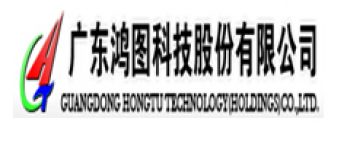
Application of Quality Traceability System in Guangdong Hongtu Nantong Final Co., Ltd.
[ad_1]
【Customer Profile】
Guangdong Hongtu Technology Co., Ltd., established in December 2000, is a leading enterprise in the domestic die-casting industry, the largest professional manufacturer of precision aluminum alloy die-casting parts in South China, a high-tech enterprise in Guangdong Province, and the only provincial-level precision Die casting engineering technology research and development center. The company is qualified as a national auto parts export base enterprise, and has passed ISO14001, ISO9000, ISO/TS16949 and other international quality system certifications. On December 29, 2006, the company’s stock was officially listed on the Shenzhen Stock Exchange.
【system introduction】
Shenzhen Jiukun Information Technology Co., Ltd. provided Guangdong Hongtu with a digital execution system for workshop manufacturing. This system is seamlessly connected with Hongtu’s existing UF ERPU9 and manipulator equipment; from process flow, planning management, production operations, quality management, Modules such as equipment management and warehouse management. Realize the real-time collection and response to the workshop production data, completely solve the problem of poor workshop information and difficult control, greatly increase the production plan achievement rate, shorten the production cycle, and increase the production capacity.
【value of customer】
1. Production scheduling, real-time management and control: timely delivery of production scheduling information to the workshop site, efficiency increased by more than 85%; rapid collection and sorting of on-site data (such as output, yield, number of products in progress, etc.), real-time improvement of 99%, efficiency improvement of 85 % Or more; real-time grasp of on-site production and processing conditions and quality conditions, real-time improvement of 99%;
2. Production process control: on-site process control to prevent process errors, foolproof and leak-proof, and reduce 70% of errors; rework on-site control and query functions, improve on-site control capabilities, and increase timeliness by 60%;
3. Production visualization management: use efficiency kanban to provide on-site visual management, and timeliness is increased by 99%; various statistical analysis reports of the manufacturing process are automatically generated, timeliness is increased by 99%, and efficiency is increased by 95%;
4. Traceability management: establish a unified product quality traceability information system to provide fast and comprehensive after-sales product traceability, including materials, processing history, quality information, etc.
5. Equipment docking management: through communication with the manipulator and laser marking machine, the laser marking machine is controlled to automatically engrave a QR code on the part. At the same time, it collects the process parameters of the die-casting machine and the leak test machine in the production engineering to provide a data source basis for the analysis of the production process.
[System case icon]
[ad_2]