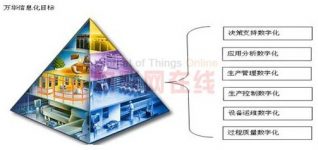
Application of GE Smart Platform Solution in Smart Factory Construction
[ad_1]
1. Project background
Yantai Wanhua Polyurethane Co., Ltd. is a joint-stock listed company. Our company is a leading domestic MDI (diphenylmethane diisocyanate) manufacturer and the largest MDI manufacturer in the Asia-Pacific region. Mainly engaged in the research and development, production and sales of MDI-based isocyanate series products, aromatic polyamine series products, and thermoplastic polyurethane elastomer series products. The product quality and unit consumption have reached the international advanced level. The company, as always, shoulders the historical mission of developing China’s polyurethane industry, actively responds to the country’s call to develop a circular economy and create a conservation-oriented society, takes the industry to serve the country as its mission, implements an international strategy, and is committed to creating a world-class new chemical material company.
At present, the company has three production bases in Yantai, Ningbo and Dongguan. This MES project is based on the construction of the second phase of the Ningbo production base, and at the same time centered on the idea of ”building a first-class chemical production base”. Through the construction of the Ningbo Wanhua MES project, the production process management and business systems are closely integrated, according to the MES standard model , Combined with the GE intelligent platform to comprehensively develop and integrate existing resources, realize data acquisition, processing, storage, utilization and management in all aspects of production management, forming a production command, process control, quality assessment, equipment monitoring and guarantee, and abnormalities A unified production management platform with comprehensive capabilities such as early warning and detection, retrospective analysis, performance evaluation and decision-making judgments will gradually realize the digital and intelligent transformation of Ningbo Wanhua’s production process, and gradually realize the transformation of production from passive command to real-time scheduling. The transition from random inspection to online control, the transition from passive supply of resources to active supply, the transition from post-accounting to process control of costs, improves production efficiency, guarantees production quality, reduces production costs, and enhances the competitiveness of enterprise chemical products.
2. Construction goals and requirements of Wanhua MES project
2.1 The general goal of IT construction of Wanhua Smart Factory
2.2 Target requirements for this period
Based on Wanhua’s MES application, through Ningbo MES Phase II, a stable and reliable integrated data integration platform with unified standards and rapid replication of factory applications will be established, and a solid foundation will be provided for the group company to require centralized factory data headquarters. The platform will start from the establishment of information integration, realize the key transaction processing of the enterprise value chain, and finally provide beneficial help for intelligent production. At the same time, as the middle layer of the enterprise’s three-tier model, it effectively undertakes the bridge relationship between the production process layer PCS and the management management ERP; it combines general MES functions with lean production to build a lean MES platform. The system platform should have good scalability, and it can be extended well on this platform in terms of depth and breadth. For example, in terms of depth, each part can be used as a separate small module to enable development, The application is more in-depth; at the same time, in terms of breadth, new modules can be added.
2.3 Implementation scope of the current period
The construction scope of the second phase of MES in Ningbo includes: the second phase of Ningbo Wanhua Industrial Park (MDI, coal gasification, nitrobenzene, electrical) and finished product packaging and related public works.
2.4 Goal description
In this phase of MES project, based on the overall construction goals of Wanhua Intelligent Chemical Factory, combined with the reality of the Ningbo factory, it will realize closed-loop execution of production plans, production monitoring, production scheduling optimization, material genealogy tracking, material and public engineering balance, process quality management, and equipment Operation and maintenance management, performance and cost management, document management and other nine types of major goals, the requirements of each goal are as follows:
Closed-loop production plan tracking: Realize the closed-loop execution of the plan from SAP to MES to the site, and report the factory’s plan execution in real time.
Production monitoring: real-time information monitoring of production status, which can monitor the operating parameters of the factory based on C/S and B/S. These parameters include but are not limited to process data, equipment operating data, HSE data, alarm data, etc.
Synchronous scheduling optimization: Combining scheduling strategies, material balance, various constraints, and various events to calculate the optimal scheduling in real time.
Material batch tracking: to realize the process tracking and event playback of each stage from the finished product to the production state.
Material balance: Calculate the material balance of the second-phase device and process to achieve the purpose of dynamic cost control in the production process.
Process process quality management: real-time calculation and reporting of OEE, CP, CPK, PP, PPK and other indicators of the production process.
Equipment operation and maintenance management: equipment OEE, downtime rate, real-time status monitoring of equipment, automatic generation of equipment operation and maintenance reports, etc.
{$page$}
Performance and cost management: Through event-driven KPI calculation, KPI changes can be reflected in time at any time.
Document management: Establish a document management module according to the process, and browse related documents in real time (operating procedures, process indicators and other related documents) according to the user’s authority and the node of the process.
Three, the solution
3.1 System architecture
During the business inspection phase of this issue of MES system, more than 10 well-known chemical system suppliers at home and abroad, including Siemens, Honeywell, HP, Emerson, OSI, Rockwell, GE, etc. were investigated in detail. Finally, GE was selected as the partner of this MES project. GE’s smart platform solution package impressed me the most with its platform-based and lean design ideas.
Combining specific needs, combined with GEIP, we can easily build a good system architecture.
3.2 Specific implementation plan
Combining Wanhua’s nine major goals, after repeated discussions by the project team, the specific implementation content as shown in the figure above was finally determined.
Fourth, the implementation process
Wanhua’s MES project has now entered the system realization stage after blueprint design. The entire team has already passed the running-in period. Although there are problems of this kind during the implementation of the project, the whole team has unified thinking, clarified goals, and gathered strength. I believe that in the foreseeable future, Wanhua’s smart factory based on GE’s smart platform will surely take the first step.
{$page$}
V. Display of some functions that have been realized
Sixth, the vision of the smart factory production system model
With the functional support of the intelligent platform, the implementation of the MES system opened the first step for Wanhua to build a smart factory. From energy saving, emission reduction, consumption reduction, efficiency increase, intelligent production optimization and other aspects, Wanhua has brought value-added ROI.
[ad_2]