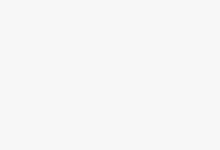
Successful application of barcode production management in Tianjin Motorola Battery Factory
[ad_1]
1. Background
The system does not make major changes to the existing production process, emphasizes the use of bar codes and other mechanical means to replace manual data collection, saves all complete data for the entire production process (incoming materials, QC, equipment personnel attributes, and shipments), analyzes them, and finds out problems , Improve productivity and management level.
2. Status and problems of production management in Tianjin Motorola Battery Factory
The current production management of Tianjin Motorola Battery Factory has a certain level. For example, the production environment is very orderly, the process equipment is advanced, and the quality management system is relatively complete. However, under the existing manual management conditions (referring to production, quality inspection, equipment, materials, personnel Etc.) The potential for improvement of management level is relatively limited.
2.1 Management methods are obviously lagging behind processes and equipment, and have great potential for improvement
At present, it still relies on manual work in quality inspection and equipment maintenance. Only by relying on machines can comprehensive field data be collected in a large amount and in real time at a low cost. The data collected by the computer can be analyzed and summarized in real time, and senior managers can conduct on-site management on the desk. Manually collected data generally has a long time lag, and only system integrated data can provide in-depth diagnosis and timely correction of problems.
Most of the time, the production equipment is operating normally, but there are some problems in some parts. Although these problems are clear, the problem-solving methods and methods are backward, and the ability to analyze and solve problems is insufficient. Many problems, such as dropped parts, cannot be quantified.
2.2 The mining of management benefits needs to rely more on system methods and comprehensive statistics and analysis of field data
Most of the ledgers are manually registered on paper, and then summarized into a simple Excel-based table. Generally speaking, the human error rate is 1/200, and the machine is 2 to 6 millionths. Management methods rely more on the observation and experience of managers and quality inspectors, rather than relying on objective multi-level quantitative data analysis of unmanned factors.
2.3 On-site management (quality/equipment)
There is still great potential for improvement in quality and equipment management. In quality inspection, online workers have greater authority, and the control process is also more arbitrary. Incoming QC currently mainly relies on vendors to do it (vender), which has potential risks. Sampling does not meet the SPC requirements. For example, taking 5 for every 200 on the second floor is not a true random sampling. The factors that cause equipment problems may be more complex, and the manager’s experience is powerless, and many factors require complex data analysis to solve them. Equipment management lacks standardized work, and problem diagnosis lacks comprehensive and complete database support to obtain objective and accurate answers.
2.4 There is room for improvement in the production scheduling method
In terms of production scheduling, manual scheduling is less effective when resources conflict, and multi-factor program scheduling is particularly effective when scheduling small batch production.
At present, the production is arranged manually based on whether the product delivery date and material preparation are complete. The implementation of a more reasonable method lacks a complete database as a basis. For example, the stock inventory lacks real-time and accurate information and orders have not been placed on the basis of future needs, and the attributes of various products and equipment also lack organic data correlation.
2.5 There are gaps in basic management work (standardization work)
Computer-optimized resource management depends on the complete standardization of management basics, such as design, production, and planning quotas, working hours quotas, equipment quotas, barcode applications, and so on. Basic standardized management requires a relatively complete database that is easy to input and analyze. Combined with bar code equipment, data collection and sorting will make this daunting tedious task easy.
2.6 Timeliness and coordination
There is no means of fast entry and real-time data transmission. QC finished products and spare parts inventory, equipment maintenance and other information are seriously lagging behind, and managers are currently difficult to manage in real time. Forecasting is even more impossible.
Modern enterprises rely on the comprehensive coordination and processing of various resources and information, and the lack of accurate and smooth interaction between various departments and teams makes top managers face overall coordination difficulties.
3. Ideas for solving production management problems in Tianjin Motorola Battery Factory
3.1 Change in leadership thinking
The advancement of information management is not about investing in the design and installation of a good system to achieve results. The benign interaction between the manager and the managed person and the system depends on the improvement of people’s quality. The biggest challenge for leading enterprises in quantitative information management comes from the support and transformation of middle-level cadres. But with the right tools, this transition will be easy. The tools of this information system should be easy to implement, without making major adjustments to the status quo, and with immediate effect, making management more efficient. Combined with barcode recognition technology, the feasibility of the system is far more acceptable than the non-barcode tutoring system.
3.2 Reasonable adjustment of management system
The management system and production process are easily optimized and adjusted. Use machines as much as possible to replace manual information collection with fast beats and reduce collection points. The efficiency is improved, the cost is reduced, and the process is more reasonable and smooth.
The operations of system managers and executors are also optimized. From complicated to simple, from more actions to few actions or even no actions. If you use the default value to replace the keys, use the keyboard instead of manual recording. The production process can also be processed in a class. For example, use barcode scanning to replace all models, quantities, employees, and operating instructions logged in.
3.3 Targeted system application
The system does not design specific solutions for specific problems, and gradually increases in stages from the shallower to the deeper combined with the actual situation and the worker’s ability to cope. This is a relatively long-term job.
3.4 Grasp basic work
Training should be conducted before entering the system, job standards should be customized, and inter-departmental coordination should be done, otherwise it will cause confusion. At the same time, standardization work must be carried out. This task requires customizing a special database supplemented by easy collection tools such as bar codes to make it easier to implement.
3.5 Improve professional management level
Existing manual management analysis methods are difficult to solve more complicated management problems, and these problems are difficult to judge and solve based on experience alone. Deeper methods require powerful and easy tools. Professional management requires complete data-based analysis tools. For example, is the reason for the equipment drop related to the product, team, maintenance gap or some combination of them? This requires systematic analysis of historical data to find the cause.
3.6 Organizational changes
The new system may bring about changes in personnel organization. The definition of different levels will change. For example, the neat handwriting of handwritten account staff will become less important than the quickness of inputting codes. Due to new requirements, some categories of personnel will increase or decrease accordingly.
4. Specific solutions
4.1 Production Ledger Statistics
First, replace manual accounts with electronic accounts. Manually recording the ledger and then summarizing the timeliness is poor, the amount of information is small and the error rate is high. The electronic ledger is real-time, with low error rate and fast entry speed, most of the data will be set as default values.
For example, it is the first to use electronic accounts in terms of incoming materials and production statistics.
4.2 Quality inspection account statistics
Electronic ledger entry is used to design the best inspection points, and the quality inspection reports are dynamically transmitted in real-time and summarized and analyzed.
The decision-making power for major quality issues is based on the mechanical real-time data statistics, completely eliminating human factors. If the production line is shut down and a batch of products is scrapped based on incomplete reliable information, it will bring huge losses to the factory.
4.3 Barcode application
Barcode technology will be applied to quality inspection, identification, ledger entry, incoming and outgoing management, and some management functions, such as employee permissions, areas and other fields.
4.4 Data analysis
Complete data enables the system to perform multi-level and complex analysis-discover complex problems involving multiple factors. The system will establish a complete large-scale database in terms of personnel, equipment, quality inspection, product flow, etc., organically combine these factors and provide powerful analysis tools. Managers can put forward hundreds or even thousands of reference results according to their needs. . Commonly used valid data will be presented on the desktop of the authorized person in real time.
4.5 SPC
At present, the manual input of summary data makes the quality inspection lag in time, and the loss may have occurred before the problem is solved. The system will collect and transmit data in real time and analyze on-site to make a conclusion. The system will coordinate with the production line at the same time, such as a 15-minute collection interval on a certain line. Managers can monitor the quality status in real time. The system will automatically judge and react.
4.6 Automatic warning
On issues related to quality, raw materials, process conflicts, etc., the system will automatically prompt the attributes that require early warning based on presets, thereby reducing human error.
4.7 Equipment monitoring
The electronic ledger is used to automatically record the equipment status in synchronization with the production, and analyze the basic information of equipment production, such as operators, production teams, production products, maintenance status, error rate, time, etc.
The system database saves complete and dynamic data of major equipment and constitutes an analysis of organic factors. Ensure that all equipment reaches nearly 100% operation rate. Preventive maintenance of equipment to find out the reasons that affect equipment problems, such as specific time, personnel, products, maintenance intervals, etc. At the same time, the smallest spare parts are maintained to save space and money.
4.8 Storage of equipment spare parts
The use of bar codes can maintain the minimum amount of spare parts required for operation and storage. Use the historical information in the spare parts account to find the best time and quantity. At the same time, the barcode technology makes the inventory easy and the parts position accurate.
4.9 Purchase
The system can be combined with production forecast scheduling for electronic order placement.
4.10 Warehousing
The system can use real-time wireless barcode technology to provide dynamic real-time product inventory.
4.11 Consultation and training
The training of employees or management personnel can be carried out in response to the needs of the factory.
5. Project Planning and Arrangement
The success of the system lies in its good operability, gradually implemented from the shallower to the deeper.
5.1 The first stage
First, carry out basic construction such as standardized training, solve the problem of using barcode equipment to replace manual entry, using electronic ledger instead of manual ledger, design inspection points, preliminary analysis of statistical reports, and generate preliminary quality inspection production and other management data.
5.2 Second stage
SPC real-time quality inspection and statistical judgment, the manager monitors the production in real time, automatically warns, and uses barcode technology to control the entry and exit and inventory in real time in logistics and warehousing.
5.3 The third stage
Establish an equipment account, establish a spare parts warehouse system, and optimize management.
5.4 The fourth stage
The system schedules production, connects with MRP and controls it.
The system coordinates production, manpower, equipment, storage and other parallel elements, so that production is stable and errors are avoided. High-level management makes the production potential reach a high level.
6. Expected benefits of the project
After the system is fully implemented, the following expected effects will be achieved:
6.1 Equipment Operation Rate (utilization)
The equipment operation rate is increased to nearly 100%, while unnecessary maintenance and manpower are reduced, and spare parts storage is reduced. System analysis reduces downtime to a low level.
6.2 Reduction in personnel
Appropriate application of barcode to identification, collection of quantity, entry into account, plus rational design can improve personnel efficiency.
Using barcodes and keyboards instead of manual entry, the manpower efficiency can be increased by more than 70%, and the accuracy rate is improved (the error rate is reduced from 1/200 to 1 in 2 million).
6.3 Quality inspection using statistics
The comprehensive and scientific quality inspection system automatically makes accurate judgments by the machine. The powers and responsibilities of general quality inspectors have been greatly reduced. Reduce human factors and improve the accuracy of quality inspection. Good products will not be scrapped by mistake, and real waste products will not leave the factory.
6.4 Ideal state inventory
Reduce warehouse space requirements and capital backlogs, and reduce costs.
6.5 Real-time benefits
Notify the management system of problems in real time, provide immediate solutions, and eliminate major losses caused by delayed discovery and processing.
6.6 Management benefits
Change the working methods of professional management departments, quantitative analysis and reduce subjective errors. The real-time nature of the system turns the problem-solving into an ongoing matter.
[ad_2]