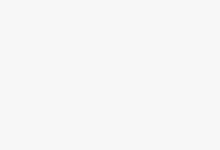
Cases of electrical appliance companies using bar codes to monitor production
[ad_1]
The management of the production process is the soul of an enterprise. The quality of the products of an enterprise mainly depends on the management and control of the production process. The production process refers to the process by which the parts and components in the enterprise finally become finished products. In the stage when there is no application of the bar code technology of the Internet of Things, each product must be manually recorded in each production line. The processes and parts required to generate the product must be manually recorded. After the picker allocates the materials according to this, the production starts. There is a record sheet for each product in each production line. After each process is completed, fill in the component number and the worker’s job number, and the operation is completed. In this process, the workload is very large and complicated, and it cannot immediately reflect the flow of products on the production line.
The production efficiency of a company’s electrical production line is relatively low, which is prone to confusion. After consideration, the company decided to adopt the Internet of Things barcode technology to manage production. After the barcode technology is adopted, the order number, part type, and product quantity number are first formed into a barcode, and the barcode is printed and pasted on the production line of product parts and assembly. In this way, the production process and required materials and parts of a product order on a certain production line can be easily obtained. After the product is completed on the production line, the product bar code and production line code number are scanned by the production line quality inspector after passing the inspection, and the worker’s bar code is scanned in the order of the process (it can be confirmed once and unchanged). For unqualified products to be sent for repair, the cause of the failure (process location) is determined by the repair.
The main advantages of barcode application in production management are as follows:
1) The production process of the product can be reflected immediately and effectively on the production line, eliminating the labor of manual tracking.
2) The production process of the product (order) can be displayed on the computer, and the bottleneck in the production can be found; fast statistics and query production data provide a basis for production scheduling, order placement, etc.
3) For the unqualified products in the inspection, it can record the problems caused by the workers or the parts, and provide a practical analysis report.
The following case describes how an electrical appliance company uses bar codes to monitor production conditions during the production process.
The four main goals to be achieved by the system:
1) Quality tracking: It can track the model (mainboard, power supply or other main accessories) of the whole machine and the main substrate (PCB board), production site, production date, team production line, PCB board version number, engineering change (ECO), batch And serial number and other information.
2) Real-time dynamic tracking of production: The actual production situation can be known from the computer at any time.
3) Customer tracking: The customer’s name, address and delivery quantity can be obtained from the computer at any time.
4) Report function: Provide various management reports for management review.
Develop a specific plan
Bar code automatic recognition technology has the characteristics of fast input speed, high accuracy, low cost and easy operation. In the automated assembly production line and various processing processes, bar codes are used to mark the main components with bar code labels. After being collected and decoded by the barcode reader, the barcode information is input into the database of the computer server. Each machine and main component will have a unique barcode. No matter where the machine is sent, there will be records. If there is a problem, you only need to read the barcode on the warranty card, you can call up all the relevant data of the product in the database, which greatly facilitates the quality tracking and after-sales service of the product.
Barcode design
The system can contain four main databases: system design library, user library, PCB library and complete machine library. Barcode label must contain information: model/logo, production site, production date, production team/production line. Batch number and serial number, and barcode tracking system software can accept different barcode format and size requirements. Barcode labels are respectively used on the PCB board, the whole machine, the packing box and the warranty card.
For example, when designing the barcode format of a PCB board, consider the model, production site, production date, production team, production line, batch number, and serial number.
The most important work of this part is each code, which must be able to reflect the various conditions of the product in a timely and complete manner, and be able to achieve the uniqueness of each component.
The main functions of the barcode management system: system management, PCB board production management, assembly production management, warehouse management and other functions.
[ad_2]