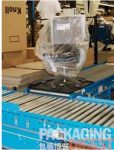
Automatic identification system makes furniture production smoother
[ad_1]
Knoll Mfg., an office furniture manufacturer in East Greenville, Pennsylvania, is universally recognized for creating “inspiring, mature, and lasting” office furniture. The innovative and modern design promised by the company has produced a wide range of benefits in office systems, chairs, files and storage, work tables and desks, wooden box products, textiles and accessories.
The new system replaces the old way
Recently, Knoll has added a material handling/order tracking system to its office chair products and packaging business, which can greatly reduce cutting costs, eliminate order processing errors, and speed up the transportation process. The system combines radio frequency identification (RFID) technology, barcode technology, and equipment from Accu-Sort Systems (www.accusort.com). Stokes Material Handling (www.stokesmhs.com), which is involved in coordinating the project, has a new conveyor belt and processing. Device, and BP Controls (
www.bpcontrols.com
) The company’s system software, controllers, scanners and other components. Knoll’s production plant in East Greenville has a chair production building, which contains four office chair production lines that produce its Chadwick, Life, RPM® and Bulldog® brand furniture.
In order to be able to transmit downwards and track correctly, the fully assembled chair wrapped in the film, as shown in the above picture, will be placed in a reusable, attached to a “license plate” that can be used throughout the entire In the plastic tray of the RFID tag that identifies the chair in the factory. The tag utilizes an RFID tag writer/reader for encoding.
In the past, after the chair was assembled, tested and perfected, a production label containing the shipping date, routing code, box/pallet number, order type and number, item number and product quantity was manually labeled and attached.
The chairs are then wrapped in a protective film or loaded into a shipping box, with a maximum of 4 chairs on each pallet.
Then, the pallet is stowed into one of the three Knoll “mixed” or inventory centers in the transportation area about 1,000 feet away from the building, where the chairs may be combined with other office furniture for shipment.
This kind of operation keeps the factory busy, and forklifts shuttle back and forth in the factory’s production and transportation areas. This has raised many concerns, including forklift maintenance and fuel costs, and warehouse safety, according to Knoll. But the biggest concern is the integrity of the order. Chairs may be accidentally sent to the wrong inventory area, causing major transportation errors or delays.
In order to reduce traffic problems and simplify the order tracking process, Knoll contacted Stokes Material Handling to develop an automated material handling system with the following functions:
· Identify chairs by order number, purchase number and their destination.
· Automatically transport the chair to the correct classification area.
· Automatically guide the cargo to enter the correct gate.
Stokes Material Handling provides the latest conveyor belts (including those from Hytrol [www.hytrol.com]Those) and automated chair lifts to make the new process more convenient, as well as Accu-Sort’s recommended RFID system and BP Controls controllers to create a new way of tracking. )
Easily deal with two packaging methods
Now, Knoll specifies that the chairs are either packaged (carton packaging) or wrapped (film wrapped). A packed chair will be packed into a two-piece corrugated shipping box, with detailed production information on the label, including product information and description of the chair, customer identity, order number, and single product number.
In order to optimize the use of trailer space, Knoll has also recently improved its packaging chair product line, so that 80% of the products are disassembled and transported, that is, the bottom of the chair and other components are separated.
Then, all parts of the chair are packed in a smaller box. However, the wrapped chairs are fully assembled, so they cannot be transported in the same way. Instead, it was wrapped in a transparent film when transported, shipped out of the factory and transported vertically.
When the chair is produced, the production department uses a desktop printer to produce a bar code, which contains information about the chair, including the destination mixing center (or direct transportation). The label affixed to the front of the box on the packing chair can be easily scanned by a scanner at a fixed position on the conveyor belt.
However, the label affixed to the film of the wrapped chair, because the chair can rotate up to 360 degrees, poses a challenge for barcode scanning, because the position of the label on the wrapped chair cannot be fixed. Therefore, the wrapped and assembled chair will be placed on a reusable conveying tray, so that it will be easier to convey down the packaging production line.
Knoll recognized that the transfer tray would be an ideal application for radio frequency identification (RFID) tags. Each pallet is equipped with an RFID tag wrapped in plastic provided by Accu-Sort and fixed to the pallet with Velcro®. When the chair is conveyed downstream in a closed circulation system, it is easy to read the information on the RFID pallet label that acts as a kind of “license plate”.
The label is placed on the center point of the square pallet, making positioning a problem. Every time when the pallet receives a new chair, the RFR-02 FRID label reader/writer from Accu-Sort will be on the label. Write the new order information. Once the chair reaches the end of the production line, the pallet is brought back to the starting point of the production line. When the pallet is loaded with another chair, the label is overwritten with new information.
Separately guide the two packages
Any of the 4 production lines can handle wrapped and packed chairs. At the end of each chair production line, the chair enters what Knoll calls a “guidance area”, which contains an RFID station to “guide” the chair into Knoll’s computer system with chain transfer and integrated control logic.It is equipped with a button with a transfer button designed by BP Controls
, A handheld scanner, a secondary signal light and a small console composed of an Accu-Sort RFR-02 RFID tag reader/writer.
A fixed-position high-frequency tag reader/writer compatible with the ISO 15693 standard uses a frequency of 13.56 mHz to read and write Knoll’s passive tags (RF electronic tags). The HF reader/writer system has a 5×16 inch antenna and is designed for factory automation control, automatic material handling and asset identification. Each main RFID/guidance area is also equipped with an automatic elevator made by Stokes Material Handling, allowing the operator to either transfer the film-wrapped chair to the transfer tray, or pack the chair to the corrugated loading on the ground In the container.
When the chair reaches the guide area, the staff will determine whether to pack or wrap by checking the work order number that matches the chair.
In the case of packing chairs, the staff moves the button on the console to the packing position, puts a box on the elevator, puts the chair in the box, and seals the box before pressing the “transmit” button, so that the chair You can continue to move downstream. Scan the labels on the packaging with a handheld scanner from BP Controls, and the box will automatically rise and transfer to the production line.
For wrapped chairs, the staff will move the button to the wrapping position and place a plastic conveyor tray on the elevator. Then turn the chair to the transfer tray and use a handheld scanner to scan the product barcode label on the plastic film cover. Then, transfer the scanned information to Rockwell (www.rockwellautomation.com) Allen-Bradley SLC 5/05 processor/programmable logic controller provided by BP Controls, which can write for RFR-02 RFID Enter the machine to format the same scan information. Next, the RFID writer encodes the information on the RFID tag on the transfer tray.
In the picture above, the RFID stations with consoles and scanners are in their respective positions in the “guidance” area at the end of each packaging line in the Knoll Mfg. production plant.
When writing a label, the signal light of each guide area will flash. When the label writing operation is successful, the signal light turns green, and the elevator automatically raises the chair and unloads it to the main production line. If the label writing fails (misalignment, scanning error, etc.), the signal light turns red and the staff repeats the process. If the label is not written successfully, the system will not guide the chair to the main production line.
When the chairs reach the shipping area, they first pass through a strapping-confirmation area equipped with an Accu-Sort Axiom™ laser barcode scanner and an RFR-02 RFID tag reader. Axiom provides high-speed scans at the fastest rate of 1,400 scans per minute, Accu-Sort said.
After the RFID tag reader detects the label on the transfer tray holding the wrapped chair, it will make the wrapped chair bypass the next strapping station on the production line and head to the sorting area.
However, if the Axiom barcode scanner detects the barcode label on the packed chair box, it will send a signal to transfer the chair from the main production line and pass forward through two automatic strapping machines equipped with EAM-Mosca (www.eammosca.com) In the strapping area, four straps are tied.
The strapping station will position the box so that the front of the box is forward and its product label faces the side. Then, the bundled boxes will be automatically “redirected” or sent back to the main production line, at this time the front of each box faces the same side.
Accurately classify and ship
In the next step, the wrapped and packed chairs will enter the classification area. Here is an Accu-Sort Model 24i DRX with periscope bypass barcode scanner to detect the packed chairs, and use the barcode labels to locate the shipping boxes of the chairs. , There is also an RFR-02 RFID reader/writer to scan and verify the RFID tag on the wrapped chair. The data sent to the sorting computer will determine which outbound product channel will send the chair for shipment. The bypass scanner can scan 3,000 times per minute, with a maximum reading range of 70 inches, Accu-Sort tells.
Then the chairs are tracked and sorted, and sent to the correct outbound transportation channel or loading and unloading platform. The sorting computer identifies products by order number or single product number, and provides detailed channel allocation instructions designated by the mixing center.
Carl Visscher, Knoll’s factory production manager, said that the company is very satisfied with the combined RFID/barcode encoding system, which has helped Knoll increase production and reduce delivery errors. With it, Knoll expects to save $300,000 in direct labor costs and another $200,000 in procurement costs, because the chairs no longer need to be picked up and loaded with a forklift. Instead, they can be delivered directly to the shipping area, enabling the warehouse to achieve a higher utilization effect. Visscher pointed out some other advantages of the system: “The new method greatly reduces the fuel and maintenance costs of the forklift, but also reduces the amount of forklift traffic in the factory and improves the safety of the factory,” he said. “If we choose another type of scanning settings, our investment will be a lot more. We should be able to see the return on investment within 3 years, including the depreciation of equipment, hardware and software.”
[ad_2]