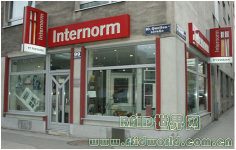
Application of RFID in Internorm door and window products
[ad_1]
Austrian manufacturing company Internorm uses RFID to track the movement of containers loaded with doors and windows in its three manufacturing plants. The RFID system cancels the previous manual tracking of containers, avoids manual errors, makes more use of containers, and also reviews the accounts of third-party trucking companies and sales partners hired by the company.
Internorm’s door and window products are not sold directly to end customers, but more than 900,000 sets of doors and windows are sold annually through more than 1,000 sales partners and distributors. Because doors and windows are fragile items, every time they are handled, they may be damaged. Therefore, the manufacturer adopts a set of just-in-time production processes to reduce inventory and improve quality (just-in-time production process, abbreviated as JIT, refers to the establishment of efforts to eliminate everything A production concept based on waste and continuous improvement of productivity. It covers a complete set of production activities from product design to delivery of finished products. As long as these activities are required to produce a final product, including each work-in-process starting from raw materials During the production stage, we must align with the goal of eliminating all waste and continuously improving productivity). The company uses 800 containers to deliver products to customers, and takes back the containers within one month.
Internorm, the largest door and window assembly plant in Austria and the fourth in Europe
In the production process, each door and window is affixed with a bar code. The label is encoded with a unique serial number, which corresponds to the description information of the article in the database. Before loading doors and windows into containers, workers scan barcodes and update the records of the logistics planning software, such as which items are placed in which containers.
Before the company installed the RFID system, the factory doorman had to manually record which containers left or entered the factory. Other workers then enter these manual records into the database to get a comprehensive understanding of the location of vehicles, containers, and goods.
In 1999, Internorm began looking for a better solution, according to Alexander Stroh, the company’s RFID project manager. “We want to understand the correspondence between trucks and containers,” Alexander Stroh explained. “In this way, if there is any damage, we can be specifically responsible.” In some cases, Alexander Stroh said, the trucking company may report Load containers that they haven’t actually shipped.
In the following year, Internorm installed the current RFID system, which uses semi-active 2.4 GHz RFID tags, plastic packaging, and Siemens chips. The battery of each label can be guaranteed to work for 5 years, and Stroh claims that most of them can run for 7 years. The system uses 800 tags and two readers are installed at the gate of each factory. One reader reads the incoming container, and the other reads the out container. The reader is installed on a pole about 1.3 meters high, and the shell is plastic-encapsulated to prevent rain and snow.
Internorm’s 40 daily delivery trucks also use semi-passive tags. When the truck approaches the gate, the reader activates the truck and container tags. The tags then send their ID numbers (the only information stored in the tags). After the ID number is verified by the database, the gate will release the truck, and the system will record the entry or departure of the truck and the materials it loads. The gate computer then updated the record of the location of the goods in the Internorm logistics software.
When Internorm installed this system in 2000, the reading distance of passive tags on the market was only half a meter, which did not meet the requirements of practical applications, so the company adopted semi-active tags. Although the company did not evaluate ROI, Stroh said the system saves a lot of labor.
Internorm plans to continue to use the RFID system, but will no longer purchase the tags used in the original system. Since some batteries with old labels are almost obsolete, and the company also needs to label new containers, Internorm uses about 60 new labels every year. The company is currently negotiating with two new suppliers.
By May of this year, the company will replace the 8-year old system and replace it with a new EPC Gen 2 system. Internorm estimates that the replacement will be less than $74,000, including all necessary readers, tags and software.
As the RFID system has brought good benefits to Internorm, Internorm said that the company plans to introduce the technology into the production line within 10 years. In addition to the ID number, the label will also store the production information of the product.
[ad_2]