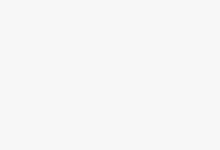
Uboxun helps Neptune Star to realize the automation and systematization of warehouse management
[ad_1]
Project Background
In recent years, private chain pharmacies represented by Neptune Star and the common people have expanded rapidly. Due to the excessive variety of drugs and the scattered customers with too many bills, chain pharmacies companies after the rapid expansion have encountered various information flow processing. The problem. Starting from the first community retail pharmacy in 1996, Neptune Star has more than 3,000 chain pharmacies, and there are tens of thousands of regular drugs that need to be purchased. How to standardize and organize the complicated drug types and a large number of business documents in a timely manner It is difficult to understand the inventory of each product and display it in an intuitive information platform.
Customer needs survey
According to customer surveys, it is learned that Neptune Xingchen mainly has the following problems in warehouse management:
1. In traditional manual accounting and inventory counting, there are often missed and wrong orders, resulting in inaccurate inventory data.
2. Putting on shelves, moving goods, sorting or moving goods, and out of warehouse operations in warehouse management are heavy and time consuming.
3. Unable to transmit data in real time, compare inventory differences, and it is difficult to share information.
System function description
PDA application
1. Login: The warehouse manager enters the employee number and password to log in to the PDA terminal system, and the system verifies whether the user information is correct according to the user downloaded to the PDA.
2. Warehouse acceptance: The replenisher/inspector scans the goods in the acceptance area and enters the purchase order through the PDA terminal, and saves it as a warehouse receipt to confirm the acceptance operation.
3. Inbound and shelves: The tally clerk scans the barcode label of the product according to the inventory and puts it on the shelf according to the position indicated by the system, and finally scans the barcode on the shelf to confirm the completion of the shelf.
4. Scanning for moving goods: The tally clerk scans the storage space of the moved product after receiving the notification of the goods removal. The system lists the goods in the storage space. After the operator selects the specified product, scans the product and enters the moving quantity, and finally scans the new product according to the system prompts. The shelf barcode confirms the completion of the transfer.
5. Dismantling and replenishment: The tally clerk downloads the product details that need to be dismantled and replenished from SAP, then scans the area and enters the amount of dismantling and replenishment, and finally confirms the submission.
6. Picking and distributing: the tally person scans the channel number through the terminal SAP, downloads the task details of the channel to be picked, then picks up the goods according to the instructions and loads them into the box, scans the picked box number, and enters the actual picking quantity, etc. Confirm that the picking is complete.
7. Packing and shipping: The tally clerk scans the product to query the product information and the corresponding store, and records the shipping information after confirming the shipment, and uploads and submits it.
8. Business inquiry: through the terminal, you can inquire about the outbound/inbound list, the information on shelves, moving, and picking, and the strategy of dismantling and replenishing goods, etc.
9. System settings: The operator can set the warehouse to which the terminal belongs and network access, and can also bind the ID number of the tally.
10. Data download: You can download product data from the background SAP through the terminal, download the login personnel, download the shelf document, query the product information of the location, download the picking document, query the shipping data, etc.
System application effect
Automatic data collection
All data is automatically collected, which greatly shortens the time for Neptune Stars to enter and exit the warehouse, saves labor costs, and improves the efficiency of warehouse operations.
Accurate transmission of information
Real-time transmission and update of warehouse information solves the problem of outdated and lagging warehouse information. Correct purchase and delivery and real-time inventory control ensure the efficient use of corporate resources.
Real-time storage of electronic data
Electronic data replaces the traditional storage method of paper text information, improves the accuracy of data statistics, and facilitates Neptune’s future document query and recall work.
?Accurate warehouse operation management
The full application of the barcode system realizes single product tracking, shelf life management, batch management and product quality traceability in Neptune’s warehouse operations.
Program summary
Neptune’s warehouse barcode system solution is based on a handheld terminal PDA, and uses wireless network to interact with the back-end SAP system to achieve efficient and high-speed operation of warehouse management. The Uboxun handheld terminal used is small in size and easy to carry when handling and organizing items. Once the solution is used, it not only improves the work efficiency of Neptune’s warehouse staff, but also enables timely inventory scanning during the movement or handling of medicines. At the same time, through the terminal inventory system, the inventory situation can be understood more clearly, thus completely solving the difficult problem of Neptune’s warehouse management.
[ad_2]