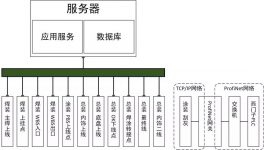
Zhidou Electric Vehicle Lean Production Tool–RFID Whole Process Work-in-Process Tracking System
[ad_1]
1. Project background
Zhidou Electric Vehicles Lanzhou plant produces new energy pure electric vehicles with an annual output of about 40,000. Zhidou Electric Vehicles Co., Ltd. is in the second phase of the construction of the MES system to meet the demand for timely tracking of vehicles on the assembly line and increase the demand for vehicles. The lean management of the entire assembly line area has introduced TBL Huaqing Kesheng’s UHF RFID-based product tracking management system for the entire process data collection management and traceability.
Two problem requirements
Automobile manufacturing is originally a typical large-scale production process, with a wide variety of materials, large quantities, complex processes and strict environmental requirements. The Zhidou electric vehicle production workshop is no exception. It has the following pain points in production and management:
◎The production line uses barcode technology to collect information, which requires workers to use a scanning gun for operation, which cannot be obtained in real time, and the labor cost is high, and errors such as missing barcode scanning are prone to occur;
◎The production tracking is incomplete, the efficiency is low, the data information is small, real-time monitoring and process traceability cannot be performed, and it is difficult to achieve lean management.
Three solutions
In order to solve these pain points, TBL Huaqing Kesheng customized this set of RFID work-in-progress tracking solutions for Zhidou Automobile, using RFID technology to replace bar code information collection, automatically collecting production site data, and real-time feedback and accurate tracking.

System architecture diagram
In the specific implementation, TBL Huaqing Kesheng provides the core software and hardware products of the RFID work-in-process tracking solution, including metal-resistant and high-temperature resistant RFID tags, RFID readers, gateways, and Noah IoT platform. These software and hardware are used in the entire production process from welding to the final assembly line.
◎The metal-resistant and high-temperature resistant RFID tags are installed on the vehicle body (recovered after the final assembly is off the assembly line). When the vehicle passes by, the system reads the RFID tag on the vehicle body and monitors the vehicle.
◎RFID readers are installed at key production points, and RFID reading and information binding are performed when the production process is over.
◎The Noah Internet of Things platform performs data docking with MES and manages RFID reading and writing equipment, thereby realizing a comprehensive tracking of the production process.
It is worth mentioning that in the general automotive production RFID tracking solution, during the process of welding and coating to the final assembly, the RFID tag will be replaced due to the replacement of the spreader, and the data transfer and binding between the RFID tags is required, which is likely to form a point of failure. And TBL Huaqing Kesheng’s solution breaks through this difficulty, using the same RFID tag from the welding assembly line to the final assembly line, simplifying the tracking process and making the production data more complete.


TBL Huaqing Kesheng RFID whole-process work-in-process tracking package realizes the comprehensive tracking of the production process of the Zhidou Automobile Factory; rapid identification of materials, information writing and abnormal situation alarms greatly improve production efficiency; at the same time, production managers can Get real-time information about the production site.
Four application value

According to the later data feedback of Zhidou Automobile, the original bar code information collection method requires 12 people to complete the collection operation part-time in the entire production process. After adopting the RFID WIP tracking program, the operation time of personnel can be reduced by 30% on average, and labor costs are reduced; at the same time, due to Automatic real-time collection and interaction of production site data improves the efficiency of production data collection by more than 50%.
Five applicable industries
TBL Huaqing Kesheng’s UHF RFID reader can realize the monitoring and analysis of multiple monitoring indicators; at the same time, it is compatible with abundant external sensor interfaces, has self-diagnosis function, strong anti-interference ability, and can be 365*24 uninterrupted Stable operation, with 99.99% data reading accuracy rate. The original Noah IoT platform provides a two-way transparent interface to realize unified data interaction in different hardware environments, and visualize data to realize real-time monitoring, fault prediction, and intelligent analysis.
Combining these high-quality industrial-grade software and hardware equipment, TBL Huaqing Kesheng’s RFID work-in-progress tracking solution can be used in many fields, not only in the automobile production plant, but also in other scenarios in the manufacturing industry and e-commerce retail. Applications, such as tire production tracking management, food and drug production tracking, cargo warehousing process traceability…TBL Huaqing Kesheng hopes to provide logistics services for more enterprises, help lean production management, and bring simpler, Efficient and intelligent real-time logistics.
[ad_2]