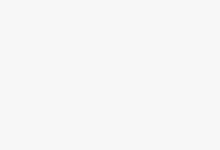
RFID mobile smart management Formosa Plastics enterprise Smart inspection application example
[ad_1]
Li Jianzhou, project manager of the Formosa Plastics Network System Software Business Group, took the Smart inspection application of the Formosa Plastics Corporation as an example to share how to implement inspections and equipment maintenance/repair corrections when the company has a wide range of factories and a wide variety of equipment.
Li Jianzhou pointed out that in the past, Formosa Plastics plant inspections used paper work record sheets, and then input record data in the back end to generate reports. Today, Formosa Plastics Network Technology uses radio frequency identification (RFID) technology to develop Smart The inspection system adopts 13.56MHz high-frequency band RFID tags and sensors with a sensing distance of 10~30cm, and RFID tags are attached to each inspection point, and the staff holds a PDA device with sensing function for inspection.
The flow structure of the Formosa Plastics Network’s Smart inspection system can be divided into three levels: inspection system, personnel execution progress inspection, and integration with the back-end AP: After the inspection system sends out the route and dispatches the work, it downloads the dispatch through the PDA device. Work data, accountable items and routes; according to the dispatching data and routes, the personnel hold the PDA to each inspection point. After the inspection is confirmed by RFID, the personnel also read the meter at the same time; at this time, the entire record data is uploaded to the inspection system, The system automatically executes inspection benchmarks and route building, inspection data analysis, report output, inspection exception notifications, trend exception notifications, and links to the back-end enterprise resource planning (ERP) system, mail server (Mail Server), Repair dispatch orders and maintenance system.
The Formosa Plastics Network Smart Inspection System has functions such as inspection benchmark file establishment, task route file establishment, smart dispatch, announcements, inspection trend analysis, report output, inspection abnormal notification, trend abnormal notification, etc. The manager only It is necessary to enter the period (for example, weekly, bi-weekly, monthly or quarterly) and fixed time interval to create various inspection tasks and automatically dispatch workers to follow up through the system. With the flexible system inspection task file, it can avoid the tedious labor dispatching procedures, and the system controls each inspection task at the same time.
After the inspector downloads the inspection task, he can immediately carry out the inspection with the PDA through clear task instructions, conduct real-time information collection, and implement equipment maintenance. Once the equipment inspection benchmark exceeds the preset value, the system will take the initiative to warn, and the processing method when the equipment is abnormal can be input in advance (self-maintenance/outsourcing/scrap) to speed up the emergency treatment of the first-line inspectors when they encounter abnormal conditions aging.
The Smart inspection system can be applied to industrial safety inspections, pipeline inspections, plant inspections, independent inspections, project inspections, and process management. At the same time, this system also integrates back-end ERP, manufacturing execution systems (MES), and Flow electronic forms. , Business Intelligence (BI) and other systems to add value to the overall benefits. This inspection system is a flexible organizational setting. No matter how many factories the company has or a multinational company, it can meet the needs through organizational settings. Even if the scale grows in the future, the organizational hierarchy can be set by itself to meet The need for future expansion.
Li Jianzhou also actually listed the application examples of this inspection system. In terms of integrating the ERP system, such as the time of equipment inspection, abnormal case filing control (when abnormal conditions occur, a repair order can be opened immediately for filing control); in the integration of Flow electronic forms In terms of processing, such as the processing of smart dispatching OA subpoenas; in addition, it also integrates mobile phone text messaging functions, such as sending instant notifications of text messages when the inspection is abnormal. In the part of introducing benefits, the inspection route planning can improve the efficiency of E-operations. In addition to saving manpower and materials, and achieving real control, it can also actively prompt for work items. When abnormal data occurs, it can also be tracked immediately.
Among the companies affiliated with Formosa Plastics, including Formosa Chemicals, Nanya, Formosa Plastics, etc., have introduced this inspection system. At the same time, the machine equipment/process inspections of the 120 subsidiaries of Formosa Plastics Corporation and the PDA inspection are integrated. The introduction of PDA M for patrol inspection of pipelines/high towers/stands, and PDA M for maintenance of the refinery equipment of Formosa Plastics has also been completed. Currently, Formosa Plastics Corporation uses about 1,000 PDAs and 50,000 RFID electronic tags online, and it will continue to increase in the future.
[ad_2]