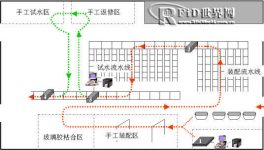
Introduction to the pilot application of RFID on the Apollo production line
[ad_1]
Guangzhou Apollo Building Materials Technology Co., Ltd. is a famous domestic manufacturer of leisure sanitary ware. Its production base is located in the Guangzhou Economic Development Zone, covering an area of 80,000 square meters. The products produced involve high-end leisure sanitary ware such as massage bathtubs, steam rooms, shower rooms, etc.
The discrete production method determines that Apollo will produce many personalized, customized products with different delivery deadlines on the daily production line. In order to meet the production requirements of JIT, the tracking management of semi-finished products on the production line is an important work of its production department. According to Apollo’s production status, Hong Kong University (HKU) Electronic Commerce Technology Institute (ETI) and South China University of Technology IBM Technology Center introduced RFID technology in July 2005 to assist their production on-line process (WIP) management.
In this pilot project, we have installed 4 RFID readers at 4 control points along the process of “molding-assembly-testing-packaging” (as shown in the figure below). At the same time, a RFID tag is affixed to each product that enters the assembly process after the molding is completed. When products flow along the production line, through the RFID reader installed in the production line, you can know the current position of each product, and even further derive the completion of the entire order.
Specifically, after the product is “formed” in other workshops, the RFID reader #1 located at the entrance is used to complete the initialization of the RFID tag: that is, the tag is associated with a certain product under an order. When the product completes the assembly process and passes through the RFID reader #2, the background monitoring system will automatically record the product’s RFID number and update the product’s completion status. When the product completes the installation test sequence and passes through the RFID reader #3, the background monitoring system will also automatically record the RFID number of the product and update the completion status of the product. At the same time, a QC platform was installed at RFID reader #3. The staff can specify whether the product is a genuine product or repaired product according to the water test situation of the product. For genuine products, after passing RFID reader #4, the product goes offline and enters the packaging area, and the time when it goes offline is recorded. For the repaired product, enter the repair area, complete the manual repair and test the water, and then return to the RFID reader #4 to let the system record the time when it was offline.
In general, by installing RFID readers on the production line and attaching labels to products, the system can automatically record the location of each product, and the person in charge of the production department can then use the system to know the completion status of the production task in real time. Avoid frequent inspections or inquiries at the production site.
For more detailed information, please email to [email protected]
Appendix: Project Memorabilia
1. September 2005: Site visit
2. November 2005: Expert argumentation
3. July 2006: Hardware installation and testing
4. October 2006: System operation
This article is the author’s original submission. The copyright of the article belongs to the author. If you want to reprint it, you must obtain the author’s consent. thanks!
[ad_2]