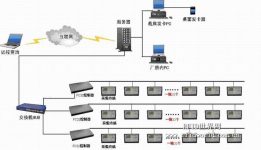
Application case of RFID technology in a furniture manufacturing
[ad_1]
As we all know, the difficulty in the management of manufacturing enterprises is the management of the production site. Companies often rely on experienced managers to collect on-site data through manual statistics. In this case, the requirements for managers are high, the accuracy and real-time of information are low, and a lot of manpower and material resources are wasted. This backward management method is a bottleneck restricting the development of enterprises.
With the popularization of informatization, companies have begun to use bar code piece counting to collect data on the production site. On the basis of manual piece counting, the level of informatization of the company has been improved. However, the bar code management method has its own weaknesses that it cannot overcome, such as: information cannot be real-time, usually at least one day behind; limited information capacity, unable to monitor the situation of each process; unable to reflect the production situation of each employee, and responsibility cannot be assigned to individuals. It is difficult to reduce the defective product rate; the production bottleneck cannot be predicted, and the overall control cannot be performed; it is necessary to have a dedicated person to print and scan the barcode, which wastes manpower; the paper and ink cannot be recycled, and the long-term use cost is high. In addition, barcodes have high requirements on the application environment, and cannot be polluted, damaged, short reading distance, and cannot be read in batches.
The integration of enterprise information resources and the realization of digital management are the keys to the industrial upgrading of manufacturing enterprises. Yiwei Furniture Co., Ltd. is a leading enterprise in Heshan furniture manufacturing. It has always hoped to effectively integrate corporate information resources, especially real-time production data. However, the factory has heavy environmental pollution, many processes, and a large number of production employees. Obviously, bar code methods cannot be used. Meet the management needs of furniture manufacturing.
In this case, Heshan Yiwei Furniture Co., Ltd. and Dongguan Yishili Technology Co., Ltd., through in-depth discussion and technical exchanges between the two parties, creatively applied RFID unlimited radio frequency identification technology to the furniture production field successfully, conquering the production site in one fell swoop Management is difficult and information feedback is not timely, and a bridge of communication is built between the management and the production line.
In the overall design of the program, the data collector and electronic tags of Yishili Intelligent Technology are used to realize real-time data collection for each process.
RFID system architecture diagram
Using a tree-like network connection, each controller can be connected to 32 data collectors (hereinafter referred to as readers), and the readers do not affect each other. And the controller supplies power to the reader online, and the reader does not need an independent power supply. Managers can grasp the factual production situation of the entire factory and a large amount of production materials through the network.
System application process
1) When the worker inserts the employee card into the reader after going to work, the system shows that the machine is online;
2) Insert the number card that represents a certain process, the worker starts production, and the system shows that the machine is in working condition;
3) After the process is completed, the worker pulls out the number card from the reader, and the system obtains the production quantity and production hours;
4) Follow-up processes are transferred in turn, complete data collection of all processes of the product, and record the time used in each process and the name of the production employee, and the responsibility is assigned to the person;
5) The number card is automatically recovered and transferred to the next work order through the card issuance flow.
The whole process is easy to operate, no need to make major changes to the current operation mode, and workers can use it proficiently in only 10 minutes of training.
Hardware product introduction
(1) Data collector
Data collector L33
Project L33
Dimensions (length * height * width) (unit: mm) 148mm*85mm*35mm
Card reading distance 40mm
The card reading mode is compatible with both inserting and swiping modes
The power supply adopts network cable for centralized power supply, no independent power supply is required
Power is less than 1W
Communication method RS485
Card read and write time is less than 5 seconds
Working frequency 125KHZ
The transmission distance can reach 100 meters with one controller and 32 intelligent terminals
Working environment temperature 0℃-50℃
Relative humidity of working environment 10%-90%
Number of keys 16 (function keys)
Display size 128*64 dot matrix
32 characters can be displayed (can be flipped)
At present, our company has four products of this type, and customers can choose according to their specific needs.
(2) FC32 controller
FC33 controller
Project FC32 Controller
Dimensions (length * height * width) (unit: mm) 440*208*44
Weight (g) 2370
Port 32 485 ports
1 TCP/IP port
Power supply adopts AC power input
180-240V AC; 50/60Hz
Power 120W
Communication method RS485, TCP/IP
Transmission distance
(Unit: meter) 90
Transmission rate 9600
No fan
Working environment temperature 0℃-50℃
Relative humidity of working environment 10%-90%
The value of all aspects after the application of RFID
(1) In terms of workers:
Through RFID real-time data collection and the reform of worker performance appraisal, the goal of workers’ self-management is achieved, thereby doubling the efficiency of workers. Efficient workers can get higher wages and reflect the principle of fairness. RFID helps companies find good workers, retain good workers, and attract good workers. The process card can only be read once in the same process, eliminating worker fraud and realizing accurate collection of time and quantity. Data is transparent, and employees can know the individual piece count at any time. Combined with performance appraisal, it effectively stimulates the enthusiasm of employees and enables employees to manage themselves, thereby reducing the difficulty of factory management.
(2) Middle management:
Know the production progress of each process, reasonably balance the production line, and maximize the production capacity of the production line. Know the working status of each worker, and conduct personalized management for each worker based on data. The factory’s requirements for the experience of middle-level management are reduced, and the capacity of the entire production line is no longer affected by the level of a certain middle-level ability, so that the middle-level management ability is transformed from experience to knowledge and data.
(3) Production management:
Managers no longer need to go to the workshop to understand the production progress of the entire factory, saving valuable time. To clearly understand the production bottleneck, it is only necessary to require workers to work overtime in the process where the work-in-process is blocked, and other workers may not arrange overtime, thereby reducing wage costs.
(4) Equipment management:
Equipment asset management makes the factory’s machinery and equipment clear at a glance. Be clear about the operation and usage of each production equipment, and plan the investment of production equipment reasonably.
Benefit analysis of Yiwei furniture after using RFID
(1) Staff reduction
Automatically collect data on site, thereby reducing on-site management personnel and saving manpower.
(2) Efficiency improvement
With timely information feedback, the management can quickly make decisions, effectively eliminate production bottlenecks and balance production capacity.
(3) Quality improvement
Responsibility is assigned to individuals, which reduces the defective rate of products, saves unnecessary loss of raw materials, and improves product quality.
(4) Facilitate production scheduling
After the RFID system is introduced, the machine utilization rate of the production workshop and the actual production efficiency of the workers can be counted, which is convenient for timely adjustment of production scheduling. Cycle time is shortened by 18%. Corresponding reduction in production loss can be up to 10%.
(5) Standardization of management
Scientific and standardized management, fairness and justice, avoiding conflicts between employees and management.
(6) Enhance corporate image
Modern management tools enhance the image of the company and are an incentive for all employees and help the company develop healthily.
At present, Heshan Yiwei Furniture Co., Ltd. has fully used RFID system for production site management, which is a milestone in the field of furniture manufacturing. With the development and popularization of RFID technology, more companies will apply this technology. To be sure, RFID technology will accelerate the industrial upgrading of my country’s traditional industries.
[ad_2]