of each store has been reduced from the past few days to a few hours. Cleor’s distribution center and 10 stores in the Paris area spent 8 months implementing this plan, and now the company has begun to apply this plan to the remaining 40 stores.
Cleor has been selling jewelry in Paris and other cities in southwestern France for nearly 10 years. By the end of 2011, the company plans to add 10 branches. Currently, the company sells approximately 1 million pieces of jewelry each year. The Cleor distribution center receives jewelry bags from suppliers in Europe and Asia. Each package contains up to 100 pieces of jewellery, and the employees of the distribution center must unpack the package and compare each piece of jewellery with the order placed by the jeweler. In order to perform this task, workers must scan the barcode label on each piece of jewelry to record the receipt of the goods in the company’s back-end management system.
The received jewelry may be stored directly, or some (usually 20-30 pieces) may be placed in smaller bags and shipped to the store. When the store receives the jewelry bag, the clerk scans the barcode of each piece of jewelry to confirm the receipt time, and scans the label again when the store regularly counts to determine whether the product is in the inventory room or on the sales floor. Due to the small size of barcode labels, a lot of labor is required to scan to ensure that each barcode label can be scanned. This process is very time-consuming for goods receipt and inventory management, the company said, and if the barcode is blurred or not scanned, errors will occur.
When Cleor chose to use RFID technology to replace this system, the company hoped that the RFID solution used could not only be easily installed, but would not affect the existing management process. The final system includes Tageos custom reader antennas, Impinj’s RFID readers and Psion Teklogix RFID handsets.
Store employees use a handheld device and a paddle antenna to check the jewelry in the showcase
The solution installed by Frequentiel needs to be integrated with Cleor’s ERP software so that it will not change any existing management processes. The system also requires hardware that can read very small RFID tags in distribution centers and stores, and at the same time ensure that the tags of each item can be read every time the store counts, so that workers can compare products and their pictures to confirm that there are no jewelry tags The situation of exchange. Frequentiel and Tageos collaborated, the latter developed a reader antenna for the Impinj Speedway Revolution reader. The Psion Teklogix handheld uses the Impinj Indy reader embedded chip, said Scot Stelter, senior director of product marketing at Impinj. This system uses 6 Toshiba RFID label printing and encoding machines.
In order to read the tags of the jewels stacked together in the distribution center, Tageos designed the Cube-12-inch metal box with a small RFID antenna embedded in the wall to read tags from multiple angles, said Lucien Repellin, Tageos’ business development director. The Cube is wired with an Impinj reader, which can read the labels of 100 pieces of jewellery in the plastic bag.
The employee of the distribution center places a bag of jewelry on an RFID mat, confirms the correctness of the goods, and upgrades the status
The Cleor distribution center uses 6 label printing and encoding machines to write a unique identifier for each Tageo UHF EPC Gen 2 passive RFID label, and print a barcode version of the same ID code on the label. If the RFID tag reading fails, the barcode can provide redundant protection. The distribution center then sends these RFID tags to partner suppliers. At present, about 65% of company suppliers send labelled jewelry to Cleor, and Cleor hopes to achieve 100% labeling by suppliers eventually. When the distribution center receives a package of jewelry from the supplier, the worker places it in the RFID Cube. Frequentiel software then corresponds the tag ID code of each piece of jewelry in the bag with the product’s SKU, description and photo (stored in the Cleor management software provided by Odeis).
When the distribution center receives a package of non-labeled jewellery bags, the employee attaches an RFID label to each piece of jewelry, uses Toshiba equipment to encode and print the label, and correlates the ID code of the label with the SKU and other product information in the Odeis system. correspond. The newly-labeled goods are then put back into the bag and placed in the Cube. When Cube reads the label of a piece of jewelry, the product status is updated in the management software, indicating that the distribution center has received the goods.
When the distribution center employee receives the store order, the employee takes the jewelry required for the order and puts them in a small bag. The small bag was then placed on an RFID mat measuring about 1 square feet in size, and an embedded Tageos RFID reader antenna was connected to the Impinj reader by wire (the working group ruled out the possibility of using another Cube, because the small bag contains more With fewer RFID tags, the use of mats is more suitable and the cost is cheaper). When the small pad reads the label, the Frequentiel software reads the ID code and again corresponds them to the SKU and other identification symbols in the Odeis software. The software then confirms the accuracy of the order, and the upgraded goods status is shipped out.
Tageos designed the Cube, a metal box with a small RFID antenna embedded in the wall, which can read tags for up to 100 pieces of jewelry
In each store, the same style of Tageos mat antenna and Impinj reader will be used to receive new products from the distribution center. The package is placed on the mat, the label reading information is forwarded to the Odeis system, indicating that the jewelry has been received by the store, and the goods are then placed in the display case. In order to count the jewelry in the cabinet, employees use a Psion Teklogix handheld and a paddle antenna, which is shaped like a large toothbrush, and the reading distance is set to 5 cm to ensure that one label is read at a time. When the employee waved the paddle antenna over the tag, the handheld screen displays the description and picture corresponding to the tag ID code, so that the employee can confirm the consistency of the tag with the jewellery. The reader software stores the ID code of each tag read. After completing the inventory process, the employee then plugged the reader into the PC, and the inventory list was upgraded to Odeis software. If the product is found to be missing, the PC will display a high-brightness warning.
According to the store manager, for each retail store, this process-which previously took four days-currently takes only four hours to complete.
At the cash register, when the jewelry is sold, it is placed on the same mat antenna, the ID code of the product tag is read, and forwarded to the back-end system, which indicates that the product has been sold. The employee removes the tag from the jewelry.
The RFID system saves bar code scanning time, Repellin says, and it also improves leanness. The system realizes the automatic confirmation of the accuracy of each order, (before the order leaves the distribution center), the goods are read again when they are received in the store to confirm the complete receipt of the ordered goods. All this information is stored in the back-end system. According to Cleor, this process reduces shipping and receiving errors.
AurĂ©lien Senechal, Cleor’s director of management, said the company is very satisfied with the system. “This innovative RFID solution has reformed the process of the jewelry industry,” he said.
[ad_2]