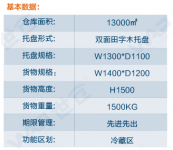
Shuttle rack case using RFID system in domestic cold storage industry
[ad_1]
Customer Introduction
XX Company is a large-scale storage and refrigeration company in South China, one of the most advanced storage and refrigeration enterprises in China, and the largest aquatic product freezer in Guangdong. The cold storage has a total area of 18,000 square meters, a total investment of 70 million yuan, a storage capacity of 30,000 tons, and a total of four standard low-temperature cold storage to meet the requirements of different customers.

There are many customer products and it is not easy to manage. The traditional operation mode-scanning barcodes is not only prone to manual scanning errors, but also wastes time and poses safety risks.
Customers are looking for a more intensive, more efficient, safer and more accurate storage operation mode.
Upgrade-maximize the storage capacity of the warehouse under a limited area;
Enhance-the overall image of the company;
Prevent-packaging loss;
Improve-corporate logistics efficiency;
Improve-corporate management level;
Operation-convenient and safe;
Secang solution:
In view of the above-mentioned customer situation, Shicang recommends the following:


Expansion, densely stored shuttle warehouse, double the warehouse capacity;
Quick access, significantly improve work efficiency;
Reduce manpower and material resources and reduce costs;
Strong operational safety;


At the same time, Shicang believes that the use of shuttle racks with WMS (Warehouse Management System) can achieve: effective batch management, dispatch of purchases, shipments, transfers, batch management, inventory work, and dynamic monitoring of each storage location. Clearly indicate where the goods should be stored to avoid misplacement and picking of the goods, and monitor the operation mode of the shuttle.

In addition, the cold storage project is currently the largest successful case of shuttle racks in Guangdong, and it is also the first case of shuttle racks in the domestic cold storage industry that uses RFID systems.
Through the combination of shuttle racking system and RFID, benefits can be implemented:
1. Complete cargo logistics process management function-timely alarm for incoming and outgoing errors, greatly improving the real-time dynamic management of goods;
2. Real-time collection and recording of the whole process data, through the centralized management of information, to achieve information sharing, reduce labor links, and save time;
3. Provide all kinds of data needed for management through statistics, analysis and processing of data, and provide reliable basis for decision makers.
4. Flexible and easy-to-use RFID technology can easily expand RFID data collection methods in existing management systems.
5. Real-time management, fast operation, detailed records, and complete management links.
6. Improve the accuracy rate of in and out of the warehouse, and the inventory is more accurate.


[ad_2]