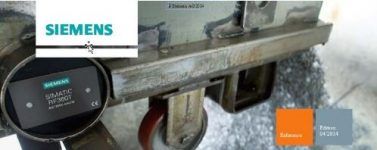
RFID technology guides the generation of stamping waste in a more flexible way
[ad_1]
In the production of punched sheets (Figure 1), a large amount of stamping waste is inevitably produced. MEVACO GmbH, located in Schlierbach, Germany, generates an additional 8,000 tons of this waste every year. The perforated sheet produced by medium-sized companies has many forms and shapes, and many materials are involved, including aluminum, copper, low carbon steel and stainless steel. The company specializes in small and medium-sized perforated plates. In addition to ready-made stock products, it also provides a large number of customized perforated plates of the size shown in Figure 1. Due to complex order planning, frequent changes in pressure and materials are required. The four high-output presses generate a huge amount of waste, and these machines process sheets up to 1500 mm wide, 365 days a year. MEVACO always directly collects the waste generated during the molding process of these four machines-without impurities-for resale. Buyers include steel mills, manufacturers of die-cast aluminum components, and iron manufacturers.

Therefore, a so-called scrap metal channel is located under the four presses, and inside the channel there is an automatic transport system, a truck with many boxes (Figure 2). This transportation system correctly arranges empty or half-full boxes under the press and returns them to the buffer zone. For example, each box is assigned to different materials. The filled boxes are automatically transported to the unloading station, and in the waste warehouse, the contents are dumped by the crane into the corresponding truck.
More variety, higher requirements
Jochen Schott, Technical Director of MEVACO, said, “Some customers hope that the stamping waste in the waste bags is free of impurities. Our task is to ensure that the weight of these plastic bags reaches 2 tons. Therefore, we must record and accumulate in each stamping sequence. Weight.” “Other customers require higher bulk density in their applications, so they can only use small diameter metal blocks, and this will increase the number of different waste products.” In order to run a reliable automatic operation System, the control system must always know the quality of the metal blocks in each of the 23 trucks and the quality of the trucks. With previous control systems and trucks, the shape of the scrap is permanently fixed, which is impossible to achieve. So the operator decided not to use the accumulation method, but to adopt a new, more powerful, more flexible and advanced solution. This solution can operate reliably for many years and is easier to expand if more components need to be connected.
The implementation of the program is handed over to the German company Stuttgart, which is a branch of Heldele GmbH, which is a system integrator specializing in automation and a partner of Siemens automation solutions, and is already very familiar with MEVACO. The two parties together put forward a sustainable development concept based on the control components provided by Siemens, and finally completed the installation and integration in just a few days.

The production of customized perforated sheets is a special feature of MEVACO GmbH in Schlierbach
End-to-end automation
The main part of the new solution is a SIMATIC S7-300 PLC in the central control cabinet, which can communicate with MEVACO’s high-level control system. An industrial Ethernet switch of the Siemens SCALANCE X116 series connects the press and the operating unit of the metal block warehouse, and establishes a network connection with the metal block channel. In order to record the quality, the location address under the press should meet the requirements of the SIWAREX U load cell directly connected to the control center. A small decentralized device installed in the lower part of the metal block channel obtains the signal of the level monitor (using ultrasonic and laser grating), and forwards it to the control center via PROFIBUS.

The new control and identification system adopts the RFID (Radio Frequency Identification) technology provided by Siemens, and MEVACO realizes a more flexible and advanced collection of stamping waste without impurities
IWLAN and RFID increase transparency
Michael Anh?user, project leader of Heldele GmbH, believes that the key to the transparency and flexibility of the new solution lies in the identification of the truck and the communication between the control components in the control cabinet on the carriage and the main control cabinet. In order to achieve identification, credit card-style SIMATIC RF360T RFID electronic tags (Figure 3) are installed on 23 trucks. These tags are installed in the groove of the plastic gasket, which can effectively prevent mechanical damage. Due to the high protection level of IP67, these tags can be used in harsh industrial environments where they are often in contact with oil and cutting fluids.
If a relatively large antenna is selected for an electronic tag the size of a credit card, the reading range can be increased, and the reading distance can be extended. Accordingly, there is no more requirement for the accuracy of positioning. Corresponding to the electronic tag is the SIMATIC RF380R RFID reader (Figure 4) installed on the transport carriage. It can read the identification number stored on the electronic tag within 10cm and match it as required. The reader is integrated into the control network and PROFIBUS through the ASM 456 interface module.
Günter Schöfer, who is responsible for maintaining the electrical system, said that “the initial suspicion about the application of the harsh metal environment is unfounded.” “Since trial operation, the operation of the highly challenged RFID system has been stable and reliable.”
The bridge between the transport carriage and the central control cabinet is built by the IWLAN system (Industrial Wireless Local Area Network), which consists of a SCALANCE W788-1 Pro access point installed on the channel wall and a SCALANCE installed in the mobile control box W746-1 IWLAN Ethernet client module composition. The access point with two standard antennas reliably covers the entire metal block channel, so the additional RCoax leaky wave cable originally planned to be laid along the driving route is also omitted. Therefore, the instructions and box data stored in the main controller data block are automatically assigned to the correct truck.
The connection between the higher-level production plan and the MEVACO control system (PPS) is realized by a SIMATIC IPC227D nano box PC installed in the central control cabinet, which is a very compact embedded industrial computer. This computer is integrated into the control network through the CP343-1 communication processor and sends command data to the production unit. In turn, the type and weight of the product are transmitted to the internal web application via OPC (OLE for Process Control), which allows MEVACO’s customers to retrieve the current supply quantities and orders from the internet.

SIMATIC RF360TRFID electronic tags are installed on all 23 trucks to clearly record and distribute materials and weights
More open, flexible, and efficient than ever
By using bulk bags, basically any type of waste on any truck can now be collected. This was impossible in the past, because small metal scraps always stick to the wall of the box and cause a lot of pollution. There are about 15 trucks that are free now, which can be flexibly assigned to different materials, so that more kinds of waste products can be sorted into bulk bags easily.
Another benefit is that the transparency of the new system is greatly increased. For example, more and more diagnostic data are shown to operators. In this way, the operator can locate and correct the wrong position faster. Jochen Schott believes that “this new solution is more conducive to future expansion.” If another production hall can be built, the metal block channel may be extended and a second transport carriage may be used. The next step can be to expand the RFID solution to cover truck containers, which will eliminate another source of error. The technical director believes, “We have never lacked ideas. We have now created the technical conditions to realize them. In this regard, we have clearly become more open and flexible.”
[ad_2]