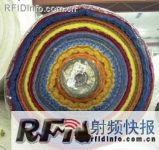
Italian textile mill Griva applies RFID technology to save inventory and logistics costs
[ad_1]
The textile industry is a highly technical and competitive industry, and many technologies need to be applied to improve efficiency in the production process. In the beginning, manufacturers used simple raw materials such as threads, etc. To make the final finished knitted fabric, they would face many problems, one of which was how to manage inventory in each step.
Textile manufacturers must strictly control the quality of materials in each step of production to ensure that each textile reel is washed, dyed, and dried. At the same time, manufacturers must also do a good job of sorting, cutting and distributing products for thousands of finished product distributors.
problem
Textile manufacturers are committed to innovating industrial processes and seeking the best way to manage inventory and finished products. They use automated production tools to increase profits while keeping costs to a minimum during production.
A typical example is Griva SpA in Torino, a city in northwestern Italy. Griva is the world’s leading large-scale textile manufacturer, with an annual output of about 300,000 rolls, and about 500 horses, or 20,000 meters, sent every day. These finished products are mainly used for upholstery and curtains, and are mainly sent to Europe. In addition, Griva also provides fabrics for the popular Hello Kitty quilt pillows.
Because of the diversity of product production, Griva must accurately control inventory. Regardless of whether it is the initial raw material line, the final braid, or the delivery and transportation of the reel, Griva must track the entire process. This is a complicated project.
In addition to the problem of tracking, another problem is that the finished product will go through multiple processing steps before it is put into storage, which causes many problems. Environmental factors caused by these problems include exposure of textiles to high temperatures, water, moisture, and strong chemicals in the printing and dyeing process. In addition, the finished product will also be subjected to machine shearing, transportation and compression packaging.
For many years, Griva has been using a traditional barcode system to track and manage textile reels. However, this barcode is not very accurate due to the pressure of the machine and the environment. So when Griva was preparing to operate a new automated warehouse in 2006, it planned to cooperate with Simet, an RFID integrator in Italy, to solve the problem of textile tracking.
“The barcodes used by Griva are often damaged due to environmental pressures,” said Claudio Bertodo, Simet’s marketing director. “For precise inventory control, Griva’s use of barcodes is not feasible.”
solve
Simet introduced RFID solutions from Alien, and developed a complete RFID tracking solution for Griva. However, at the beginning, Simet used Alien Gen 1 RFID products, and later chose the Alien Gen 2 reader solution, and chose the best model ALR-8000, which complies with the European Telecommunications Standards Institute (ETSI) EN 302-208 specification.
Griva uses the Alien EPC Gen 2 Squiggle label, which is attached to the textile reel. This Squiggle tag can be effectively used in complex production environments, supports 860-960 MHz, and reaches the first-level EPC Gen2 efficiency cost benchmark. Squiggle tags and readers provided by Alien can provide the best read range and read performance.
Simet also provides a reader-ERP interface for Griva. As a middleware, it can be shared with Griva’s existing ERP software program and control the reader through the Alien Reader Protocol.
Bertodo said that initially this RFID system was used in parallel with Griva’s existing barcode system for six months. “After we repeatedly compared the implementation effects of the barcode system and the RFID solution, we found that RFID is the best choice for Griva,” Bertodo said, “because RFID has high accuracy.”
Effect
The RFID solution provided by Simet can solve all the problems that Griva could not solve when using bar codes before. Through the use of RFID technology, Griva can implement full tracking of the various processes of textile production logistics.
The Squiggle label provided by Alien can identify products through the plastic film, which is not possible with barcodes. By using RFID technology, Griva can effectively track the reel after packaging, thereby saving time and providing customers with accurate information about the finished textile.
This RFID tag can enable Griva to automate inventory: each reel is programmed with an ID number so that the reel can be moved to the next checkpoint. Readers are installed at each checkpoint so that the staff can quickly determine whether the reel should be placed in the storage warehouse or should be shipped immediately.
In the final stage, this automated system will use RFID technology to determine the final packaging and the most cost-effective means of transportation. By using the textile weight and destination information, the inventory manager can order some shipping boxes to prepare for the final shipment.
Benefits and post-work
The RFID system used by Griva has made the company’s logistics more efficient and has also brought a significant return on investment. Gualtiero Casalegno, President and CEO of Griva, said, “After adopting this RFID system, we have saved costs, time, and increased customer satisfaction with our products. In just 9 months, our return on investment It reached 30%.”
Griva’s later work will be to install more readers in the warehouse, especially portable readers. In this way, the warehouse clerk can check the inventory in one night.
[ad_2]