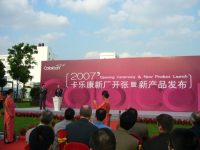
Colorcon’s new plant in China introduces RFID technology to identify materials and control
[ad_1]
Since its establishment in 1961, Colorcon has been committed to promoting the development of the pharmaceutical excipients industry and has become a global leader in this industry. As one of Colorcon’s six production bases in the world-Shanghai Colorcon Coating Technology Co., Ltd. has integrated GMP and ISO quality management systems, from R&D, supply chain management, manufacturing, supervision and inspection, and sales services. Standardize itself in various aspects such as technical services and provide satisfactory services to customers for more than ten years. At present, the company has more than 1,000 domestic customers and hundreds of customers in the Asia-Pacific region.
In order to better serve China’s pharmaceutical excipients industry, Colorcon built a first-class excipient factory in Shanghai in accordance with global standards, which was officially put into use in September 2007. By then, this Asia’s most advanced pharmaceutical excipient factory will become a booster for China’s pharmaceutical industry. Shanghai Colorcon inherits the world-leading quality of its headquarters in terms of software and hardware. It uses global raw materials. All materials are imported from abroad, keeping pace with the United Kingdom and the United States. Colorcon’s 7 factories around the world use the same machines. The same technology, the same quality standards, 100% fresh air, 100,000 cleanliness level, the flow of people and logistics into the clean area by channels. These world-class standards will escort China’s pharmaceutical industry to successfully enter the international market.
In order to meet the continuous upgrading needs of customers, Colorcon has invested huge sums of money to simultaneously upgrade and replace the ERP system globally, use computers for daily management, reduce human errors as much as possible, and adopt the world’s advanced radio frequency identification (RFID) system Material identification and control, so that each material has an ID card, to prevent pollution and cross-contamination; the use of customer relationship management system (CRM) and customer support system (CSS), continuously optimize and consolidate the company’s production and service processes, the largest It has greatly improved the company’s technical service efficiency and created a competitive advantage and development space for customers. Colorcon has also implemented 5S (organization, reorganization, cleaning, cleaning and literacy) management in the office area and laboratory area to improve the work quality and efficiency of the support service department. The company also introduced the advanced management concepts of Lean Manufacturing and implemented 6 Sigma management to improve its own quality internally.
[ad_2]