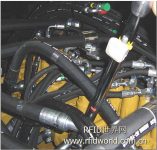
Caterpillar uses RFID to ensure the tightness of the valve assembly
[ad_1]
The world’s construction machinery manufacturing giant Caterpillar adopts a real-time positioning system at its Belgian heavy equipment manufacturing plant to ensure the correct installation of hydraulic valves and hoses. When workers assembled hydraulic valves at Caterpillar’s Belgian factory, they used twist pliers to tighten the pipe (made of rubber and steel) to the valve. The valve-installed on a construction vehicle made by Caterpillar-is the size of a car engine. In order to fix the conduit on the valve and ensure the normal operation of the valve, the worker must use a certain amount of torque-approximately 300 Newton meters-to tighten the bolts. Before the RFID system was adopted, workers had been using twist pliers to manually tighten the bolts, and could not confirm whether the torque reached the correct Newton meter.
Caterpillar uses a set of software system Protrac provided by Belgian industrial software company De Jaeger Automation on the assembly line to track the assembly of each component and the corresponding staff and assembly time. The worker enters his ID code and detailed information about the work to be carried out on the software running on the PC of the container station, as well as the serial codes of the parts planned to be installed.
Before the adoption of RFID, the tightness of the pipe installation could only depend on the judgment of the employees. The employees painted the parts as a mark, and visually checked the tightness of the connection.
The factory has approximately 4,300 workers who build large and medium-sized excavators and wheel loaders. Caterpillar and De Jaeger met in 2008, and Caterpillar project manager Degraux said that the two companies decided to jointly develop an RFID system at an acceptable cost.
In December 2008, De Jaeger installed RFID readers in the main assembly area of Caterpillar’s high-pressure hydraulic valves. This RFID system can work with Protrac software. At the same time, the company replaced manual twist pliers with 6 electronic twist pliers equipped with active RFID tags. Each wrench is designed for a specific loading area and is preset with a specific torque. When the worker reaches the maximum force preset by the valve, the wrench starts to make a ticking sound, indicating that the catheter has been installed correctly, and the applied torque is transmitted to the corresponding PC. By applying RFID tags to each wrench, the real-time positioning system ensures that the correct wrench is used in the correct location.
Use RFID tags on each twist pliers to ensure that the correct twist pliers are used in the correct position
The amount of torque is the key. Degraux said that when the machine is integrated, it will be tested before it is sent to the retail store. If these hydraulic pipes are not really tightened, the leaking valve will not pass the test. “The main goal of traceability in the container area is to ensure the tightness of the valve,” he said. The company not only needs to know whether workers are applying the proper screwing force and using the right tools in the right place.
Now, every electronic twist pliers is equipped with Ubisense label. Only when it is active, each battery-powered 7 GHz ultra-wideband tag sends its unique ID code. When the twister is not working, the tag goes to sleep to extend battery life. A total of 8 Ubisense readers were installed on the ceiling, and the staff adjusted the reading area of each reader to 6 meters * 30 meters. These readers cover 6 production sites, capture the ID code of the wrench’s tag, and then send the ID code to Caterpillar’s back-end system and 6 pallet PCs. The Protrac software determines whether the correct wrench is used in the correct position based on the position of the tool.
Before starting the assembly of the valve, the worker first enters his or her ID code, which corresponds to the relevant data of the employee, including the assembly line authorized by the worker. The worker then uses a bar code scanner connected to the PC to scan the ID codes of the machine parts. The system matches the bar code with the position and ID of the wrench to ensure that the worker uses the correct wrench. The PC screen then displays the execution instructions of the process. If the wrong tool is used, the system will issue an alarm. The green light indicates that the correct wrench is used in the correct position. The yellow light indicates that the red tool is not in the correct container, and the infrared indicates that the connection between the PC and the back-end server is wrong.
So far, the application of this system has been very successful. Most of the valves and hoses were installed correctly during the inspection, and the accuracy was greatly improved compared with the previous ones.
[ad_2]