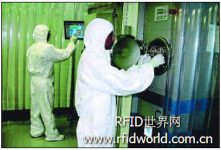
Indian optical lens manufacturer uses RFID to achieve priority order processing
[ad_1]
Indian optical lens manufacturer GKB Hi-Tech Lenses sells spectacle lenses to more than 7 million users worldwide each year. Although it has world-class lenses, the company’s order management system is quite old-fashioned. Until recently, with the help of RFID system integrator S3Edge, GKB Hi-Tech adopted an RFID system, which greatly reduced order delays, promoted overall production efficiency, and reduced order completion time by 23%.
When a customer purchases GKB Hi-Tech Lenses in a retail store, the lens specifications he needs are entered into a central order management software, which then assigns a unique identification code to the order. In the factory, the number is used to collect production information: the strength of the engraving and other characteristics, such as anti-reflective film or toning.
At the start of production, the workers first print out the order, print a barcode with the order number on the order, and then select a pair of lens blanks. Workers process the lens blanks in multiple procedures according to requirements. In the production process, the order and the lens blank are placed together in a reusable container and flow through various processing steps.
RFID readers are installed at each processing point of GKB Hi-Tech Lenses
Before adopting the new system, workers in each process must scan the barcode of the order so that the order management system can update the position of each order in the manufacturing process in a timely manner. However, some orders have a short delivery period, and the order management system cannot notify workers to give priority to these orders. As a result, some orders were completed later than scheduled, and some orders were completed earlier than required.
The company needs a way to send messages to workers and prioritize certain orders. This is where RFID improves the production process.
Now, workers still need to print the order and scan the barcode of the order. The difference is that while scanning the bar, the RFID readers installed in the processing locations of each process will collect the unique code of an EPC Gen 2 UHF passive tag on the container. S3Edge’s Real-Time Visualization System (RTVS) software-using Microsoft’s BizTalk RFID middleware platform-controls the RFID reader and is also connected to the order management software. The RTVS software corresponds the order to the ID code of the RFID tag. Before adopting the RFID system, employees in various processes had to manually scan the order barcode to upgrade the processing process and position of the lens in the order management system. Now, RFID readers automate this process by continuously reading surrounding tags.
At each processing point, RTVS collects the required information from the order management system, and then uses the data to display alarms on a video monitor. According to the specifications and completion deadline of a particular order, for example, the software specifies the maximum time required for the order in each process. If the order stays longer than the allocated time in a certain process, RTVS sends an alert to the processing worker to notify him that there is an order that needs priority processing. The alarm and the order number are displayed on the display, so that workers in this process can find the order and proceed immediately to process it. If, for some reason, the employee fails to respond as quickly as possible after receiving the alert, the second alert will be displayed in red font on the screen, and the system will also send an email or SMS message to the manager to remind them.
In addition, if an order is sent to the wrong processing process, the system will also issue an alarm.
This system also provides GKB Hi-Tech with more detailed production process traceability, helping the company improve the accuracy of orders and reduce completion time.
S3Edge uses ThingMagic’s Mercury4 reader at 7 different processing points in the factory, and the reader supports 4 bistable antennas. The label is produced by UPM Raflatac, the size is 2 cm * 10 cm, and the company currently has about 5,000 labeling containers.
[ad_2]