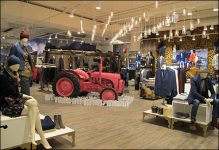
Moods of Norway chose Checkpoint System RFID tags and tested fixed readers
[ad_1]
In the past year, Moods of Norway’s clothing suppliers used it on all clothingRFIDLabel. The company claims that its suppliers are using Zephyr 2 EPC UHF RFID tags provided by the Checkpoint system, and employees will check the products in 14 stores every week to improve inventory accuracy. Hans Petter Hübert, supply chain manager of Moods of Norway, said that because the RFID system has improved inventory-level product accuracy, the product can now be delivered to online customers from the store closest to the consumer. He said that this is impossible without an RFID system, and the inventory accuracy rate in the past was not high enough to ensure that the goods are in stock.
Moods of Norway is also testing fixed RFID readers for receiving and shipping goods at distribution centers. The company has piloted a fixed reader in a store for inventory tracking.
(In Moods of Norway’s 14 Scandinavian stores, all clothing is attached with Checkpoint Zephyr 2 EPC UHF RFID tags. At the same time, employees will take inventory once a week)
The retailer operates a total of 18 Moods of Norway stores, most of which are located in Norway, with only two opened in Sweden and California. Three of the 18 stores are discount stores. Retail stores sell clothing and accessories, of which clothing sales account for 90%. The company’s 14 non-discount stores in Scandinavia are equipped with handheld RFID readers provided by Nedap, and the company is also discussing a system implementation plan for its California store.
In January 2014, Moods of Norway began testing RFID technology and chose Nedap’s! D Hand handheld RFID reader for employees to conduct weekly inventory counts. During the inventory process, employees walk around the store with a! D Hand handheld reader and iPod, read the ID numbers of all clothing tags in the store and the back room, and then the reader will automatically upload the data to the iPod via Bluetooth. Then, this information will be transmitted to the Nedap cloud server, and employees can log in and view.
Initially, the company only marked on men’s shirts and suits. Now the supplier has marked on all clothing. Recently, Moods of Norway began to choose Zephyr 2 RFID tags due to price and checkpoint service reasons. Currently, most of the company’s suppliers are located in China, but Hübert said that half of its products will be produced in Europe next year. But whether in Europe or Asia, Checkpoint can quickly provide suppliers with the RFID tags they need.
The read data is stored in Nedap’s cloud software and integrated with Moods of Norway’s ERP. In September 2014, all suppliers began to attach a new brand and model label to each product, involving 30 to 40 manufacturing plants. After attachment, the products are transported to Moods of Norway’s distribution center in Norway. The company has also tested RFID tunnels at the distribution center to speed up the receiving and transportation of goods. The RFID tunnel uses an RFID reader and Impinj Brickyard antenna to read the received item tag ID. At present, the test focuses on judging the quality and efficiency of tag ID reading.
When the goods arrive in the store, employees will place them in the back room or on the shelves. Then, employees will take inventory once a week. Let the company know any cargo information.
Moods of Norway also uses an automatic replenishment system, which uses sales data to trigger replenishment of goods in the distribution center. Hübert said that one of the advantages of RFID is that it can reduce confusion in the replenishment process. Stores often complain about the wrong items or missing items from the distribution center. He also said that due to the weekly inventory count in the store, the company learned that the inspection process in the distribution center rarely makes mistakes. The cause of the confusion is due to inaccurate inventory information in the store. Since store personnel don’t know what items need to be restocked, they don’t know that the distribution center’s delivery is actually correct.
Last summer, before using the Zephyr 2 tag, Moods of Norway tried out the Impinj xArray reader in a Norwegian store. At that time, the company tracked 700 tagged items and found that they could check the location of items in real time. Hübert said the company needs more testing to determine whether it will be deployed permanently. The company is also considering installing a reader at the cashier or installing a fixed reader at the door for electronic commodity anti-theft system (EAS) detection.
Checkpoint’s Doyle said that other retailers have also shown considerable interest in RFID. She said: “Clothing brands are updating products more and more frequently to provide consumers with more fresh products.” The clothing industry has shortened the process from product and label design to delivery, which has also led to continuous redesign and prototyping of products. And listed. She said: “Our design services, on-demand printing services, and automated production have shortened turnaround times, helping apparel brands adapt to faster cycles and changing needs.”
Hübert said that since the RFID system was deployed last year, online sales have increased by 20% due to availability from nearby stores. When a customer places an order online, the purchased goods will be sent from the central warehouse or the nearest store. By better understanding local inventory, the company can deliver faster, thereby increasing sales.
Hübert said that the inventory accuracy rate has also increased to 100% due to the installation of the RFID system. He said: “Compared to the past 70%-80% inventory accuracy rate, 98% inventory accuracy rate can increase service levels and shelf utilization.”
Hübert expects that the revenue increase from the system during the six-week trial will be enough to cover the cost of labeling for one year.
(Exclusive manuscript of rfid world network, please indicate the source author for reprinting!)
[ad_2]