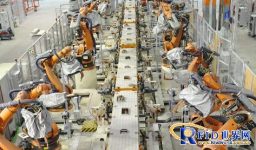
An electrical company in Zhuhai applied RFID technology to improve production and logistics management
[ad_1]
Software introduction
1 Overview of requirements
Informatization, automation, networking, intelligence, and flexibility have become the distinctive features of modern manufacturing enterprises. With the popularization and development of information technology and network technology, especially Internet technology, it has solved the standard problem and cost problem of information sharing and information transmission, making information more widely used as the basis and basis for control and decision-making. In order to reduce costs and speed up capital turnover, it is necessary to further solidify new processes or new management systems so that they can be implemented in a standardized manner. The RFID management information system can solidify management and optimize operations.
RFID work-in-process tracking management system, combined with ERP and MES material management system, automatically and intelligently guide the operation of the production line, real-time feedback of production information, production data analysis and monitoring, strengthen the control of production and logistics, and improve the enterprise’s technological innovation ability and market response speed , The comprehensive competitiveness of the enterprise.
Zhuhai Gree Electric Appliance Co., Ltd. applicationRFIDTechnology cooperates with ERP and MES to improve production and logistics management data source to ERP, and material data management mainly comes from MES.
2 RFID solution
2.1 Data source and technical plan planning
The integrated application of RFID technology in the on-site data terminal of the workshop fully adapts to the complex requirements of the industrial environment without direct vision or manual scanning, which effectively and concisely solves the problems of data collection, data accuracy and real-time input;
Provide data module design for “individual” or “batch” level, real-time, accurate, precise and efficient traceability and tracking of materials and work-in-progress, and use this as the core to establish a real-time file at the individual level of the product to realize the life of the product Cycle tracking and management;
Apply RFID, MES network technology, etc. to production control, accurately, real-time, and comprehensively reflect the status information of the production process, effectively and agilely guide the industrial process, form a good complement to ERP, promote the construction of “transparent factory”, and promote production, management and The optimization of the organizational structure promotes the realization of the production model;
The tracking management of “materials” and “work in progress” is closely integrated with quality, benefit, efficiency, warehouse management, logistics, etc., to encourage workshop workers, manufacturers and material suppliers to form a community of interests.
The application of RFID in the traditional manufacturing industry (MES) project makes full use of the characteristics of RFID, adopts specific RFID data collection terminals that can be installed in complex industrial sites, adapts to the environmental requirements of traditional manufacturing workshops, and is moisture-proof, oil-proof, lightning-proof, The performance of electromagnetic interference, heat protection, etc. meets the needs of non-contact automatic collection of materials and products in progress, and provides information input interfaces and query interfaces for the management system. At the same time, on the basis of the RFID data collection terminal, a workshop-level production execution management system with a software basic platform and a series of application modules can be developed with the tracking of materials and work-in-progress as the core. In the design process of the system, through the design of data modules oriented to “individual” or “batch” levels, the traceability and tracking of materials and work-in-progress will be realized in real time, accurately, meticulously, and efficiently. This is the core to establish individual products. Level of real-time archives. Apply RFID, MES, network technology, etc. to production management and control, accurately, real-time, and comprehensively reflect the status information of the production process, effectively and agilely guide the industrial process, form a good complement to ERP, promote the construction of “transparent factory”, and promote production and management And the optimization of the organizational structure to promote the realization of the production model.
The production plan and process are directly transferred to the process and equipment, directly instruct the equipment processing, prevent cross-process processing, and reduce process errors; the real-time data collection allows timely plan assessment and real-time monitoring of production progress; each workshop functional department can share production data, Understand the production progress of related processes to facilitate production coordination. Accurately confirm delivery time and realize batch management; Process feedback correction: Correct process errors in time and shorten process correction cycle; Processing data effectiveness, reduce manual input and paper transfer; facilitate quality traceability; Intelligent Kanban: complete quality information collection and quality Analysis; extended logistics management: RFID batch number-barcode-product; and the RFID data collection terminal used in the workshop site is used to provide the system with information about materials, products, equipment status, personnel information, etc., to achieve system and specific Operator’s two-way communication.
2.2 System Architecture
Construction of overall architecture and system model: Through in-depth analysis of network architecture, factory equipment, communication routing, software and hardware combination, and system scale and performance, establish the hierarchical relationship between monitoring system software and data acquisition hardware equipment, and determine each functional module The division of modules and the interfaces between modules complete the construction of the overall architecture. Fully consider the system’s integration, configurability, adaptability, scalability and reliability;
Software platform architecture construction: Based on object-oriented design technology, distributed network, and various advanced database and configuration technologies, build a system software basic platform suitable for real-time, on-site, and remote monitoring, easy to expand and modify, and fully reflect the orientation The system application integration of discrete objects supports real-time activities and realizes the combination of management and control based on on-site management rules and comprehensive management knowledge. It mainly includes the construction of software system function positioning, platform selection and data collection, data storage, network applications, client query and browsing;
2.3 Operation of RFID production management system
The implementation of RFID production management system operation process has the following functions and advantages:
Automatic collection: can automatically collect materials, work in progress, workstations, and personnel information without contact;
Information query: can query production plan, production process, product batch and other information;
Information input: equipment status information, processing quantity, processing status, quality information, etc.;
Resistant to harsh environments: it has the performance of moisture-proof, oil-proof, lightning-proof, electromagnetic interference and heat-proof.
2.4 Operation process of RFID logistics management system
3. System module
Specific software development of functional modules, including:
Production process modeling/production planning and production management/field data collection/material tracking query/work-in-process tracking query/product life cycle archives
Quality and performance analysis query/Internet application
Workflow research: design workflow models and network data flow planning, support various control and communication strategies, support various workflows in the production process, and realize automatic driving, recording, tracking, analysis, and information sharing of manufacturing production and management processes, etc. , And easily integrated to achieve seamless integration with ERP, MES, etc., forming a smooth channel for information flow;
Device communication and integration and data interface technology: standardize different industries, different types of monitored devices and system interfaces, including digital or analog sensors, programmable logic controllers (PLC), direct digital controllers (DDC), control actuators, video Like devices; research on data formats and protocol conversion methods of various equipment and systems to meet large-capacity, high-speed data storage and access, with real-time and continuous historical data retrieval and playback functions, and provide complex and special data queries ;
The realization of intelligent decision support function: The purpose of real-time monitoring is to provide data for the decision-making of dispatch and operation operators. The system can reflect the production status while having data analysis functions, and then put forward operation plans and suggestions, which is practical.
The biggest advantage of the manufacturing industry lies in its cost advantage. At present, the price of resources, oil, metals and other basic raw materials have risen sharply, which has led to a substantial increase in the cost of manufacturing raw materials. The situation of energy and environmental protection is severe. Green environmental protection, energy conservation and emission reduction have become the current government’s importance to enterprises. One of the assessment indicators, the appreciation of the renminbi directly affects the export costs of manufacturing companies. The promulgation of the new “Labor Contract Law” has further increased the labor costs of enterprises, and the overall economic growth of the periphery has slowed down, and even local recessions have led to continuous overall demand. reduce.
4 RFID production management system hardware configuration
4.1 RFID electronic tag reader
4.2 Independently design customized perception/comparison detection data intelligent command reader to read and write electronic label controller
4.3 Self-designed and customized integrated RFID reader, intelligent command and automatic printing bar code automatic labeling machine
4.4 Independent design and customization of integrated RFID readers, intelligent command, automatic printing of barcodes, automatic labeling machines and other large-flow communication gateways
4.5 RFIDelectronic label(User-supplied)
4.6 System data server and application server (user-supplied)
5 System configuration table
6 Part of case sharing related to RFID production management
7. The effectiveness of the implementation of RFID production management system
1. Save labor: According to the user experience of successfully implementing the RFID management system, it is expected that the labor can be reduced by 15-21%;
2. Reduce the cost of direct salary expenses: According to the user experience of successfully implementing the RFID management system, it is estimated that the salary expenses can be reduced by 9-15%;
3. Reduce the error rate: According to the user experience of successfully implementing the RFID management system, reduce the error loss by 5-10%;
4. Improve production efficiency: production, warehousing and loading and unloading capacity have maintained steady growth; the average finished product processing efficiency has increased by more than 50% compared with the same period; the highest finished product processing efficiency has exceeded 100% compared with the same period.
8. Service Commitment
After-sales service commitment:
The normal operation of the maintenance system shall be responded to and maintained 7X24 hours within three years after the sale.
[ad_2]