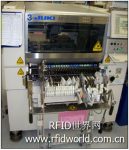
U.S. circuit board manufacturers adopt RFID tracking circuit integration
[ad_1]
NBS Corp., a circuit board manufacturer in Santa Clara, California, uses RFID tags on the component rolls of circuit board integration machines to track specific components and their locations on the circuit board. By monitoring this kind of information, the company can not only ensure the correctness of the component installation position, but also store the relevant data of the integrated circuit board, so that the corresponding data can be traced in the event of a component failure or a manufacturer’s recall. To equip the integrated machine with RFID functionality-provided by Juki Automation Systems-NBS uses Cogiscan’s RFID tags, readers and software.
NBS provides circuit boards for various equipment users. In many cases, the normal operation of the circuit boards is of great importance. For example, NBS is a medical implanted device, such as a pacemaker, which produces circuit boards. The normal functioning of these circuit boards is vital to life and is one of the most concerned issues, said Peter Chipman, NBS test director.
When a small trailer is inserted into a circuit board integrated machine, the system uses RFID to confirm that all feeders and component rolls are still in the correct positions
The components are packaged in the form of “tape and reel” when they arrive at the assembly plant. The reel is designed to feed into the automatic placement machine and place the components on the circuit board.Each roll of components is identified by a barcode label. The serial number of the label corresponds to the part number, batch number and other specific information of the component. All of this information is stored in a central database.
The company uses a strict system of checks and balances, Chipman said, to ensure the normal integration of circuit boards (containing 100-200 components such as resistors, capacitors, switches, and LEDs). This includes a close inspection of the component roll placement by several workers, ensuring that each component is installed in the correct slot of the trailer, and then inserting the trailer into a circuit board integration machine. In this way, the company can confirm that the components are installed in the correct position on the integrated circuit board.
Each feed chute of the trailer is equipped with a small antenna
After the integration is completed, the worker conducts a series of inspections on the circuit board to reconfirm the installation of the correct components. Since the company usually produces 5,000 circuit boards a day, the settings of the machine and the component rolls of the small trailer often need to be replaced, which makes the traceability process more complicated. If a component fails and is recalled by the manufacturer, it will be difficult for NBS to determine the source and batch of the component, nor can it trace the circuit board using this batch of components.
Peter Chipman fingered the RFID tag of a feeder
The company now uses Cogiscan’s RFID technology and Juki IFS-X2 intelligent feeding system. Before production, workers load each roll of components into its own belt feeder-a fixture that sends the components one by one to the required integrated machine. Each tape feeder is identified by a serialized barcode label, including a low-frequency 125 kHz RFID label using a proprietary air interface protocol. When the component roll is loaded into the feeder, the operator uses a handheld machine to scan the barcode label of the component roll and the feeder, and correlate them in the database. In the second step, when the feeder is loaded on the small trailer, a reader-equipped with a row of small antennas (one antenna per feed chute)-reads the tag. The reader reads the unique number of the tag, and then sends the information to the software of the company’s back-end system. According to the position of the antenna that reads the ID code of the tag, it is determined that the component roll is placed in a specific slot.
The software then judges whether the component roll is installed correctly or whether it is installed in the correct slot according to the type of the integrated circuit board and the machine program. Once the configuration takes effect, the small trailer is inserted into the machine (some machines can accept four small trailers at once). When the small trailer is installed in place, the system again uses RFID to confirm whether all feeders and component rolls are in the same position for the integrated product. If a volume is found in the wrong slot, the machine instructs to stop the integration, and an alarm flashes on the display, telling the worker to remove the wrong component volume and reinstall it.
During the integration process, Cogiscan President Francois Monette said that each circuit board was printed with a barcode serial number, and a camera mounted on the machine took pictures of the serial number. In this way, the company can record the specific circuit board and its receiving component rolls, and the location of the components mounted on the circuit board.
“In the final stage of production, if each process is OK, the system writes all data to a file, including the serial number of the circuit board,” Chipman said.
“We started to provide this solution for medical device companies,” Chipman said. Customers are willing to pay for the increased technical costs. This system is not designed to save man-hours, but to provide component records of the circuit board. Chipman claims that litigation costs caused by a bad component may be higher than the cost of the entire system.
NBS initially adopted this system for only one of the five assembly machines to track the component data of medical equipment circuit boards. However, Chipman stated that if the system continues to work normally, the company plans to use the system on all integrated machines.
[ad_2]