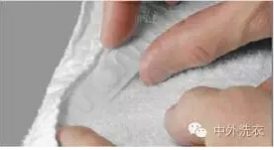
Why does the most advanced laundry factory in the UK use RFID technology?
[ad_1]
The most advanced laundry company in the UK-Fisher Textile Services has adopted RFID radio frequency identification technology in its new laundry facility in Glasgow. The laundry factory reads the chips sewn on the linen and the chips installed on the bags and cage carts. The manager of the factory can see the state of the linen: whether the linen is sorted in the factory or being washed, or On the way to the customer or already delivered to the customer.

The company’s new laundry facility in Glasgow serves 300 hotels within a 50-mile (approximately 80 kilometers) service radius. In order to reduce the loss of linen, Fisher Laundry has installed RFID chips on the 4000 laundry carts and more than 7000 bags in the laundry factory. Nearly 200,000 pieces of linen leased by the laundry factory from the hotel are also pre-installed with RFID chips by the supplier. (For reports on Fisher’s most advanced laundry factory, please refer to the April 2016 issue of “Chinese and Foreign Laundry” magazine)

The customized software system can track multiple data of the linen and its movement trajectory. It can monitor the linen return speed (the number of days it takes for the customer to return the linen), the linen return ratio (according to the number of bags received or the number of laundry carts), and the time spent by the linen in the laundry factory. Because this technology can track each piece of linen, it can even give the number of times each piece of linen is washed and calculate how many times the linen can be washed before it needs to be replaced.
The software can also provide a 30-day warning that the linen has not returned to the factory. When a piece of linen is in the hotel for more than 30 days, the software system will automatically alarm. This function allows the laundry factory to communicate with the hotel as soon as possible to ensure that this type of linen is not lost. Customers can also log in to the software system with a password to understand the status of the linen. Through a standard network interface, customers can observe the status and trends of the linen they receive in real time. Customers can clearly see their linen consumption levels according to different categories.

Fisher Textile Services estimates that the seven laundry factories it owns will lose approximately £1 million worth of linen each year. Therefore, Fisher will successively install RFID chips in all of its factories to reduce the loss of linen.
The British Fisher Textile Service Company uses UHF tags (ultra-high frequency RFID chips) to track the receiving, washing and transportation of linen, so it can know where the linen is and which ones are delayed and which ones are lost.
By installing RFID chips, the laundry factory can not only better manage the linen inventory to prevent loss, but also let customers know the status and data of the linen.

Since 1900, Fisher has been doing work clothes and linen washing business throughout Scotland where his headquarters are located and northern England. Now, the company rents sheets, quilts and towels to hotel and restaurant customers all by means of leasing washing. These customers handed the dirty linen to the nearest Fisher laundry factory for washing, drying, folding, and then returning to the laundry factory.
Fisher has been growing. Fisher washes, irons, and delivers more than 2 million pieces of linen every week. In March of this year, Fisher established the most modern “super laundry factory” in Glasgow. The company serves more than 2,000 hotels, and the new laundry facility in Glasgow serves 300 hotels. Through upgrading and transformation, the current production capacity of this laundry factory has doubled.

The company earns 36 million pounds (US$52.7 million) per year, but the annual loss of linen costs is as high as 1 million pounds (US$1.5 million). To this end, they wanted to find a convenient solution to track the linen in and out of the laundry factory and track when and where the linen was lost.
In the past few years, Fisher has been tracking RFID’s solution for linen inventory tracking, but only recently has RFID made a breakthrough that can withstand repeated washing. Although there were breakthroughs in this area, many difficulties were encountered during the trial process. One of them is that the RFID system must be turned on 24 hours a day, so that the read data can be collected and accessed, but this also means that other software systems in the laundry factory also need to be turned on. Moreover, the company also wants customers to see the data of the linen they use or the data of the washed linen from this system, but this requires Fisher to allow these customers to enter its IT system, which will cause security problems. .

Ubisoft offers a better alternative because its system is provided with the hardware, including the touch screen that enters the cloud server software system. This makes the operation easier.
Fisher installed an entrance with readers and circular polar antennas to receive dirty linen in the new laundry in Glasgow. The other two readers are installed on two dirty linen conveyor belts.
After washing and sorting, the linen is placed in a laundry cart or bag to be delivered to the customer. In the process of delivering these laundry carts or bags to the delivery platform, employees push bags with linen and laundry carts through a tunnel reader that is a bit like a cabin. In this position, the employee uses the touch screen to select the customer to whom the linen is to be delivered, and at the same time selects detailed data related to the linen delivered, such as the number of towels, sheets or tablecloths. This information is then recorded along with the unique identification number of the bag or laundry cart containing the linen.
When the dirty linen is sent back from the customer, the linen is sent to the washing area via a conveyor belt. The reader installed on the conveyor belt will capture the tag ID numbers of the laundry cart and linen, and update the data in the software to indicate which linen has been sent back. Once these linens are received by the washing area, the tags will be read again. The purpose of this is to achieve information redundancy and record the actual linens that have been washed.
Fisher’s goal is to master real-time data on all linens. If the technology continues to improve, Fisher may install RFID readers in some customers’ hotels, or provide these customers with handheld readers for greater visibility. The key to return on investment will revolve around the ability to confirm that the linen sent to the hotel has been sent back, so that you can avoid sending more linen to the customer to replace the original linen. Linen.

In the long run, Fisher expects that the intellectual capabilities of this system can help Fisher managers make decisions about Fisher products, such as which type of linen needs to be replaced more frequently. This system may also help Fisher reveal which customers have a higher rate of loss or damage to the linen rented by them, so that the company can work with such customers to find solutions to such problems.
Fisher did not install RFID chips for all linens. If the value of the chip exceeds 20% of the value of the linen itself, Fisher will not install RFID chips for these low-value linens.
[ad_2]