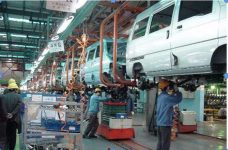
The application scheme of RFID technology products in the manufacturing industry
[ad_1]
Since the implementation of reform and opening up in 1978 for more than 40 years, my country’s manufacturing industry has developed rapidly as a world power, no matter from the perspective of the improvement of people’s living standards, economic development, or national security, it needs a strong, independent and independent manufacturing industry. The emergence of the new industrial revolution is not only a challenge, but also a rare opportunity. my country has entered the late stage of industrialization and is in a critical period of economic structural transformation and upgrading. The new industrial revolution has promoted the birth of a large number of new technologies, new industries, and new models, laying a technical and economic foundation for the development of my country’s industry, clarifying the future development direction, and also for my country’s scientific formulation of industrial development strategies, accelerating economic transformation and upgrading, and mastering development. Initiative provides important opportunities. Let’s take a look at the application of RFID technology in the manufacturing industry together ——
The RFID electronic tags on the production line use RFID technology to realize automatic control and monitor products on the production line, which greatly improves the speed and accuracy of production, improves work efficiency, improves production methods, and saves costs. RFID tags conveniently and accurately record process information and process operation information to meet the needs of flexible production. RFID technology is used to realize automatic control and monitoring on the production line, increase productivity, improve production methods, and save costs.
1. RFID demand analysis in the manufacturing industry
Manufacturing production lines consume a large amount of materials almost every month, and production results and expected errors affect delivery from time to time. Production lines often cause various errors due to human reasons. Attaching RFID tags to production materials or products can automatically record the quantity, specifications, quality, time, person in charge and other production information of the product, instead of traditional manual recording; the production supervisor can read the product information through the reader at any time; other related The personnel can grasp the production status in time and adjust the production arrangement according to the situation; the purchasing, production, and storage information are consistent and can be monitored in real time; the system will automatically record the warehousing information before the materials and products leave the warehouse, and can track the location of the items in real time.
In the industrial link, RFID technology is used to assign an identification number (ID) to each work-in-progress component, which is the name of the component in the information network. Through RFID technology, the production status and inventory status are mapped to the information network and registered in the information network. In the field center database, it is transmitted to the information system. Applying RFID technology to production line monitoring can realize automatic control and detection and save costs. RFID tags can uniquely identify each product, and record the raw material and source, production line location, production process and inventory status of each product through the application, and provide an effective basis for companies to better manage production and adjust inventory.
Second, the application characteristics of RFID in the manufacturing industry
2.1 Real-time data sharing
In the production process of a manufacturing enterprise, it is very important for the production line to feed back information in a timely and accurate manner. In the past, it was only possible to record faults manually while producing. After the production is completed, the statistics and summarization of the information from each process is time-consuming and laborious, and sometimes it cannot be very accurate. Install RFID reading equipment in each process of the production line, and place RFID electronic tags that can be read and written repeatedly on products or trays. In this way, when the product passes these nodes, the RFID read-write device can read the information in the product or the label on the pallet, and feed this information back to the back-end management system in real time, so that the manager can understand the working status of the production line in time. .
2.2 Standardized production control
The RFID system can provide a constantly updated real-time data stream, which is complementary to the manufacturing execution system. The information provided by RFID can be used to ensure the correct use of machinery, equipment, tools, and parts, so as to achieve paperless information transmission and reduce downtime. Furthermore, when raw materials, parts and assemblies pass through the production line, the production process can be controlled, modified and even reorganized in real time to ensure the reliability and high quality of production.
2.3 Quality tracking and tracing
On the production line where the RFID system is implemented, the quality of the product is tested by a number of test posts distributed in several places. At the end of production or before product acceptance, all previously collected data must be able to clearly express its quality. This can be done easily with RFID electronic tags, because the quality data obtained during the entire production process has already been taken off the production line with the product.
3 The application principle of RFID in the production line
The current bar code-based production management system enables various quality analysis and control to be easily realized. The bar code technology has its advantages as well as its obvious shortcomings, such as easy to be contaminated, easy to be damaged, short scanning distance, etc., batch reading The efficiency is not high and cannot meet the needs of fast and efficient. Use RFID electronic tags, barcodes, and sensors to collect real-time data on the production line, and transmit the read data to the upper device (controller or computer) through the network (wired or wireless). However, to manage loose sensors requires a brand new, The management mechanism of the network can be automatically discovered and organized. The method adopted is to deploy RFID readers and establish reader network connections at the same time to solve the problems of planning, optimization and control of the reader network. The RFID tag on the item, together with the RFID reader connected to the network, each identification means a tracking of the item.
[ad_2]