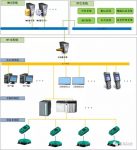
Hippocampus RFID radio frequency identification system
[ad_1]
business background
With the continuous development of information technology, the Internet of Things has undoubtedly become the hottest topic in the current manufacturing industry, and has even been hailed as the third information revolution after computers and the Internet. The Internet of Things technology combines RFID radio frequency identification technology, wireless positioning, product electronic coding (EPC) and Internet technology, and will be widely used in social, economic, and national defense fields.
In recent years, my country’s automobile industry has shown a trend of rapid growth, and due to the continuous increase in sales, the production efficiency of automobile enterprises will be more and more fully reflected. In 2016, my country’s automobile production and sales exceeded 28 million, and it has been ranked first in the world for eight consecutive years. The rapid growth of automobile demand has undoubtedly put forward higher and higher production requirements for automobile manufacturers. The market research report predicts that the automotive industry will be one of the main industries to promote the development of Internet of Things technology. The application of RFID radio frequency identification technology of the Internet of Things in material and product tracking will have a positive impact on automobile production management. The application of RFID technology in automobile production management will include production and assembly, body identification, tracking management of parts and fixed assets, anti-counterfeiting identification of key parts (such as engines and tires), logistics management and after-sales service of the entire vehicle, etc. .
User needs
Haima (Zhengzhou) Second Factory has been using a barcode system before the RFID radio frequency identification system. Previously, Haima has also implemented RFID projects in some production areas, such as the welding main line WMES system, WBS warehouse management, PBS warehouse management, RFID systems in spraying workshops, etc., but because the systems are isolated from each other, they cannot form an overall whole-process identification and tracking and are therefore abandoned. With the rapid development of the automobile industry and the increasing demand of market customers for the personalized functions of automobiles, higher requirements have been placed on Haima’s original production system, and the existing production system will be transformed to realize flexible and intelligent manufacturing and achieve rapid response to the market. The demand is imminent. Under this enterprise background, Haima has implemented projects such as MES system and plant-wide RFID radio frequency identification system. Haima’s demand for the new RFID system is based on the ability to use the original RFID hardware, through the new hardware equipment, software system to achieve the vehicle body identification from the welding shop to the assembly shop in the entire process, on this basis Production tracking error prevention, driving robots, providing production line material distribution information and other functions.
System Overview
The Haima RFID radio frequency identification system is based on RFID radio frequency identification technology. RFID sites are deployed at the corresponding stations on the production line, and a code carrier that can carry vehicle body information is installed on the line-mounted skid or on the body to realize the position of the body. Real-time full-process tracking. Due to the use of the original system hardware equipment, the original hardware contains many unreliable factors such as multiple brands, multiple models, and uncertain operating conditions, which brings certain difficulties to the system design and implementation. After careful investigation, in terms of system design, the hardware that meets the actual conditions of the site is selected, the software function meets the requirements of the Haima technical agreement, and the latest design concepts are added to complete the vehicle from the welding sub-assembly station to the final assembly 3C station. Process RFID radio frequency tracking system.
system design
As part of the informatization construction, the Haima RFID radio frequency identification system needs to cooperate with the MES system and other third-party systems to complete the production management function. The RFID system is used as the order and information upload and release layer, and the MES system is the workshop-level control layer. Collaboration is in charge of the MES system. The RFID radio frequency identification system consists of three layers, from top to bottom are the central management layer, the intermediate control layer and the device identification layer, as shown in the following figure:
System functions
Vehicle queue collection and location tracking
The RFID system is equipped with RFID reading and writing station equipment at the corresponding stations on the online body, which mainly includes the first and end of the station, special assembly stations, robot stations, transfer stations, etc., by configuring the reading and writing stations at these stations in the workshop, it can be The production workshop is divided into different areas in the system, and the number of vehicles and queue information in each area can be tracked. This information is sent to the MES system and displayed in real time. The workshop manager can easily understand the production situation of the workshop.
Vehicle leaving and returning to the team management
Vehicle leaving and returning management means that the vehicles on the production line need to be abnormally offline due to bad factors or three-coordinate detection. First, the offline reason needs to be registered in the system and the vehicle information is written into the mobile code body. The system registers the vehicle status as offline. When the vehicle needs to be returned to the team after maintenance or inspection, the vehicle information is copied from the mobile code body to the vehicle code body of the on-board vehicle, and the vehicle is operated in the system to return to the team. The system will automatically change the vehicle status to online. The records of leaving and returning to the team can be easily queried in the system.
Error-proofing of vehicle door device
Before the vehicle is assembled in the general assembly workshop, the door needs to be dismantled and placed on the corresponding spreader conveyor line. After the vehicle and the door are assembled separately, they will be assembled. Under normal circumstances, the automated conveyor line has been properly designed, and the speed limits of the car and the door are matched with each other. The car and the door are exactly one body when assembled at the door assembly station, but the vehicle will leave the team due to special circumstances during the assembly process. Phenomenon, leading to mismatch between the car and the door and possibly a series of assembly errors. The door assembly error prevention function in the system is designed to solve this problem. When the vehicle leaves and returns to the team, there will be corresponding registration in the system. A large screen display is configured at the door assembly station. When the car and the door do not match during assembly Prompt in time to prevent assembly errors.
Assembly visualization function
When the assembly is visualized, it means that the name, model, quantity, etc. of the assembly parts or quality control information will be displayed at this station due to the special needs of the vehicle during the assembly process. The RFID system can track the position of the vehicle in real time. When the vehicle arrives at the assembly station and collects the vehicle configuration information, the assembly auxiliary information is displayed on the operating station according to the production process requirements. After the assembly is completed, it needs to be manually confirmed on the system for subsequent workshop management Provide evidence.
Production material distribution management
The timely delivery of various assembly materials in the assembly workshop can reduce the probability of production stoppages. Because customers often change plans and mixed-line production, the queue information is not issued in time, which leads to mismatch between material supply and actual production, or material distribution Lag, etc. By deploying the RFID system in the assembly workshop, real-time and accurate information of vehicles on the production line is obtained, and reliable assembly information is provided for the assembly line of each sub-assembly. Place a large-screen display in the corresponding station of the sub-assembly to display queue information, thereby eliminating the manual printing of paper vehicle queues in the past. The deployment stations include engine assembly stations, instrument sub-assembly, seat conveyor lines, tire conveyor lines, instrument sub-assembly lines, etc.
Implementation Effect
By deploying the RFID radio frequency identification system in the Haima (Zhengzhou) Second Factory, the original manual scanning and tracking was changed to automatic scanning by the RFID system, reducing tracking inaccuracy due to manual misoperation, making the system more accurate and reducing labor Invest. The system leaving and returning to the team management allows managers to see the number of vehicles offline and the reasons for offline, helping them to effectively count and analyze the causes of failures and improve assembly quality. The door error prevention function can effectively reduce door and vehicle assembly errors and improve assembly efficiency. The material pulling function can provide reliable queue information for each subassembly line to ensure that the materials are matched with the main line vehicles and delivered to the assembly station in time.
Prospects
With the continuous development of the automotive industry and the continuous improvement of market requirements, RFID systems have become more and more widely used in the automotive industry, and have even become the core system for production tracking and material distribution. The RFID system can replace the original bar code system and meet the requirements for information accuracy and timeliness in the production process. RFID technology has gradually become the basis for the application of the Internet of Things technology in the automotive manufacturing industry.
[ad_2]