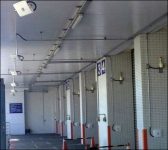
RFID helps improve the visibility of LCD panel manufacturers’ supply chain
[ad_1]
The Taiwan factory of LCD panel manufacturing company Innolux installed a passive UHF RFID system to track the arrival and departure of vehicles and pallets. Since the installation of the program in June, the system has improved operational efficiency and reduced errors caused by trucks entering the wrong dock or difficult to locate in the past.
Innolux plans to install the same system in a Chinese factory. The system uses Alien’s readers and UHF RFID tags provided by EPC Taiwan. The tag is installed on the ground, forklifts, metal and plastic pallets, and shipping containers. The tag has an Alien Higgs 3 RFID chip built into it. In addition, Innolux also deploys self-developed software to manage RFID reading data.
(Two Alien RFID readers are installed on each terminal door: one is installed on the ceiling above the loading platform (used to read the ID number of the label on the floor and shipping container), and the other is installed on the door side (used to read Take the forklift and pallet tag ID number))
Jacky Cheung, Manager of Innolux, said: “This is our first warehouse transportation management system. We use the most advanced RFID technology.”
Founded in 2003, Innolux is the world’s largest TFT-LCD display manufacturer. The company’s customers include many leading information technology and consumer electronics manufacturers such as Dell, Hewlett-Packard, Lenovo, LG, Panasonic, Samsung Electronics and Sony.
Innolux has 14 factories in Taiwan and a number of factories in China, providing a series of panels and touch screens for consumer electronic products. In this company, some parts are produced in one factory and then shipped to other factories for assembly. Therefore, trucks need to transport materials, semi-finished products and finished products back and forth. The management of truck movement, packing pallet goods on the truck has become a very challenging task. The company tried to use active RFID tags, but found that the technology had little effect. RF signals will overflow from the dock doors, and the system will not be able to identify the specific location of specific pallets and trucks.
The company contacted EPC Taiwan, seeking to deploy EPC UHF RFID technology in its factory. Innolux wants to know where the truck is arriving, where the loading and unloading doors are.
A total of 17 Alien ALR-9680 readers were installed in EPC. Among them, two Alien RFID readers are installed on each dock door: one is installed on the ceiling above the loading platform (used to read the ID number of the label on the floor and the shipping container).
(A passive UHF RFID tag is installed on the ground in front of each dock door, so that the system can confirm whether the truck is in the correct position)
When the truck arrives at the gate of the factory, the driver first registers with the doorman, and then fills in a paper document stating the items to be picked up or placed. The UHF tag is attached to the bottom right of the shipping container towed by the truck by a magnet. EPC Taiwan project manager John Chiu said: “During the project installation, we developed a special label for trucks. The label is recyclable, durable, easy to disassemble, and can be used on metal materials. Therefore, we used magnets for fixed installation.” Label link The ID number and its binding information are stored in the Innolux RFID software. The driver can then follow the instructions of the supervisor to load and unload the cargo.
Aden Yin, a senior engineer at EPC Taiwan, said: “The tags on the ground at the entrance of each terminal ensure that the RFID system does not make mistakes when the truck is in front of the door.” When the truck is not parked on the loading platform at the entrance, the reader on the ground ceiling can read Label to confirm that there is no car at the terminal. When the vehicle retreats to the door, the vehicle prevents the transmission of the tag, and the software therefore no longer receives the tag ID, which means that the truck is at that location. At the same time, the reader will also read the tag ID of the truck transport container. The software automatically pairs these two pieces of information to confirm the location of the container.
If the software judges that the vehicle is parked in the correct position, the light on the dock turns yellow, indicating that it is ready to be loaded or unloaded. If there are no vehicles on the dock, the light remains green. If the vehicle is parked in the wrong position, the light color will change to red.
Innolux uses two types of pallets to move materials and products. Metal pallets flow within the company, while plastic pallets flow to the supplier. RFID tags are permanently attached to the metal tray. The RFID tags of plastic pallets are for temporary use.
When the truck leaves the factory, the magnet tags are removed from the shipping container. Subsequently, these tags will be recycled on other vehicles.
(UHF tags are installed on the bottom right of each shipping container that arrives at the dock by magnets.)
Innolux’s software stores information about each container and pallet. In this way, the system will issue a warning when the forklift loading and unloading position is wrong.
Chung said: “Using the RFID system, we don’t need to touch any buttons. The data is there.” The system has improved the efficiency of the company, and employees don’t need to spend too much time filling out paper documents or reviewing before loading.
[ad_2]