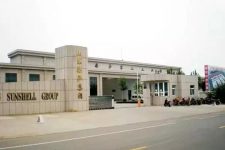
How does Sansa Group, which owns 17 garment processing plants, apply RFID systems to improve efficiency?
[ad_1]
Shandong Sansa Group is headquartered in Zhucheng, Shandong and has 17 subordinate garment processing plants. It has become a well-known large-scale garment manufacturing and garment export trading group in the industry. More than 99% of its products are exported to Japan, South Korea, the European Union, the United States, Hong Kong and other countries and In the region, there is a complete industrial chain including weaving, dyeing, printing, and garment manufacturing.

In recent years, production costs have continued to rise, and foreign trade orders have been transferred to emerging production countries and regions, putting pressure on domestic apparel manufacturing companies. In the real environment of high cost, Sansa Group is also thinking about how to maintain or further improve the production efficiency under the OEM business model. In 2012, Sansa Group set out to optimize production, and on the basis of the previous information transformation, it led production to the direction of lean development.
The system is huge, where do you start?
With 17 subordinate processing plants and thousands of people at every turn, Sansa Group operates a large system. When practicing lean production, where should you start? After analysis and sorting, Sansa Group first considers three points to improve.
First, the number of factories is large, and production coordination and management are difficult. Sansa’s subordinate fabric factories, knitted garment factories, woven garment factories…their products are different, involving tens of thousands of materials. They have encountered great challenges in formulating production plans and coordinating material requirements. If only manual management is used, this It is almost impossible to do a good job.
The second is that the scale of the factory is large, with a single factory having up to dozens of workshops and hundreds of production lines. In such a huge production system, how to grasp the production schedule in time and accurately is also a big problem.
The third is that the large number of workers, with thousands of people at every turn, not only increases the difficulty of material control, but also “difficulties” in terms of output, efficiency control, and wage accounting.

Prior to this, Sansa had introduced several department-level application systems to improve the operations of various business departments, as well as financial management system solutions, but it has not been able to effectively optimize the core business of production site management. Therefore, at the time of lean development, Sansa Group put the focus of problem solving on production site management.
There are many options, how to choose the right one?
As early as 2012, in the face of numerous production management systems on the market, Sansa focused on selecting and investigating three aspects: the stability of the system structure, the carrying capacity of data, and the professionalism of the implementation team. Due to strict requirements, Sansa failed to find a suitable system for a long time, and the production transformation was put on hold for a while. In 2014, Sansa established contact with Jiangsu Bealead and learned that Bealead can provide efficient factory management solutions, has a professional R&D and implementation team, and has cooperation experience in factories with more than 10,000 people, so Bealead was included in the inspection object.
But, what solution should Sansa introduce Bealead? At that time, the company used a traditional work ticket (barcode Philippine) statistical system. During production, workers cut off the process barcode on the “Code Philippine” according to their own production conditions. The production vouchers are then summarized and scanned and input into the computer system to count production and calculate workers’ wages. This method will bring many problems, such as: workers have to keep the code and the manager has to calculate the wages, the workload is large, and the cost of calculating the money is high; depending on the scanning device, there will be bit errors, and the bit error rate of different devices Different, the effect of simultaneous scanning depends heavily on the printing effect, and paper waste is large. These problems lead to waste of manpower and costs, data lags that cannot keep up with the company’s progress, and the accuracy of production data cannot be guaranteed. Therefore, Sansa considers introducing Bealead’s “IE-BOX” system and using RFID (Radio Frequency Identification Technology) to assist in production transformation.
In order to investigate Bealead, before launching the cooperation, Sansa put forward the requirement of “providing a system or program within one month to collect production data with an employee card that supports the Chinese bank card (IC card)”. According to this requirement, Bealead’s system needs to interface with Bank of China’s bank card and use this as the basis for data collection. This is a difficult problem.

In the process of solving the above-mentioned problems, Bealead also contacted the relevant banking institutions of Bank of China in Qingdao. Knowing the situation of the project, Bank of China Qingdao Branch took the initiative to participate in and contributed funds to jointly complete the project, providing a bank card-this card can be used not only as a salary card for Sansa’s employees, but also for data collection by Bealead’s system. The bank’s active participation helped the Bailian team to meet Sansa’s requirements as scheduled, and also realized the synchronization and improvement of large-scale system data. From the “test” set up this time, Sansa saw the strength and efficiency of the Bealead team and reached a cooperation between the two parties.
How will the new plan achieve results?
Sansa will first implement the imported Bealead system in the fifth and third factory. The company’s senior management, financial department, IE department, production planning department, cutting workshop, production workshop, piece library, statistics department, personnel department, etc. participated in it.

At the beginning of the implementation of the Bealead system plan, the Fifth and Third Factory adjusted its production to adapt it to the Bealead system. During the trial operation, the Fifth and Third Plant made key inspections on Bealead’s system in terms of subcontracting data, real-time data collection, automatic calculation and statistical data. After that, the Fifth and Third Factory also organized trainings for various departments, so that all departments were familiar with the use of the system. After some time, the related production process of the new system went smoothly, and the fifth and third factory officially used the Bealead system to collect and statistical data.
In the implementation process, the fifth and third factories no longer use paper work tickets, which not only reduces consumables, but also saves manpower; it realizes real-time collection of production data, the system automatically counts data and calculates wages; it can track quality and improve the level of quality inspection. The Fifth and Third Plant finally successfully applied the Bealead system, which not only has accurate data, but also has obvious advantages in real-time and automatic calculation. Since then, Sansa has successively promoted the Fenbailian system to other subordinate factories.
As Sansa has many factories and different types of products, Bealead’s system needs to be re-developed.To this end, Bealead sent a team of implementers, developers, and professional consultants to Sansa to analyze application requirements, and based on the conditions of different products and different factories,RFIDThe system has been adjusted to solve the problems of each factory one after another, and it also realizes seamless connection with the existing ERP system of Sansa Group.
How does Bealead’s system help Sansa to achieve the actual results of production transformation? For example, the workshop electronic billboard reflects the production data in real time and improves the efficiency of on-site management; managers can use reports to analyze the efficiency of each workshop and factory and compare them to stimulate enthusiasm and increase production. ; Each workshop supervisor accurately grasps the production progress of each contract order to avoid production problems such as overdue; automatically collects quality inspection data, so that quality inspection managers can query the scrap reduction rate of each manufacturing order in time; realize the data transfer of each factory, do There are numbers to check and evidence to follow; the “call for machine repair” function is implemented, which reduces the time wasted calling for machine repair, and the electronic data report can reflect the operation and maintenance of various equipment, facilitate maintenance, and so on.
The importance of production optimization and cost control in clothing production is self-evident, especially for the current OEM-type clothing companies, these two points are of great benefit to improving production efficiency and improving production efficiency. Shandong Sansa identified the problem and applied RFID solutions in a targeted manner to solve the problem of production management. In fact, this kind of information transformation cannot be carried out only by large factories. For every garment company seeking to transform and upgrade, Sansa’s case can be referred to and practiced.
[ad_2]