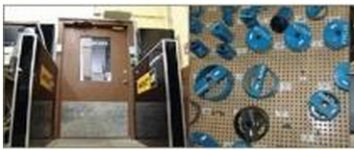
Holt Cat uses a fully automated RFID tool tracking system to achieve a rapid return on investment
[ad_1]
Summarize
Holt Cat’s daily asset management department needs to manage tens of thousands of tools. The bar code method is inefficient for them and consumes a lot of manpower. After being converted to an RFID tool tracking system, the company saw a return on investment in less than eight months, and at the same time brought about a decrease in costs and a rapid rate of employee adoption.
Holt Cat is an authorized distributor of Caterpillar® heavy equipment and engines, covering 118 counties in northern, central, southern and eastern Texas.
Holt Cat, established in 1933, is mainly engaged in the sales, maintenance and leasing services of Caterpillar equipment, engines, and generators used in construction, mining, industrial, petroleum and agricultural environments. Holt Cat also sells Caterpillar second-hand equipment worldwide and builds its own customized product line, including root plows and sprinklers.
Facing problem
The Household Assets Department of the Machinery Division manages tens of thousands of tools used in the repair and maintenance of heavy industrial equipment in 16 factories throughout Texas. Tracking the movement of these devices (from sockets to drill bits to atmospheric ion detectors worth $18,000) is increasingly necessary to control loss and maintain capacity.
Holt Cat previously used a barcode-based “virtual tool house” system to track its tools. At first, it received some results, but it turned out to be inefficient in the end. Like most companies with a large inventory of tools, Holt Cat hires an employee for each tool library to manage the tool library and track the flow of tools. The dealer chose a paper and pen-based system. After the employees took the tools from the tool library, they manually wrote down their name and the number of the tool they took. Then the tool library administrator typed the data into the company’s back-end system to excel Tracking in the form of a table.
This labor-intensive system consumes a lot of time in finding misplaced or missing tools. On average, each factory costs the company $10,000 per month.
In many cases, Holt Cat employees spend several hours looking for tools, or they are unable to complete their work because of the loss of necessary tools. In early 2006, the company decided to seek a new solution.
face the challenge
In addition to the increasing costs of unproductive working hours (and the cost of replacing lost tools), barcode-based systems simply cannot meet the daily needs of Holt Cat employees. They asked to find a “automatic, time-saving and labor-saving system” that could boost output in addition to effectively tracking company tools.
Under the leadership of Mark Pavuk, the senior management of daily assets, the Holt Cat team began to find an effective alternative to the barcode system. At the beginning of this two-year plan, RFID appeared as a similar “automatic” solution. However, difficulties still exist. The most notable is the metal environment of Holt Cat tool warehouse. 90% of the tools are all metal, and the tool warehouse shelves are all metal. There is even metal trimming in the cement on the ground, which increases the load-bearing capacity of the building area for the storage of heavy equipment. .
These metal environments cause severe signal interference between RFID tags and RFID readers that use traditional dipole antennas. After the initial test, Holt Cat found OnAsset Intelligence—an asset management integration company also located in Irvine, Texas—to assist Holt Cat in testing to determine a suitable RFID solution. Considering the multi-metal environment of Holt Cat tool library, OnAsset recommends Holt Cat to test Omni-ID’s passive passive RFID tags with 915 MHz EPC Gen2-protocol. Unlike traditional RFID tags, Omni-ID tags show the characteristics of being fully compatible with metals, so the accuracy of performance on the metal surface is almost perfect.
Omni-ID passive UHF RFID tags are part of Holt Cat’s complete tool tracking solution in Irvine, Texas. Elimination of the problem of wasting human time in the early stage, so that the whole program brought an initial return of $76,000 for Holt Cat in less than 8 months.
Solution: RFID tool tracking
The RFID-based solution brings fully automatic and intuitive information to Holt Cat’s daily asset management department, accurate to which employee uses which specific tool, and when it is used. In fact, when the system is deployed in the Irvine factory, Holt Cat no longer requires employees to manage the physical tool library.


Now Holt Cat can get specific information about who is using what tools, and can track the flow of tools between repair shops. This visualization allowed Holt Cat to receive an investment return of $76,000 for the first time in less than eight months. Through improved inventory control and the ability to share high-value tools between factories, instead of equipping each factory with a set of other changes, it also brings additional cost savings. Equally important is the affirmation of this system from Holt Cat employees.
Each employee has an ID card containing a passive HF RFID tag, with a unique ID number written in the tag. When an employee passes through the fixed reader of the tool library, the antenna of the RFID reader will obtain the employee’s ID number. At the same time, the UHF reader and antenna will pass through UHF tags (including Omni-ID Prox? and Omni-ID). Flex?) Get the tool’s code. When the technician leaves the tool library with the tools, the UHF label and the HF label in the work permit will be asked at the same time, linking the employee with these tools in the system.
The RFID-based solution proved so effective, so Holt Cat was installed in its San Antonio factory six months after completing the installation in Irvine (in the second factory, the return on investment was received in four months). In the next few months, the system will continue to be installed in 8 Holt Cat plants. As of December 2009, it is expected that this system will be fully implemented in 12 of the company’s 16 factories.
After completing its own successful implementation, Holt Cat found a new market opportunity to increase return on investment and future sales. The company has launched AccuTRACKER, a completely self-owned business system included in the tool tracking system configuration of CAT dealers and other companies across the country.
[ad_2]