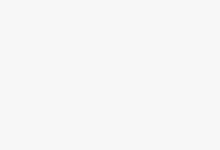
Application case of sportswear intelligent unmanned finishing system
[ad_1]
A few days before the most magical festival on the planet, “Double Eleven”, the online promotion war has long been “smoke of gunpowder.” The chopsticks are accumulating great power and preparing to buy, buy and buy. As the highlight of the “Double Eleven” over the years, the sales of apparel products have been far ahead.
With more and more garments “made in vietnam”, the editor today takes everyone to see how the HUGO BOSS, ADIDAS, PUMA, etc. of this Vietnamese foundry can achieve rapid “shaping” and “sorting” .
After the sewing link of the production line is completed, the inspector hangs the qualified clothing on a special hanger, and the garment to be ironed will be automatically transported to the “magic tunnel” to complete the automatic “shaping”, and then automatically sort to the designated location for packaging …
After 40 days of installation and commissioning, at the end of October, the intelligent unmanned finishing system for sportswear, independently developed and designed by Shanghai Weishi Machinery Co., Ltd., was put into use in Ho Chi Minh City, Vietnam.
The purchaser is the most well-known apparel manufacturer in Asia, which mainly manufactures for first-line sports and leisure brands such as HUGO BOSS, ADIDAS, PUMA, REEBOK, etc. It has production bases in Vietnam, Cambodia and Zhongshan, Guangdong, and employs more than 10,000 people.
There are 23 production lines in the workshop where the project is implemented. Before the introduction of the smart unmanned finishing system for sportswear, each line is equipped with two irons, using the traditional model of “iron + ironing table”. Work, labor intensity is high, work efficiency is not high.
In addition, the air humidity in the natural environment in Southeast Asia is high, and the steam pressure in clothing factories is generally low, and the steam sprayed by irons has high water content. When many clothes float across the ocean to reach customers, they are prone to dampness and even mildew. Circumstances affect the quality of clothes, and it is also easy to cause serious consequences such as complaints from customers who placed orders, and even cancellation of compensation orders.
In response to the customer’s production problem, Visa has designed this intelligent unmanned finishing system for sportswear based on RFID Internet of Things technology according to local conditions. This system is made up of the HGX-Q9000 tunnel finisher (currently widely used in the automatic finishing field of sports, leisure, fashion and other products), the “star” product of Visa, combined with intelligent conveying, dynamic temporary storage system, and belt It is composed of special clothes hangers with RFID chips, which fully realizes the automatic, intelligent and efficient finishing mode. While greatly increasing the output, it reduces labor intensity and labor input, realizes unmanned production, and solves the problem of “drying and moisture-proofing”.
The computer system can also monitor the production capacity of the workshop site and the production efficiency of the sewing line in real time, which greatly facilitates the manager to control the production situation of the factory.
The whole system can handle up to 1500 pieces per hour (25 pieces/min). The 23 sewing lines saved a total of 46 ironers and 23 packers, and shortened the layout of the lines. “We compared the humidity of the finished product before and after the process improvement, and the qualification rate of the three-dimensional ironing product reached 100%. Moreover, after the use of RFID automatic identification and sorting technology, the clothes of each group will not be confused, and the production efficiency is greatly improved. Improve. We are very satisfied, and will be fully promoted in other factories and workshops one after another.” Customers who use Weishi’s “intelligent” products greatly appreciate the product.
According to Weishi, the core of this system is the control program, which can realize the “line-to-line” efficient production mode according to the actual production needs of customers. Even if the progress of each production line is different, after the automatic ironing process is completed, every time The garments produced on the sewing line will be intelligently sorted to the designated location without any confusion. Solve the problem of “fighting” that was easy to occur in the process of inserting orders and changing money.
[ad_2]