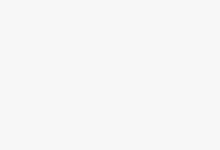
RFID chip manufacturers use RFID technology to improve production and processing efficiency
[ad_1]
TowerJazz, a global silicon chip manufacturer, not only produces high-memory radio frequency identification chips for the aerospace industry, but also uses WIFI-based RFID technology to track work progress at one of its production bases. The solution is deployed at the TowerJazz manufacturing plant in Newport Beach, California, and consists of the following parts: AeroScout’s battery-powered (active) WIFI tag, a sensor (trigger) that can better point out the location of the tag, and a Positioning information processing software, based on reading the label information, can locate the position of the wafer during the processing through this software, and at the same time can share the read data information with the company’s dispatch and distribution system. The system was installed in different stages: the first stage in 2011 (identifying the location of the manufacturing station); the second stage at the end of 2012 (identifying the temporary holder of the container filled with wafers). Light-emitting diodes (LEDs) are now being installed to observe that a batch of wafers has reached a specific workstation.
TowerJazz provides integrated circuits to many semiconductor companies in the world. Tego Inc. is one of the customers. TowerJazz manufactures high-memory passive ultra-high frequency (UHF) RFID Tego chips that meet the EPC Gen2 standard for tracking pressurized or unpressurized parts in the aerospace industry. TowerJazz operates three processing plants: one in Israel (producing RFID chips); the second in Japan; and the third in California.
In addition to manufacturing Tego chips, TowerJazz produces dozens of multiple batches of chips every day. Each batch contains 25 wafers, uses different processes, and has hundreds of unique steps, such as etching and polishing. Before being delivered to the customer, each step is completed in a series of workstations in a specific order. At the workstation, during the manufacturing process, the staff must use specific tools for each location to complete a step and then move the wafer to the next intended filling location for a specific batch and sequence.
Dale Bogan, the production director of TowerJazz said that this process is time-consuming. If the operator performs manual scheduling, that is, for the next workstation that a batch will be moved to next, make sure that it performs the appropriate procedures and does not lag behind. In the order that is specified thereafter. “Our production line is not linear,” he explained, “so anywhere in the production line there may be a batch that is dispatched to the next step.”
Although the company seeks to improve the efficiency of the system for manually scheduling and distributing the manufacturing process, Bogan said that the high cost of installing a fully automated conveyor system does not provide the high return on investment the company needs. Therefore, TowerJazz chose to continue to use the existing scheduling system-many orders are received, specific sites are arranged to manufacture these chips-while using RFID to read the data to ensure that the appropriate allocation process. The company believes that adding RFID technology to the manufacturing process can improve efficiency and achieve on-time delivery.
During the manufacturing process, TowerJazz puts an AeroScout T2 label in each batch of wafer boxes. When an order is received, the tag’s unique ID code is connected to the order description in TowerJazz’s existing real-time dispatch (RTD) system, and then the tag sends its ID to the WIFI nodes installed throughout the facility.
The company also installed AeroScout EX2000B and EX3210 triggers at the entrance and exit of each workstation to track the progress of each batch of boxes. When a batch is transported to a site, the sensor at that location will send a low-frequency wake-up signal to the tag, and then the tag will send its own unique identifier and sensor ID to log in to the regional WIFI access point.
AeroScout software determines the location of the batch at a specific workstation and forwards this information to the company’s scheduling software, thereby updating the status of the batch. At any time during the manufacturing process, Bogan said, TowerJazz “can go back to the history of the physical location” for each batch in the production process. He pointed out that, compared to manual methods, “scheduling data is real-time and more accurate.”
When the manufacturing process of a batch is completed, the wafer is taken out of the box and delivered to the customer, and the box and the RFID tag on it will be reused by another order.
Since the system was installed in July 2011, Bogan reported that TowerJazz can understand where each batch is located at any point in time and determine when a particular batch is behind or sent to the wrong workstation. “We have greatly improved the efficiency of operators,” he said. He also added: “We were able to reduce labor costs and deliver on time.”
In the second phase completed at the end of 2012, TowerJazz installed triggers on the racks between the workstations to identify a certain batch of racks waiting for the next designated workstation. Currently, there are more than 100 triggers installed in its brackets, outlets and entrances of workstations.
For the next stage, the company will install a system with a visual positioning function. When a labeled batch enters the reading range of the trigger, the LED will light up to remind the staff of the location of the batch.
[ad_2]