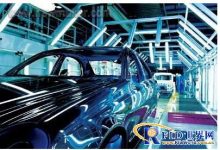
SIEMENS RFID application in automobile manufacturing industry
[ad_1]
After decades of development, China’s automobile industry has entered a stage of rapid development. Through the introduction of technology and independent research and development, large and small joint venture factories and private factories have continuously improved the level of technology and craftsmanship. At the same time, due to fierce competition, automakers and component suppliers are facing increasing pressure. On the one hand, it is necessary to continuously reduce costs, and on the other hand, it is necessary to ensure that its products meet the particularly stringent quality standards of the industry. In recent years, automobile manufacturers have spent a lot of their expenses on production logistics management systems, with the goal of achieving transparent and flexible production logistics and improving production efficiency. The role of RFID technology in material and product tracking has a great impact on automobile production logistics. By deploying the RFID system, the information visualization management of the production logistics process can be realized.
The necessity of RFID in the automotive industry
First, the quality regulations of the automotive industry. As end users have higher and higher product expectations, automobile manufacturers have increasingly strict requirements on product quality, and competition among manufacturers has become increasingly fierce. This requires efficient quality management systems (QM systems) in all areas of the automotive industry. Detailed regulations for obtaining and storing quality data are increasingly reflected in the requirements of the automotive industry’s quality specifications: it must comply with the ISO 9000 certification standards, comply with the relevant legal systems, and conform to the interests of automobile manufacturers.
Second, flexible production. In order to improve production efficiency, automakers are increasingly adopting flexible production lines. That is, multiple models are produced on one line, and one model is painted with several colors. In this case, the production information needs to be written into the RFID tag according to the production plan. In the corresponding process, the relevant production information is read out, and the production operation is carried out according to the pre-set arrangement. To produce multiple models on one production line, how to identify, color control, and distribute materials for different models? All these processes are controlled by RFID. Through the read/write operation of the tags installed on the skid, All information is uploaded to the workshop production process monitoring system PMC through PLC for further processing and calculation, so as to realize the tracking and production process control of the entire workshop workpiece logistics.
Third, pull materials through the MES manufacturing execution system. Before entering the paint shop from the welding shop, the body in white will be stored in the buffer zone of the WBS welding shop. There will be several lines in WBS, which store different car models.
The management system needs to know the position and production status of various car bodies at any time, automatically arrange production according to the production plan, and notify the material pulling system to replenish the corresponding materials, so that the production can be carried out automatically, efficiently, and in an orderly manner. By installing RFID tags on the spreader or skid, installing RFID readers at the fork of the workpiece logistics, the entrance of the paint shop, etc., read the body information stored on the RFID tag, and then send this information The MES system realizes the management of materials. Similarly, the painted car body will be stored in the buffer zone of the PBS paint shop before it comes out of the paint shop and enters the final assembly shop. RFID is also used to control the production process and manage the production information and status.
Fourth, the harsh production environment requirements of the paint shop. The production environment in the paint shop is quite harsh, with not only splashes of metallic paint, but also a baking process with a high temperature close to +200°C. It is impossible to use bar codes in this environment, and RFID must be used to control the steps of the entire production process and trace production information. In the paint shop, the car body recognition technology with RFID as the core is adopted, which can adapt to the needs of flexible manufacturing and realize the following functions:
Realize the precise positioning of all car bodies in the paint shop. As the coating process includes pre-treatment, electrophoresis, spray painting, etc., the use of non-contact RFID radio frequency identification technology can fully meet the requirements of the harsh working environment. For each car body that enters the paint shop, the system can track its current flow position and display detailed information about the car’s model, color, body, model, etc. When the data information is abnormal, it can be fed back immediately.
Painted body deployment. Allocate and manage vehicles in each temporary storage area.
Monitoring of coating quality. Record the important process parameters and quality inspection parameters of each vehicle, and control the vehicles according to the paint batch.
PBS management. For vehicles that pass the quality inspection, control the temporary storage location for entering the color car body. Generally, the horizontal and vertical moving machines used by PBS are composed of horizontal and vertical moving machines. For vehicles entering PBS, it is necessary to be able to easily deploy the sequence. s position.
Fifth, the engine assembly line. The engine assembly line uses the cylinder block as the basic carrier to assemble engine parts into an engine assembly, including the main assembly, preparation area, and inspection links. The focus of control is assembly accuracy, torque, test results and defects in the assembly process. Key components such as chains, generators, and starters are tracked in batches.
RFID is used to record important parameters of the assembly equipment, manage and control qualified and unqualified products in the assembly process, and realize the full-process tracking of production information.
SIEMENS is used in the characteristics of RFID products in the automotive industry
First of all, SIEMENS provides industrial-grade encapsulated RFID tags, which are strong and durable and can withstand the requirements of very harsh industrial environments. If ordinary barcode labels are used in industrial production environments, if they are contaminated and damaged, they will easily cause information reading errors. . Secondly, RFID tags are readable and writable, and information can be rewritten repeatedly. Once the barcode label is printed, it can only be read but not written. In the real-time management and control of production information, the application of RFID labels is more flexible and can fully meet the requirements of automated flexible production lines. Thirdly, the storage capacity of the RFID tag is large and can be selected according to the needs of the process flow. Therefore, the RFID tag is equivalent to a small mobile database that can store a large amount of production quality information.
According to the working principle of RFID, even if the production information can be stored in the RFID tag, once the IT system fails, it will not affect the work of the RFID system, that is, it will not have much impact on the production process. If a barcode is used, only the ID number of the container or pallet can be stored in the barcode. The information of the raw material and workpiece in the container or pallet is stored in the database system, and the ID number is associated with the information in the database. Once IT system failure occurs, it will affect the management of production information in the production process.
In addition, the SIEMENS RFID system can be easily integrated into the SIEMENS PLC, that is, the information communication between the field level and the control level is extremely convenient. Moreover, the operation of the control layer by the upper computer management system software is very easy. Therefore, the SIEMENS-based RFID and PLC and the upper-level MES management system constitute a complete set of fully integrated automation solutions without the need for the development of additional management systems.
Application of SIEMENS Moby I in Shanghai General AVI System
Shanghai GM uses SIEMENS Moby I products in its four factories in Shanghai, Shenyang, and Yantai in the AVI automatic vehicle identification system to improve production efficiency.
For example, SIEMENS automation and control technology is used in the paint shop, BDC (car body distribution center) and part of the final assembly shop in Shanghai GM’s South Plant. The AVI automatic car body recognition system is used to identify car bodies on high-complex production lines. It is required to produce four models of different platforms on the same production line, and complete the automatic identification and tracking of car bodies in different process segments and the control of the production process through the AVI system.
SIEMENS Moby I product solution: AVI automatic body recognition system controls welding, body distribution center, and painted body until the body is transported to the final assembly. Each AVI system is connected to the factory information system FLEX/SFE via Ethernet. The AVI system requests production data from the FLEX/SFE system, or sends car body information to the FLEX/SFE system. Through the FLEX/SFE system, you can understand the location of a particular car body and what stage of production it is in. The production efficiency is improved by arranging the car bodies of the same color coming from the car body distribution center to be sprayed together.
The body-in-white from the welding shop enters the paint shop through the body distribution center BDC for electrophoresis, sealing and spraying. After processing, the car body is sent to the assembly shop for further assembly through the car body distribution center. Through the AVI system composed of SIEMENS Moby I system, the whole process is tracked.
Using this technology, you can first get a good understanding of the location of the car body in the scene, and secondly, you can exchange information with the IT department to determine the process for the car in the paint shop.
The division of tasks at AVI sites is different. Some sites request data from FLEX/SFE before the start of the car body and write it into the code carrier on the skid or spreader; some sites start from the skid or spreader. The data is read from the code body and sent to the FLEX/SFE system; some sites can initialize the code body or clear the content on the code body at the end of the process.
Shanghai GM adopts the AVI system with SIEMENS Moby I as the core to realize a flexible production method of co-production of multiple models, improve production efficiency and shorten the production cycle of new models.
SIEMENS’s RFID products have been widely used in the automobile manufacturing industry with their excellent performance and stability. Various automobile manufacturers at home and abroad widely use SIEMENS RFID products in the four major process stages of automobile manufacturing, including stamping, welding, painting, final assembly and engine assembly. In addition, many auto parts suppliers and OEM equipment manufacturers have also generally adopted SIEMENS RFID for production and manufacturing, and significantly improved production efficiency.
[ad_2]