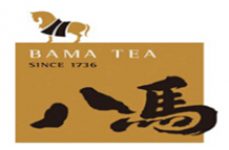
Application of Quality Traceability System in Fujian Bama Tea Industry Co., Ltd.
[ad_1]

【Customer Profile】
Bama Tea Co., Ltd. originated from the “Xinji” tea shop a hundred years ago. The head Mr. Wang Wenli is the representative inheritor of intangible cultural heritage and the thirteenth generation heir of Wang Shirang, the discoverer of Tieguanyin. At present, the company participates in the management of more than 50,000 acres of tea plantation base. There are two processing plants in Xiping and Longmen, with a total construction area of 60,000 square meters and an annual processing capacity of 6,000 tons. Among them, the Longmen processing plant is currently Asia’s most modern oolong tea Tieguanyin refined Processing plant.
【system introduction】
Shenzhen Jiukun Information Technology Co., Ltd. provides Bama Tea Co., Ltd. with six intelligent information systems including SCM, MES, WMS, franchisee management platform, e-commerce management and logistics Internet management. These six systems are related to Bama Tea Industry ERP (NC) system has realized seamless connection. Fundamentally, it realizes the automated and integrated management from supplier-production-warehouse-franchisees, e-commerce users-logistics.
Supplier platform: Realize the functions of inquiry, quotation, supplier selection, ordering, barcode printing, receipt and delivery, settlement, etc.;
WMS: Realize raw material warehouse management (receiving, quality inspection, return, delivery, warehousing), finished product warehouse management (quality inspection, warehousing, delivery, return, inventory), warehouse management, location management, Electronic billboards, etc.;
Franchisee platform: It realizes the integrated information operation functions of customers placing orders online, NC automatic order generation, payment, delivery, logistics query, and account reconciliation.
MES: It realizes functions such as production planning, product BOM management, process management, picking management, product packaging management, product weighing management, bar code association management, production progress management (electronic kanban), product quality traceability, and statistical reports.
E-commerce platform: realized order consolidation, freight calculation, NC automatic order generation, picking, delivery, logistics query, etc.;
Logistics management: Realize the functions of logistics information printing, logistics query, logistics information and shipping information association, logistics settlement, reconciliation, etc.;
【Customer System Value】
1. Automation and integrated management: use the system to make the company’s intelligent manufacturing fully automated and integrated operating system;
2. Supplier platform management: through inquiry, quotation, ordering, delivery, settlement and other links to ensure real-time interaction with supplier information, ensure delivery and timely reconciliation;
3. Production management: Through bar code turnover box association, production process management, etc., product traceability and quality monitoring are realized, and the production workshop realizes visual management through electronic billboards;
4. Warehouse link: Through the real-time management of the warehouse, the accuracy of the inventory is ensured; the control of the bar code realizes fast and accurate shipments, while also effectively preventing cross-stocking and anti-counterfeiting;
5. Franchisee management platform: seamlessly docked with NC, allowing franchisee channel merchants to place orders conveniently, query product prices, inventory, payment, and query order details and logistics information;
6. In e-commerce management: enable the warehouse to ship quickly and accurately; e-commerce platform orders and NC orders are completed synchronously;
7. Logistics management: enable the company to quickly query logistics information and reconcile with logistics settlement;
[Case icon]
Supplier platform:
Scan code traceability management:

[ad_2]