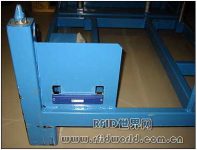
RFID helps ZF Friedrichshafen speed up product shipments
[ad_1]
ZF Friedrichshafen is a world-renowned supplier of vehicle chassis and transmissions. The company is now upgrading its manufacturing plant, including the adoption of an RFID container management system. The RFID system reduces the processing time of containers and increases the speed of the delivery process. ZF is now also carrying out relevant tests to determine whether RFID can be used to improve the efficiency of other processes.
ZF has 119 factories in 25 countries around the world, with approximately 57,000 employees, and the company’s fiscal revenue in 2007 reached 19.5 billion U.S. dollars. At the ZF Friedrichshafen plant, the company produces transmissions and chassis for commercial vehicles of other brands such as MAN and Iveco. More and more truck manufacturers require ZF not only to be punctual, but also to supply products in the order of production. Therefore, ZF hopes to improve the production process to deliver the right products to customers at the right time and in the right order. So ZF contacted Trico, an Austrian RFID system integrator.
Tricon installed an RFID system for ZF in 2006. This system uses 15,000-20,000 passive UHF tags to track 1,000 containers every day. The system has been running well since it went live at the end of 2006. , There have been no problems. ZF is considering adopting this system in other factories, said Jürgen Kusper, Tricon project manager.
Passive UHF tags installed on containers
Through the RFID system, ZF knows exactly what cargo is loaded in the container. Before adopting RFID technology, the company had to manually count the cargo in the container on a specific date to estimate the average inventory of the container. In addition, Kusper said, RFID helps ZF minimize the loss of expensive containers. “Now, ZF can clearly understand which customers have returned which containers and which containers can be shipped.” He said.
When workers receive the truck or the container returned by the car manufacturer, they usually place them in a temporary storage area. A few days later, workers placed the containers on an automated conveyor belt system and sent them to a fully automated high-bay storage area. When the container moves along the track, a FEIG Electronic reader reads the tag. Based on the position data read, the system can determine whether the container is in the correct position on the crawler track, or whether it must be rotated 180 degrees.
As the container moves on the conveyor belt, a reader reads the tag
Unless a new container is introduced during transmission, this will be the only tag reading point in the entire application. Since the container flows automatically in the process of loading and preparing for shipment, the computer system can calculate the next position of the container according to the label reading point. When new containers are added to the conveyor system, employees use a handheld reader to initialize them. The system assigns a container code to each label, which is compiled into the label together with the description of the labelled container, so that ZF can track a single container and the corresponding customer. There are 9 types of containers used by ZF.
When a worker needs to integrate a drive or component, he places an electronic order in the company’s warehouse management system. The automatic system puts the required components in a labeled steel container, the size of the container ranges from 80 * 120 cm to 80 * 160 cm, and sends the container to the appropriate location in the production area. Factory automation speeds up production and delivery, and it is also necessary (because the parts are too heavy to be transported manually). When the container is sent back, the worker scans the label (that is, when it is sent to the conveyor belt), and the system updates the information accordingly, so that ZF can know which containers are in the factory at a specific time.
At present, ZF is considering revamping the existing RFID system, hoping to automatically read the tags when the container is returned, rather than being read by the RFID reader on the conveyor belt after being placed in a temporary storage point for a few days. Reading the label earlier allows the company to better understand the available containers.
During the implementation of the project, Tricon’s biggest challenge was to find container labels, taking into account the application environment of metals and machinery. The tag reading distance must be long (even if installed on a metal surface), easy to install, and cost-effective (considering the high application volume).
Tricon finally chose the Intermec 869 MHz frequency label, which complies with the ISO 18000-6B standard.
[ad_2]