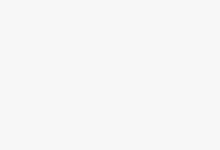
RFID system increases visibility of glass production
[ad_1]
After the completion of its pilot program at the Owatonna point in Minnesota, architectural glass manufacturer Viracon is preparing to launch a Wi-Fi-based active RFID real-time location system (RTLS) throughout the company, so as to correct when the glass transporter is moving. Its positioning.
The system is provided by AeroScout and has been used to track, monitor and manage all glass transport vehicles throughout AeroScout’s 10,000 square foot campus in Minnesota. The company intends to deploy this system in its other two plants by 2008. The locations are in Stesborough, Georgia and St. George, Utah.
Viracon is one of the largest architectural glass manufacturers in the country. It designs windows for large-scale commercial buildings, such as the Freedom Tower in New York City, as well as small projects. The company orders and sells 50 million square feet of glass each year, and its three factories are processing hundreds of orders at the same time. In the Minnesota factory, orders are usually transported back and forth between six stations in a truck to complete cutting, laminating, lamination or imitation silk printing. Some of these transport vehicles, giant metal frames with wheels, can only hold one or two molds of glass for an order, while others can hold much more than this when there is a large order.
According to Todd Schelling, Viracon’s production manager, hundreds of trucks shuttle between the three buildings in the Owatonna plant. “This is very different from the assembly line,” he said. Unlike the assembly line, the path is knowable, the transportation route of glass from one site to another varies, depending on the customization requirements performed. Therefore, positioning these transport vehicles is a difficult task.
Until it launched an RFID-based trial in the fall of 2007, the company used a handheld Intermec SF51 mobile barcode scanner to track the movement of the truck. When a transporter is installed for the first time, each piece of glass on it is attached with a barcode number label. These labels on the glass are scanned together with the barcode ID labels affixed to the transport truck, and finally linked to the back-end inventory management system of Viracon.
When the truck is sent to a site for processing, an employee at that site will scan the ID number on the truck and update the system regarding the location of the order. Employees only need 60% of the time it takes to scan the truck, and when they are looking for a specific order, they sometimes need to go from the assembly level to the other. If the transporter cannot be found, Viracon will have to re-execute the order and start the manufacturing process from scratch. If the company found this car afterwards, part of the glass processed inside was also discarded.
Matt Miesner, the company’s production improvement project leader, said that Viracon considered using RFID solutions about a year ago and found that passive RFID tags do not work as well as active tags in this environment. Therefore, in the third quarter of 2007, Viracon began to trial the Wi-Fi 2.4 GHz RFID system provided by AeroScout. The company installed approximately 80 Cisco Wi-Fi access points in one of its three plants, and also attached AeroScout T2EB industrial tags to 500 transport vehicles. These tags are powered by a battery that can work for eight years and have a readable range of 450 feet.
If the transport vehicle is stationary, its tag only transmits the ID number once every half an hour. Once the car starts to move, a motion sensor in the tag will notify the tag to flash every few seconds when the car is moving. The Cisco application software allows the access point to record the label position in detail within a fifteen-inch range. This data is stored in Viracon’s inventory management database and is acquired by AeroScout’s MobileView software, allowing workers to locate a specific transporter by displaying an icon on the assembly level map on their computer screen.
AeroScout Industrial Solutions Market President Amir Ben Asa said that the trial, which began in late 2007, was very successful and directly led to the full realization of the technology in the Viracon Owatonna plant in its three buildings. According to Ben Asa, the company found that the search time for each truck has been reduced from an average of 15-30 minutes to less than one minute. “Our goal is to automate the process, shorten the search time, and avoid the loss of transport vehicles,” he said. “We have achieved these goals.”
Ben Asa said that the biggest challenge in installing this technology is that the presence of metal and high ceilings may cause RF interference, but the use of Wi-Fi active tags and access points makes it possible to effectively transmit signals in this environment. . These facilities were completed at the Owatonna plant this month. With them, Viracon will use approximately 5,000 Wi-Fi-based active tags provided by AeroScout on its transport vehicles.
Miesner said the company has completed a cost/benefit analysis and determined that the system will reduce search time, increase throughput, and reduce the amount of waste glass. He expects that the search for transport vehicles can be reduced from 40% to less than 1%, and said that the company expects to reduce the re-customization caused by the loss of transport vehicles by 50%-70%. Miesner said: “We expect to recover the investment in one year.”
[ad_2]