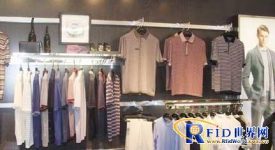
A case of using Yaosheng’s wireless barcode in clothing logistics
[ad_1]
In the past few years, focusing on barcode applications, Yaosheng barcode has successfully provided a series of solutions for customers in the fields of electronics manufacturing and chemical industry. Fiber and other enterprises have established long-term and stable cooperation. At the same time, Yaosheng Barcode has also expanded its barcode solutions to the apparel industry, with customers including Jinba, Sevenwolves, Jiumuwang, and Ports. In July 2006, Yaosheng Barcode helped Rimula successfully implement the wireless barcode management solution and achieved good application results.
The role of barcode technology in the apparel industry is mainly manifested in:
1. Improve the accuracy of receipt/delivery.
The purchase of the clothing industry is usually carried out according to orders, including production orders, processing orders, purchase orders, etc., with the characteristics of small batches and multiple batches. When shipping according to the order, due to the various information related to style, color, size, etc., a large number of color and code combinations often occur, which brings additional transportation costs for return/exchange. The use of barcode scanning can accurately record the arrival and order execution. By collecting the barcode information on the items, the delivery accuracy can be effectively improved, reaching more than 99%.
2. Easy to grasp inventory information.
Accurately grasping inventory information plays a very important role in the operation and management of apparel companies. The application of the wireless barcode system in the warehouse is shown in Figure 1.
3. Timely and accurately collect terminal sales data.
The distribution system of the clothing industry includes various forms such as special counters, specialty stores, and shop-in-shops, which are distributed all over the country. With the occurrence of sales behaviors, a large amount of information is frequently generated. Barcode technology can realize data collection while product sales, and accurately transmit the data back in time through the information system. as shown in picture 2.
4. Convenient for inventory counting.
Apparel companies usually need to take inventory of warehouses and stores on a regular basis. Manual operations are time-consuming and laborious. Using barcode technology, data collection can be done directly through scanning, which is convenient for companies to accurately grasp inventory, profit and loss and other information.
5. Facilitate data analysis.
The back-end system can analyze data such as sales, inventory, orders, receipts, and out of stock, so that companies can formulate production, sales, and distribution plans in a timely manner based on market demand.
How does the value of using wireless barcode management solutions in the apparel industry reflect?
Wireless barcode management solution technology is based on barcode technology, which is a kind of information management technology, and its adoption often requires a certain process. In the manufacturing industry, almost all manual operations were adopted at the beginning, and then the ERP system was gradually established with the help of information management tools such as computers.
Wireless barcode management solutions can help apparel companies achieve faster and more accurate process management. With the increasingly fierce competition in the clothing industry, the life cycle of clothing has become shorter and shorter. Take men’s jackets as an example. According to our understanding, in order to ensure the profit of a batch of new products, the average cycle from receiving customer orders to product launches must be controlled within 13 days by apparel companies, because once this time is exceeded, one day later, it will lose Thousands of yuan.
One of the most obvious management features in the clothing industry is the comprehensive management of styles, colors, and sizes in the warehouse entry and exit link. Many clothing companies deal with thousands of styles, colors, and sizes every day, and the general invoicing system cannot meet this management requirement. . The error rate of manual memory operation alone is extremely high. Especially the warehouses of clothing companies often make mistakes when packaging and shipping according to customer orders, resulting in unnecessary returns and exchanges, delays in the time of stocking, and ultimately affecting product sales.
The wireless barcode management solution can manage brand, category, color, style, size and other information through barcode. After the clothing comes off the production line, it is scanned and stored in the designated location of the warehouse, which shortens the delivery time, improves the accuracy rate, and reduces the additional transportation costs caused by shipping errors.
In 2006, the wireless barcode management solution provided by Yaosheng Barcode was successfully launched in Rimula (China) Co., Ltd.
Rimula’s wireless barcode management solution is jointly provided by Motorola Enterprise Mobility (formerly Symbol Technology Corporation of the United States) and Yaosheng Barcode. The solution includes the implementation of a wireless warehouse management system in Rimula’s material warehouse and finished product warehouse. Stores and stores conduct real-time data collection, realize real-time information sharing and communication with the headquarters, and solve the problems faced by Jinba in warehouse management and supply chain management.
Since its franchise business started in September 2000, Jinba has thousands of franchise outlets in 32 provinces, municipalities and autonomous regions across the country. With the continuous expansion of business scale, the number of goods and varieties items that Jinba exports every day is very large. At present, relying solely on manual inspections of the delivery status, it is impossible to avoid the wrong delivery or missed delivery when multiple styles and models are mixed. condition. At the same time, because the production and finished product warehouses cannot understand the market feedback information in time, it is often that the products needed on the market are not stored in the warehouse, and the products with unsatisfactory market sales are piled up like a mountain, causing a lot of waste. Therefore, Jinba considered using informatization to improve the level of warehouse management and distribution business.
At present, Rimula’s wireless barcode system process includes outbound information collection, scanning result query, distribution warehouse inventory, store inventory and other links.
When collecting outbound information, the operator uses the MC3000 to scan a product barcode each time, and the data is transmitted to the background in real time. The system automatically accumulates the number of the category that has been scanned, and compares the total number of scanned items with the category in the original shipping order. Comparing the planned shipments, if it is equal to or greater than that, the corresponding prompt will be given in time, and the scanning of similar categories will no longer be accepted. Each scanned box number and corresponding product barcode will be saved in the barcode interface table, and other useful information, such as operator code, shipping order number, shipping date, etc., will also be recorded.
When performing inventory in the distribution warehouse, the operator uses the MC3000 to scan the barcode of the goods, and the data is transmitted back to the barcode interface table in real time to form a temporary inventory list. The Rimula background system processes the inventory list in the bar code interface table, compares the differences with the system, and forms an inventory difference report that can be sampled by item, location, or warehouse.
When performing a store/store-in-store inventory, use MC1000 to scan the barcode of the goods. When a batch of data collection is completed, the collected data will be sent back to the barcode interface table through the cradle or GPRS to form a temporary inventory list. The software can be implemented by The development language directly calls the ActiveSync API to access the data of MC1000. The Rimula background system processes the inventory order in the bar code interface table and compares the differences with the system to form an inventory difference report.
The wireless barcode management solution has helped Rimula realize the inventory of the product quantity in specialty stores and warehouses at any time. This is a task that used to require at least 30 employees to work for two days at full capacity.
In the supply chain management link, since the current sales information can be shared with the headquarters in a timely manner, Jinba can replenish goods in time to achieve fast and efficient logistics links. At the same time, timely and accurate data collection helps decision-makers quickly grasp market information, and then respond quickly and make decisions quickly, effectively improving management efficiency.
Do companies need to have certain conditions to implement solutions such as wireless bar code management? What are these conditions? Not all clothing companies are suitable for using wireless bar code management solutions. This requires two conditions: First, the product To achieve a certain sales volume; secondly, the company itself has a sound sales network, generally around 2,000 stores. Therefore, the current application of wireless barcode management solutions in the apparel industry is still in its infancy. It is not a technical problem, but the market itself is very limited.
Based on Yaosheng Barcode’s past project experience, what are the difficulties in promoting wireless barcode management solutions in the apparel industry? What are the reasons?
From the perspective of customer demand characteristics, the informatization construction of the clothing industry is usually realized step by step, starting from the marketing system, which is what we often call the invoicing system, then the warehouse management system, and finally the production link information system Construction. Due to the complicated technological process involved in the garment production process, this part of the information construction is more difficult.
The reason for this phenomenon is simple. The first thing all clothing companies care about is marketing and sales. However, in the development process, due to the lack of timely information and unclear information, the inventory gradually rises, and even the entire process has problems, they begin to realize The importance of controlling the product cycle. In addition, from the perspective of cost, the construction of the information system of the store generally only needs tens of thousands of yuan, and the construction of the back-end system ranges from several million to tens of millions. Only companies with a certain financial strength and a certain information team can do this. investment.
With the improvement of enterprises’ awareness of informatization construction, wireless barcode management solutions have been promoted in the apparel industry in the past two years. As a system integrator, Yaosheng Barcode is mainly responsible for helping customers customize some software and establish a complete back-end system. The most difficult and critical task is budgeting and testing to ensure the reliability and stability of the entire system. This task usually takes 2-3 years.
At present, some companies have implemented advanced information management models in the entire supply chain, such as Guangdong’s Luen Thai. We believe in the existence of this market. On the one hand, there are many footwear and clothing companies in Fujian Province. In the process of market development, they will gradually accept information construction. On the other hand, although many clothing products on the market use barcode technology on their labels, most of them are a kind of “false appearance”, just staying in the store’s purchase, sale and storage function to ensure that a certain type of price is the same The product of does not make mistakes when receiving payment. The reason is that companies do not have a sound back-end information system. These barcodes simply cannot realize one-by-one item tracking, let alone the processing of a series of information such as colors, styles, and models.
The application of wireless barcode has many advantages. The data transmission rate can now reach 11Mbps. It is a supplement and extension to the wired networking method, which makes the computer on the Internet mobile and can quickly and conveniently solve the problem of using wired methods. Network connectivity issues.
[ad_2]