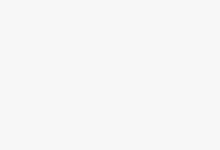
Beijing Shufei Technology RFID aluminum ingot management system case
[ad_1]
Project Background
Oriental Hope is a large private multinational enterprise group founded in 1982, headquartered in Pudong, Shanghai, with feed as its primary business. In 2002, the group selected the aluminum-electricity complex industry as its second main business. In early 2002, Oriental Hope Group invested heavily in the construction of a large-scale aluminum-electricity integration project in Baotou. Oriental Hope Baotou Rare Earth Aluminum Co., Ltd. (hereinafter referred to as Oriental Rare Aluminum) is a wholly-owned subsidiary of Oriental Hope Group, with a total project investment of 9.8 billion yuan. In May 2003, it was listed as a key enterprise in the Inner Mongolia Autonomous Region and was awarded by China Guangcai Enterprise. The Promotion Association is listed as a key project of the national glorious cause.
Due to the late establishment of the factory in the same industry and the relatively complete informatization supporting facilities of Dongfang Rare Aluminum, currently under the guidelines of the factory’s “refined management”, the financial and production departments of the factory have achieved informatization. , But due to the particularity of aluminum ingot production, there is currently no better management plan for aluminum ingots. Through the launch of this RFID project, the aluminum ingots can be bound with RFID tags to realize warehouse management, quality inspection, etc. The automation or even unmanned operation of the links has laid a good foundation for the company to further integrate the information subsystems of various departments.
This software is used as an RFID-based aluminum ingot platform management system. The ultimate goal of its implementation is to integrate RFID technology with Dongfangxi Aluminum’s existing aluminum ingot generation process, and optimize its workflow, using RFID as the integration point to achieve aluminum ingots. Automated and unmanned management. In the process design of the system, the following issues are mainly involved and need to be resolved:
(1) Binding method of RFID tag and aluminum ingot;
(2) The binding cycle of RFID tags and aluminum ingots;
(3) The management method of RFID tags.
Binding method of RFID tag and aluminum ingot
In the production process of Dongfangxi Aluminum aluminum ingots, the smallest unit of aluminum ingot production is roots, but in measurement and management, the smallest unit is bundles. Under normal circumstances, 54 aluminum ingots are bundled into a bundle by steel belts (this The process is called bundling), and in subsequent management, this bundle is used as the unit.
Under the condition of maintaining the existing management of Dongfang Xi Aluminum and the operation method unchanged, choosing to bind an RFID tag with a bundle of aluminum ingots, such management is a better solution.
Binding cycle of RFID tags and aluminum ingots
From the perspective of process optimization, the more departments that a labeled aluminum ingot circulates in the circulation process, the more places where RFID is applied in the production department, and the higher the degree of automated management.
From this point of view, once the aluminum ingots are collected into bundles, they are allocated, the tags are bound, and the label is recycled when the aluminum ingots are out of the warehouse (leave the factory). On the one hand, the application of RFID is expanded (from production) On the other hand, the cost is saved, that is, the label can be bound with the next batch of aluminum ingots after recycling, so that it can be reused.
RFID tag management method
The RFID tag is uniquely identified by its built-in 16-bit ID. Without a reader, it is impossible to know the ID of the RFID tag. This makes the same type of tags look the same on the outside, for management And storage brings great inconvenience. In response to this situation, laser engraving is used to assign a short, easy-to-remember number to each label used, and the corresponding relationship between the RFID tag and the number is stored in the database. When managing, as long as the management is carried out according to the number, the inconvenience caused by the inability to identify the label by human eyes is solved.
Software flow
After various opinions and on-site inspections, the software process is finally determined to consist of the following parts:
Label initialization
That is, the label and the aluminum ingot are bound one by one in bundles. The specific operation method is that when the casting workshop is handing over shifts (24 hours a day, divided into three shifts), the labels of the aluminum ingots to be produced in this shift are initialized by the handheld according to the aluminum output plan.
Hang tags
In the aluminum casting process, for each bundle of aluminum ingots produced, the corresponding labels are hung on the aluminum ingots after the bundling is completed. The production of aluminum ingots is produced by furnace, with batches as the unit. Each batch consists of five to six bundles of aluminum ingots. The same batch of aluminum ingots can be mixed with each other. Therefore, after the label is initialized, you only need to press it It is stored in batches. When labeling, only randomly picking labels from the same batch is enough.
Random inspection
After the label is hung on the aluminum ingot, the casting or quality inspector shall check the label on the aluminum ingot with a hand-held or printed label comparison table to check whether there are any wrong labels or initialized wrong labels to ensure weighing and The subsequent process went smoothly.
Weigh and warehousing
While the aluminum ingots are being produced, the quality inspectors will sample and test the aluminum raw materials. When the test results come out, the aluminum ingots can be weighed, put into storage, and allocated according to the test results.
Out of stock
After the aluminum ingots are weighed and transported to the yard, they can be packaged in accordance with the order placed by the supply and marketing department. The aluminum ingots must be shipped out of the warehouse before the packaging is carried out, mainly by handheld scanning to ensure the accuracy of the information , At the same time, remove the label and perform new initialization work after the outbound operation, bind it to the new aluminum ingot, and enter the next cycle of use.
[ad_2]