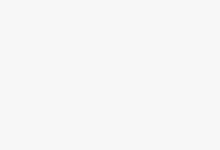
Uniform rental automation relies on RFID
[ad_1]
With the continuous development of RFID tag materials, the durability of tags has increased, including: water resistance, heat resistance, pressure resistance, alkali resistance, etc., allowing RFID technology to penetrate more service applications. Uniform rental industry is an innovative application .
Grantex uniform rental service company is a uniform rental service company in the United States. Its customers are as many as 1,000 companies. It needs to send up to 6,000 uniforms per hour to different customers. In order to provide better customer service quality, Grantex decided to introduce RFID technology to its new processing plant in Michigan in the last (2007) year, hoping that this new technology can reduce the delay in uniform processing and delivery operations.
Need new technology to improve processing efficiency
In the previous manual operations of Grantex, the employees of the processing plant had to start the relevant steps of the field operation after receiving the uniform, including hanging the identification card (Figure 1), (pushing the hanger) moving, (after registering the data) Hanging, packing, reorganization, etc., after these operations, uniforms can be classified and stored. Because Grantex has many customers and many types of uniforms, and the uniforms of a single company are often different by job or job attributes, a single staff member may also be in different workplaces (such as operating rooms and wards) or seasonal ( For example, winter and summer) different combinations of clothes (such as jackets, short-sleeved tops or long-sleeves, etc.), and the size and color of the clothes are not compatible with the differences in the combination. These must be identified in the operation before they can be reorganized. Good uniforms are smoothly categorized so that they can be rented out later.
Figure 1. Grantex employees hang identification tags on different uniforms
Therefore, this new RFID system must be able to achieve the following functions:
Reduce delays in the delivery of clean uniforms.
Reduce the inaccuracy in the processing.
Reduce errors in manual processing.
RFID system application scenario
To meet the application requirements proposed by Grantex, the first thing is to be able to grasp the status of uniform items in the warehouse in time. Due to the manual operation in the original factory, input data errors (such as clothing size) or incorrect quantity counts (such as multiple pieces of clothing) may be generated. As shown in Figure 2), these visual or manual omissions may affect the effective quantity of clothing in the warehouse, as well as the evaluation of the subsequent rental and return quantity. In this way, reasonable shortages and waste may occur. (Refer to 1)
Figure 2. When multiple pieces of clothing are fed in, manual operations may be incorrect
The system integration manufacturer TAGSYS uses special RFID tags and related hardware as a solution to this problem.
In this case, the Ario™ SL microtag is attached to the neckline of each uniform (as shown in Figure 3). The tag contains an identification code for tracking and subsequent classification of objects during the washing process. Use an RFID reader to write the size of the clothes, the steps to be washed, the name and address of the customer using the uniform, and write the identification code. Due to the needs of the operation, the label must be completely waterproof, chemical material, able to withstand 400 degrees high temperature and can withstand It weighs 100 pounds per inch (because there will be electric ironing and flattening).
Figure 3. The RFID tag in this case contains an identification code
The RFID reader and antenna are integrated into a three-dimensional channel (as shown in Figure 4), which can identify piles of clothing entering the processing plant and ready to be shipped out of the packaged clothing. This three-dimensional channel will help speed up the reading The identification data on the tag and the data of these objects are transmitted back to the RFID clothing management system provided by TAGSYS. The on-site workers’ operations after receiving the clothes can be supplemented by a handheld reader to accelerate the identification and subsequent classification of the clothes, and store them in the inventory rack according to the type and size of the clothes.
Figure 4. Three-dimensional channel integrating RFID reader and antenna
Now, Grantex has a clearer grasp of the number of uniforms available for rent. These finished clothes are delivered to the service counter. The staff at the counter can easily pick up the RFID tags on the clothes so that they can clearly know which staff should wear them.
Better customer service
Through this RFID clothing management system (as shown in Figure 5), Grantex uniform rental service company can now handle clothing more efficiently:
Automated clothing sorting: In this way, Grantex speeds up its uniform handling process and can now deliver it to customers 4 days in advance compared to the schedule required by customers.
When clothes are delivered to individual customer managers, individual uniforms can be more reliably identified to different positions such as management, employees, cleaners, maintenance technicians, etc. This operation becomes simpler and more precise.
Once the uniforms provided have defects in quality, they can be traced back to the processing center.
Reduce errors in uniform delivery and improve uniform management quality.
Figure 5. RFID can accelerate the classification and tracking of clothing
Grantex President Douglas Singer said: “Compared to the previous time schedule for customer requirements, which can be 3 days earlier, this new system allows us to deliver to customers 4 days earlier, and our work schedule can still be maintained. Class (from 6 in the morning to 2:30 in the evening). “We can do it now. The greasy clothes we received yesterday can finish all the processing work and hang it on the storage rack before we get off work today.” 』(Refer to 1)
Uniform rental automation
In addition to achieving the original goal set by Grantex, the use of RFID technology in the uniform rental service industry can also reduce the risk of uniforms being lost and being taken out by unauthorized persons for speculation (for example, police or physician uniforms). Since the uniform rental industry has traditionally set a certain loss rate for the corporate customers it serves, when the rental service company finds that the clothing is short, most of it will absorb it on its own (unless the quantity is large). The relative corporate customers’ loss of their own uniforms , The uniform is usually not or cannot be tracked.
Now, RFID tags are directly attached to uniforms, which can be found in this RFID clothing management system no matter in the stitching or drying stage. Manufacturer TAGSYS also found that the automatic or semi-automatic classification provided by RFID technology can greatly reduce uniforms. The manpower required by the rental company; even, the uniform rental service company can directly set according to the customer, and the specific uniform will automatically fall into the discarded category after a certain number of times. In this way, the company’s worthless uniform inventory can also be reduced. With these hoardings, the company’s operating profits will naturally increase.
This derivative application can also be applied to uniform management of hospital medical staff or military and police.
Reference materials:
1. An RFID-enabled Uniform Service Plant
2. TAGSYS RFID tunnels
3. TAGSYS offers a full range of RFID systems
[ad_2]