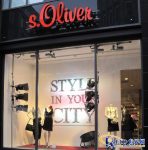
German clothing company s.Oliver uses RFID to avoid out-of-stocks
[ad_1]
After several subsidiary stores tested the use of RFID to reduce the stock-out rate, the German clothing company s.Oliver Bernd Freier began to evaluate the results of the project and determine whether to permanently adopt the technology.
s. Oliver Bernd Freier has annual sales of more than 14 billion U.S. dollars and a total of 6,500 employees worldwide; the company sells men’s, women’s and children’s clothing, focusing on youth fashion trends. 24% of s.Oliver’s business is retail, and the rest is wholesale and authorized agents. In its operating store, s.Oliver hopes to avoid out-of-stocks of certain products. The company has conducted surveys of customers, and 17% of participants claimed that if they cannot find the goods they want, they will not return to the store again.
In order to gain relevant experience in RFID applications, the company carried out its proof-of-concept test in July-September 2010, hoping to verify whether the technology can improve logistics and ensure that the store’s NOS (never-out-of-stock, never-out-of-stock) products are available. Adequate supply, thereby increasing sales.
“From the test, we realized that this technology is stable and can be directly adopted,” said Florian Oechsne, the company’s international business retail director. “Our employees are very comfortable with this system.” This system can detect 3,500 tags per hour, with a reading rate close to 100%. During the test, none of the s.Oliver customers expressed concern about RFID infringement of privacy, and employees responded positively, saying that this technology makes inventory easier to ensure that NOS products are available in the store.
The company installed a Logokett RFID reader on the ceiling above the entrance of the s.Oliver store in the Stuttgart area, and a reader from Deister Electronic to read the tags of passing goods. In the other two stores, the company uses Nordic ID handheld readers.
At the distribution centers in Rottendorf and Munchberg, s.Oliver used an Avery Dennison RFID printer to write a unique ID code on the EPC Gen 2 RFID tags, and then attached the tags to 12,000 items sent to the three test stores. Before the labeled goods are sent to the store, a reader installed under the table in the shipping area reads each label. The system electronically informs the receiving store that the goods have been dispensed, and the staff of the distribution center prints a packing list and puts it in the shipping box.
When delivered to the s.Oliver store with fixed reader facilities, the labeled goods are taken to the main entrance, the reader and antenna above the ceiling read the tags, and the system upgrades the database to indicate that the goods have been received. In the other two stores, employees use mobile handsets to read the labeled goods in each box without opening the box, and then place the handset on a cradle connected to the computer. The system compares the receipt list and the delivery list of the goods, shows any differences, and finally sends the goods directly to the store.
If the product does not need to be put on the shelf immediately, it will be delivered to the storage room at the back of the store. At this time, when the worker carries the box through the antenna and reader installed on the wall, the ID code of the tag is read again. The system upgrades again to indicate that the item has been sent to the back room. Employees use handheld computers to count NOS items twice a week to determine whether the actual items in the store meet the inventory list of the store’s ERP system. Any discrepancies found will be corrected, and missing items will be re-ordered, thereby boosting sales, according to Uwe Quiede, a senior consultant at the consulting firm Tailorit. Tailorit helped s.Oliver conduct proof-of-concept testing.
When the customer passes the RFID antenna installed at the front door, the RFID tag of the product is read for the last time. In this way, the purchased goods are deleted from the RFID database, thereby upgrading the store’s inventory.
The company is also testing the use of RFID in three stores to replenish goods of a certain size: store assistants use handheld computers to count specific items of clothing-such as women’s purple shirts. If the system detects that a certain size is missing, the employee uses the handheld to check whether the storage room is stocked. If so, the system generates an electronic pick-up form to notify employees to pick up the goods in this size immediately. When an employee brings a product to the store, the wall reader reads the product tag, and the system updates the location information of the product.
In order to simplify this project and reduce the time and expense required, s.Oliver did not integrate an RFID solution in its information system. Instead, the company adopted Gebit’s independent set of IT solutions-consisting of middleware running on separate computers in each store and distribution center, connected to an RFID server at the company’s headquarters to exchange product data in real time.
Tailorit is responsible for managing the entire project, Quiede says, from concept construction to identification and purchase of equipment, to result analysis and staff training.
[ad_2]