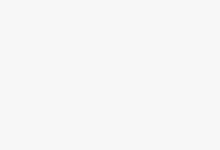
Application of IoT remote service in XCMG Group
[ad_1]
In May 2010, a service vehicle of an office of Xuzhou Construction Machinery Group Co., Ltd. (hereinafter referred to as “Xugong Group”) was stolen at 1 am. The staff of the monitoring center of the Xugong branch happened to see the abnormal movement of the service car on the surveillance big screen: the service car started at 1 am and was driving towards Xi’an. Then the staff of the monitoring center immediately called the police and assisted the local public security personnel to inform the service vehicle in detail which road to follow. Soon, when the two thieves got out of the car, they were caught by the police.
The use of this Internet of Things technology is also being recognized and accepted by XCMG customers. The omnipresent remote service drives XCMG’s industrial upgrading and also leads the transformation of the engineering equipment industry to intelligent equipment.
“Clairvoyance” monitoring
The rapid detection of the car theft in this office of XCMG Group is based entirely on the use of remote monitoring technology, which is the use of global satellite positioning technology (GPS), wireless communication technology (GPRS), and geographic information on XCMG products. Technology (GIS), database technology and other information technologies are finally realized by collecting and analyzing data such as the geographic location, movement information and working status of the vehicle and sending it to the police.
In the plan to realize the application of the Internet of Things technology, Xugong Group is to use the Internet of Things technology to realize 24-hour online real-time positioning and tracking and health monitoring of in-service equipment in various places, monitor the operation status of equipment and machine performance changes, and predict the occurrence of early warning accidents. , When failure occurs, it will promptly report to the police and change passive maintenance into preventive maintenance.
The reality is that although more construction machinery and equipment have realized the automatic alarm function for a long time, they have not yet realized the remote alarm function. Many devices have intelligent functions, but because they are not equipped with relevant data output and input systems, the Internet of Things has not yet formed.
The visual monitoring platform of XCMG Group is composed of geographic information system (GIS), management information system (MIS), fault diagnosis system and maintenance service system to realize real-time positioning, tracking and historical trajectory playback of XCMG equipment; construction machinery Information management and operation status information query; fault diagnosis and early warning and fault log query; maintenance reminder and maintenance log query.
Most of the customers of construction machinery companies are individual bosses, and XCMG is no exception. If construction machinery companies provide leasing services—allowing more users to purchase their own equipment through financial leasing is the first step from production-oriented manufacturing to service-oriented manufacturing, then providing remote monitoring, testing and diagnosis is engineering machinery The most important step towards full-service manufacturing.
However, because of this flexible method of financial leasing, many construction machinery companies are caught in a dilemma. Zhang Qiliang said: “Some users don’t pay after they ship the equipment. We used to have a dedicated department to deal with the huge amount of bad debts and bad debts every year. After the product is installed on the GPS system, if the user does not pay within the specified time limit. If the account is paid off, the device will automatically lock up.”
The use of remote monitoring to manage funding issues has had a good effect. Zhang Qiliang said: “In 2010, our collection was very good, and we paid back on time.”
However, this is not the main content of remote service, which is more about after-sales service of products. At the customer service center of Xuzhou Heavy Industry Co., Ltd., a subsidiary of XCMG Group, you can see a large screen wall as soon as you enter the door. There is a two-dimensional map of China on it, with four data frames on the left and right. The two-dimensional map shows the location of the product. Zhang Qiliang said that XCMG’s current positioning vehicle can be accurate to about 15 meters, and the frequency of updating data is every 10 seconds.
The dialog box displays the monitoring data of a device you want, including vehicle-related information of operation type, detection type, and control type. Through the real-time working parameters of the equipment and the intelligent analysis and monitoring platform, the customer service center provides active services, corrects customers’ irregular operations through phone messages, etc., reminds necessary maintenance operations, and prevents malfunctions.
[ad_2]