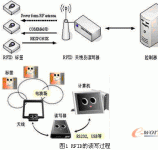
RFID-based manufacturing execution system and application cases
[ad_1]
1. RFID application background and needs
1. The new situation facing the manufacturing industry
· Short product life cycle
·The rapid growth of multi-variety and small-batch production methods
· Market changes are fast and unpredictable
2. The transformation of production process management methods
·Just in time (JIT) and lean production are becoming more and more popular
·The coordination requirements for all links of production are getting higher and higher
·How to accurately and timely solve the tracking and management in the manufacturing process
·How to adjust the production process in time to adapt to the multi-variety and small-batch production method
3. Problems faced by the manufacturing industry
·The real-time production information of the workshop does not have a unified data view, and the system is difficult to integrate
·There is a gap between enterprise resource system and workshop production
·Multiple and complex systems lead to inconsistent real-time information and lack of standardization
·There is a gap between the process control system and the manufacturing execution system
Can not detect and prevent problems that may occur in the production process of the workshop
In view of these problems, although the idea of lean production is advanced, how to implement its idea into actual work? First of all, it is necessary to find a way to implement the concept, secondly, to establish the means and measures that can operate in the workplace method, and finally to implement it in the production activities. It must rely on such a process to implement it.
Let’s analyze the bottleneck of the problems faced by the manufacturing industry: Lean production involves the collection, transmission and processing of information. At this stage, the development of enterprise informatization in the three parts is not consistent, and the bottleneck problem largely comes from information collection.
Lean production requirements for information collection:
·Real-time: Collect and upload production line information in time
·Accuracy: to ensure the accuracy of the collected information
·Information collection scope: collect all kinds of information needed to implement lean production
2. RFID technology and application
1. Technical characteristics of RFID
·RFID (Radio Frequency Identification) is a non-contact automatic identification technology
·Automatically identify target objects and obtain relevant data through radio frequency signals (radio waves)
·Without manual intervention, multi-target, high-volume, fast identification
·High temperature resistance, adapt to harsh environment, long working distance
·Unique identification, large data capacity
2. RFID reading and writing process
Figure 1 is the specific read and write process of RFID.
3. RFID tags
RFID tags can be packaged into different shapes, and there are various specifications. There is a chip in it, the chip has an antenna, and it is connected to the reader through the antenna. This is a relatively advanced technology at present, as shown in Figure 2. Some chips are only the size of a finger, and some can be very large.
3. RFID-based manufacturing execution system
Utilize the above-mentioned characteristics of RFID, introduce RFID technology into MES, promote manufacturing production process management and control, and adapt to modern production process management changes. RFID is an effective way to improve the management of the production site of discrete manufacturing enterprises. Realizing the management and control of the production process based on RFID is the current technological development trend.
1. The role of RFID in MES
·Effectively track, manage and control the resources and work-in-progress required for production;
·Realize data collection automation and real-time, solve the problem of information lag;
· Make up for the “information gap” between the enterprise planning level and the control level;
·Realize real-time, transparent and visualized management of the production process;
· Effective control of production and inspection procedures;
·Tracking and analysis of processing procedures;
·Extend production and inspection information to after-sales service, enabling effective and accurate tracking management to be established.
2. MES combined with RFID-the support of lean production system
Implement lean production based on RFID-MES:
·Acquisition of basic data
·On-demand transmission of production instructions
·Support staff management
·Realize the real-time sharing of information between departments
·Realize on-site management and support collaborative work
Through information transmission, the entire production process from order placement to product completion is optimized and managed. Emphasizing the optimization of the entire production process, it is necessary to collect a large amount of real-time data during the production process and deal with real-time events in a timely manner.
3. The role of RFID-based MES
·Timely grasp the production plan and production line production status
·Strengthen the timeliness and accuracy of material distribution on the production site, and reduce the rate of assembly errors
·Collect various production data, such as important parts assembly information, inspection data
·Strengthen production process quality monitoring and tracking capabilities to improve product quality
·Improve the overall production efficiency of the production line
Four, application cases
With the support of the National 863 Program, Loncin Motorcycle’s finished car production line has successfully applied a manufacturing execution system based on RFID technology, as shown in Figure 4.
1. MES application function
1) Management application
·Remote monitoring of production process
·Production process quality management
2) Production site application
·Management of dispatch plan execution
·Work station production coordination management
·Batching and assembly management
The information collected in real time includes: ① finished vehicle tracking information, ② ingredient information, ③ finished vehicle quality information, ④ worker workload, etc.
2. The benefits of implementation
It provides strong support for the implementation of lean production management:
·Improved the level of on-site management, improved the pass rate and production efficiency of finished vehicles once off the assembly line;
·Promote the refinement of production organization and management, improve the quality of product manufacturing, and reduce the consumption of manufacturing resources.
3. The problem to be solved
·Insufficient ability to monitor the status of the production site
·Poor coordination between stations
Lack of effective guidance on site operations and ingredients
·Quality data entry lagging and other issues
Five, concluding remarks
With the increasing popularity of lean production process management, informatization support methods such as MES and RFID have gradually improved and matured, which has promoted the deepening of enterprise informatization and provided a stage for enterprises to implement advanced production models. Effective integration.
[ad_2]