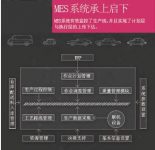
With the help of RFID, JAC successfully implemented the MES system
[ad_1]
As early as 2003, the ERP system for passenger cars was completed, and the annual output at that time was less than 10,000 units. In the case of low output, the company’s requirements for production schedules, plan changes, and material management are not very high. However, when production increases, JAC’s production needs to meet the above requirements, and has higher and more comprehensive requirements for the continuity and accuracy of planned time, the timeliness of material supply, and the integration with automation equipment. In view of this situation, Jianghuai Automobile decided to start the construction of the MES system.
The Jianghuai Automobile Information Department has conducted multi-party research and program comparisons, and referred to some successful cases. During the MES system inspection stage, they also considered whether to use foreign MES systems, but because the environment of each company is different, the requirements for the system are also different. All the same, so the decision still has to start from itself.
Considering that the existing production line is relatively old, using foreign systems, the fit may be poor, and the investment cost will be high. Finally, the information department reported to the group’s high-level plan: to cooperate with Huazhong University of Science and Technology to develop one that can meet the maximum satisfaction MES system of own production line.
Huazhong University of Science and Technology, as the lead unit of the MES project in the discrete manufacturing industry of the National 863 Program, has in-depth research on the key technologies involved in the MES system. After in-depth analysis and research on JAC’s MES system requirements, Huazhong University of Science and Technology worked with JAC to formulate an overall solution for JAC’s MES system. The two parties cooperated in the development and implementation of the MES system.
JAC passenger car MES system was officially launched at the end of 2007. After a year of construction, it was put into online application at the end of 2008.
Three key elements of low-level integration
“The biggest difference between the MES system and the ERP system is that the former involves many integration issues with automation equipment.” recalled Wu Ruidong, deputy director of the Jianghuai Automobile Information Department. In the entire construction process of the MES system, there are three key factors that he pays most attention to. One of them is the integration with the underlying automation equipment. Such as coding equipment, testing equipment, etc., as well as the control system of the production line, and the operation data of the equipment, all need to be integrated with the MES system.
Since many equipment on the production line were made in advance, the MES system was not considered when the equipment was made. In addition to the aging of the equipment, it would take a lot of energy and time to read out the information on the equipment. , It is quite difficult to integrate.
Wu Ruidong, deputy director of the Jianghuai Automobile Information Department, cited a small case. A PBS (Painted Body Storage) area is installed in the painting and general assembly of the vehicle factory. There is a dispatching system in this area to control the entry and exit of the vehicle body. Before there was no MES system, the entry and exit of the car body was controlled manually according to the execution of the production plan. After the implementation of the MES system, it is necessary to install RFID on the body spreader to track the position of the body, and integrate the MES system with the PBS control system to realize the automatic control of the body in and out of the PBS area.
In addition to the integration with the underlying automation equipment, another key factor is the connection between the MES system and other related information systems such as ERP and SCM. The MES system needs to read the entire production plan from the existing ERP system, and the ERP may only reach the daily plan. For example, today ERP plans to produce 100 cars, but 100 cars contain different varieties. Some need to produce 10 cars, and some need to produce 20 cars. In the MES system, we must consider how these orders should be arranged, and what should be produced first, then what should be produced.
The MES system needs to divide these plans in more detail. In the daily plans issued by each ERP system, in addition to distinguishing the order of production, it also includes the redistribution of various elements such as vehicle color matching and variety matching.
Vehicles have to go through multiple processes on the production line, including on-line, interior trim, equipment completion, and inspection completion. In addition to accepting the ERP plan, the MES system also needs to track the information of the production process in real time and upload it to the ERP system. In addition, the MES system also transmits the data to other equipment systems. Therefore, the connection between MES and upstream and downstream systems is very important.
The last key factor of the MES system is whether it has flexibility and whether it can meet the continuous adjustment of the production line. “Most of the current automobile production lines require a relatively high system flexibility to meet the production needs of different models. This requires high flexibility of our system, including the adjustment of software and hardware.”
Because of the variety of automotive products, rapid update, product structure and manufacturing process are complex, the manufacturing process in the production is very closely related, and the production environment is also extremely complex and changeable, temporary order insertion, material shortage and other phenomena often affect the production plan The normal arrangement.
While Jianghuai Automobile is building a passenger car MES system, the company is expanding another sedan project with an annual output of about 200,000 vehicles. Compared with the previous, the biggest advantage of the MES system is that in addition to completing the plan more accurately, there is also a material pulling process, which can send animal material requirements on time according to the production status of the vehicle, so as to avoid a long time stop due to material shortages. String.
Speaking of the construction process of the MES system, Wu Ruidong can vividly remember the situation when everyone worked overtime at the beginning. “The more difficult part of MES is that the production line itself is an old production line, and the debugging process may conflict with the production line itself.” Therefore, everyone generally can only use the night time for system installation and debugging, and the production line must be restored during the day. Delay production. Once there is a problem with debugging at night, the production line will not start the next day. “This is more difficult.”
RFID detection
The MES system is located between the upper-level ERP and the lower-level control system. It is a management information system for the shop floor. Its goal is to control, track and effectively manage the production process, as well as to optimize the configuration of manufacturing resources including related people, materials, and equipment.
Although the launch of JAC’s MES system does not involve many major process and management system changes like ERP, it is inevitable to cause changes in the small processes on the production line.
After the previous production plan was released, it was necessary to manually print out the report through ERP, and then record where to code, and then manually operate to code. Now this link can be sent directly from the MES system and downloaded to the corresponding equipment system; after the vehicle is offline, the automation equipment can automatically complete the coding work.
The use of the MES system gradually transfers the data and information on the production line from manual transmission to the system, which not only reduces the workload of workers, but also reduces the interference and errors of human factors, and at the same time makes the rhythm of the production line more smooth. In addition, an indispensable method in the construction of the MES system is the extensive use of radio frequency technology for data collection on the production site.
On the production line of JAC’s workshop, when the vehicle is first launched, the electronic label must be updated first, and then the vehicle number is entered into the electronic label. When the vehicle is online, there is a spreader to lift it and attach it to the spreader. Electronic tags, when a vehicle passes a certain position, there will be a device to read the electronic tags, and then take the reading every step of the way. This approach can facilitate the identification of vehicles and at the same time transfer relevant information to other equipment systems through the MES system to smoothly proceed to the next step.
Wu Ruidong said that the current operation of the MES system basically meets the original design goals, and has played a role in management and monitoring of the production line. In the past, the production line was suspended due to insufficient materials, insufficient planning and thoroughness, or abnormal production equipment. The launch of the MES system has reduced such downtime, because the MES system speeds up the flow of relevant information and makes the production plan more reasonable and complete.
The MES system is a system closely attached to the production line. The less manual intervention and the higher the automation, the higher the production efficiency and the stability of the production line.
Jianghuai Automobile’s passenger car MES system has been making minor improvements since its launch. There are still some manual operations in the current process, such as data collection on the production site. During the process, some barcodes are still scanned manually. If all electronic tags are used, higher automation can be achieved.
Therefore, “the existing processes and systems need to be further optimized, and the planned scheduling needs to be more detailed and comprehensive.”
Information input audit
Because of its independent development, JAC’s MES system requires only two or three million yuan of investment in both software and hardware. Of course, this is inseparable from the “informatization investment audit” policy of JAC.
Informatization input audit is to conduct some effect evaluation after the project input, and overall measure whether it has exerted its due effect. Of course, such audits are often not aimed at a certain system, but are generally done as a whole.
Wu Ruidong introduced that informatization investment audit, the system evaluation of capital investment is one aspect, but not the most important aspect. The main aspects cover two major directions. One is to evaluate whether the existing system matches the business, that is, which system cannot meet the business needs or Deviated from the original design process of the system, it needs to be optimized and improved immediately; the second is to start from the direction of management and business process, to investigate whether which business is still unable to keep up with the advanced system requirements, and the management system and system need to be improved.
“The change of management is a gradual process, and the system itself is also a complex thing, so we need to make a package of improvements.”
In the construction of Jianghuai Automobile’s MES system, Wu Ruidong said that because it is based on custom development, there is actually no ready-made MES system and software, so their approach is based on the existing process and their own experience to realize what If the place is unreasonable, make improvements first, and then design the MES system after the improvements. For example, there must be a difference between the original manual planning and automatic scheduling, and the material management process has also been sorted out and improved.
JAC’s MES system supports the information release of the production site and the model configuration list to guide production; at the same time, it realizes the real-time data collection of the production site; improves the process monitoring and management of the entire vehicle assembly process; and makes the material distribution more accurate Timely, it realized the effective integration of MES with planning management and process monitoring layer.
Speaking of the feelings of the entire MES system construction process, Wu Ruidong said frankly that IT personnel need to have a full understanding of business processes and be able to look at informatization from a higher level than business personnel in order to integrate systems and management well. stand up. “Otherwise, the business department puts forward a requirement, but it does not match the overall plan, then it cannot be done blindly, so IT people themselves must understand the business.”
[ad_2]