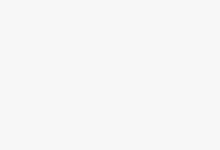
Avery Danny e-RFID tag application case
[ad_1]
1 Preface
Avery Danny é develops innovative identification systems and decoration solutions for global enterprises and consumers, and is a recognized leader in the industry. The company’s products include pressure-sensitive label materials, graphic media, retail apparel labels and branding systems, radio frequency identification inlays and labels, office supplies, special tapes, and a variety of products specifically designed for automotive, industrial and durable products Volume label. Ranked among the Fortune 500 companies in the United States, and ranked 69th among the “100 Best Employers in the United States” in 2006. Avery (Suzhou) Co., Ltd. is a wholly-owned company of Avery Danny E in China. The company’s total sales in 2006 were 5.6 billion U.S. dollars, and in 2008 total sales reached 6.7 billion U.S. dollars. There are more than 200 factories or sales organizations in the world, products are sold in 89 countries, and there are more than 22,000 employees. Since entering China in 1994, Avery’s Retail Consulting Services (RIS) department has established 4 production plants and 1 sales office in Nansha, Qingdao, Fuzhou, Suzhou and Shanghai, and has a sales network all over the country.
Avery Danny’s RFID department is headquartered in Flowery Branch, Georgia, and manufactures and sells RFID inlays and durable labels through label printers and system managers. Design, testing, and production facilities are located in the United States and Europe. Avery Danny’s RFID division is a leader in the global RFID market, serving manufacturers, consumer product packaging, pharmaceutical products, and the U.S. Department of Defense. Avery Danny’s RFID division is one of Avery Danny’s businesses.
RFID is very suitable for the aviation market. It has no linear field of view requirement, can scan objects faster, and can quickly locate the location of items. RFID solutions provide high returns on investments by airlines, airports and security agencies. Provides huge opportunities for improving efficiency and customer service. RFID baggage tag tracking reduces the loss rate by as much as 40%, improves the chances of on-time departure, and provides more commercial aviation security. à S Vegas McCarran International Airport is one of the pioneers, where the United States uses RFID tags. According to the estimates of the International Air Transport Association (IATA), RFID baggage tags will save the aviation industry 700 million US dollars each year, and will break this record in the next year or several years of operation. It costs about $100 to find the missing package, and missing luggage is a key factor affecting customer satisfaction.
Officials at Hong Kong International Airport stated that the cost of handling baggage at Hong Kong International Airport has dropped to 7 to 4 yuan per piece. Because the barcode is easy to cause damage or damage in the handling of luggage and parcels, and the scanning success rate is only 67% to 80%. The success rate of reading RFID tags in the same time is between 97% and 100%. International Air Transport D will estimate that RFID baggage tags will reduce the loss rate of accidental baggage by 30% to 40%, because there are almost no errors in RFID reading baggage tags. More importantly, through RFID radio frequency identification, you can quickly find packages that require re-security or priority processing. The RFID tag recognizes the package very quickly, so it can be quickly sent to the correct destination. Finally, RFID tags have not yet provided passengers with an additional identification. The post-911 security procedures stipulate that luggage will be deleted if the passenger does not show up. RFID tags can quickly locate and identify needed luggage, improving the chances of airlines’ flights departing on time.
On May 15, 2009, Avery Danny’s RFID department will cooperate with Motoror à and Print-O-Tape to provide Hong Kong Airport Authority with more than 70 million RFID-enabled baggage tracking tags. Motorola à has recently won a multi-year project contract. Hong Kong International Airport is one of the first airport pioneers to adopt RFID technology, which can greatly improve the reliability and efficiency of baggage handling systems. The airport will use Avery Danny’s AD-833 RFID inlay, hardware provided by Motorola à, and Print-O-Tape, which is responsible for luggage tags.
Wu Ziqi, deputy director of airport operations of the Hong Kong Airport Authority, said that in order to maintain the status of Hong Kong International Airport as a major regional and international aviation center, they promise to provide passengers with comfortable, fast service and the most advanced facilities. The application of RFID technology proves its continuous efforts to achieve high-quality services.
Unlike traditional barcode labels that require a scanner to read the label in sight, Avery Danny’s AD-833 RFID label is specially designed for the needs of the aviation industry and can be read at long distances without direct contact with the label. The RFID system can achieve an average reading rate of over 97%, which is more reliable than the 80% reading rate of the general traditional barcode system. The RFID tag system enables the baggage handling system of the Hong Kong Airport Authority to track baggage more accurately, help baggage be delivered in time, and airport flights and passengers depart on time. The system also helps improve luggage delivery and enhance customer service levels.
Jack Farrell, Vice President and Head of RFID Division of Avery Danny, said that they are very pleased to be able to provide tag inlays for this important project. Based on years of accumulated experience in the design and production of RFID tags, coupled with Motoroà’s leading position in the industry, and Print-O-Tape’s experience in printing luggage tags, the cooperation of the three parties will lead the development of RFID in the aviation industry. Innovative applications.
Hong Kong International Airport currently uses RFID luggage tags to check in luggage for passengers in multiple locations, including the check-in counters at Terminal 1 and Terminal 2, and the downtown check-in at the Airport Express Kowloon Station and Hong Kong Station. Check-in counters and check-in facilities in the upper reaches of the Pearl River Delta region. Currently, more than 70 airlines have participated in the project.
Avery Danny é, Motoror à and Print-O-Tape plan to continue to cooperate on the application of RFID in the field of baggage tracking to develop other markets.
Avery Danny é’s AD-833 RFID tag is specially designed for the needs of the aviation industry. It can be read at a long distance without direct contact with the tag. It is different from the traditional barcode tag that requires a scanner to read the tag in the line of sight. The RFID system can achieve an average reading rate of over 97%, which is more reliable than the 80% reading rate of the general traditional barcode system. RFID tag technology enables the baggage handling system of Hong Kong International Airport to track baggage more accurately.
2 RFID application cases in the retail industry
RFID technology provides one-stop service from manufacturing to sales. Due to the rapid and practical supply, the benefits of using RFID tags in retail clothing chains include inventory accuracy of 98%, which can reduce the number of people who count inventory every day, thereby increasing the number of people who interact with customers and improving customer service. It can also increase the position accuracy of the goods on the shelf to facilitate more effective replenishment of goods.
2.1 Metro Future Store uses RFID to track raw meat
Avery Danny e RFID company announced that Metro Group is using its AD-222 inlay chip to track raw meat in the future store in Toenisvorst, Germany. This AD-222 inlay chip can be embedded in an RFID tag to track the meat packaging tray of the bubble. The application of this label will help Metro better manage the flow of perishable food, reduce costs and save time for purchase.
Avery Danny’s solutions include conducting feasibility studies and designing RFID tags. However, a particular challenge for such labels is to meet food safety requirements. To this end, Eldanny E has strengthened cooperation with the European Fasson Roll company to provide S-2000n compatible adhesives that can come into contact with food. This type of RFID tag can be read in the refrigerator and complies with Metro Group’s food label safety regulations.
Dr. Gerd Wolfram, MGI Information Technology Manager of Metro Group, said that new technologies and new concepts are the key to meeting the ever-changing needs of customers. RFID plays a key role in ensuring the quality of fresh food, and this technology will help improve product quality and efficiency.
Avery Danny RFID vice president and general manager Robert Cornick said that Metro Group’s vigorous implementation of RFID technology shows to other retailers that RFID technology has achieved real benefits by improving efficiency and reducing costs. This AD-222 label inlay meets Metro Group’s high-performance standards, while Danny’s proprietary high-volume manufacturing process ensures uninterrupted supply.
2.2 Global fashion group Gerry Weber chooses Avery Danny RFID solution
Gerry Weber, a leading fashion company with 338 HOUSES OF GERRY WEBER branches and 1,400 shop-in-shops around the world, will become the first retail company in Germany to promote radio frequency identification (RFID) technology with inventory management and loss prevention functions. Gerry Weber uses Avery Dennison’s RFID solution to use an RFID chip embedded in the ironing instructions label to produce more than 25 million pieces of clothing each year. The solution will optimize Gerry Weber’s logistics and retail processes, reduce the incidence of theft, and ensure that the store maintains an adequate inventory of hot products.
Gerhard Weber, Chairman of Gerry Weber International AG, said: “The decision to promote RFID is a real milestone for our company. We recommend that all textile and apparel suppliers adopt RFID to significantly save costs, increase efficiency and retail transparency.”
Avery Danny RFID fabric ironing instructions tags will be applied in the production process, so that retail employees do not have to install and remove traditional large security tags in the store-which is not only time-consuming but also costly. After the customer pays at the cashier, the signal in the Avery Danny RFID tag can be automatically released.
Avery Danny E, Middle East and Africa vice president and general manager Graham Diamond said: “We are very pleased to work with Gerry Weber, they have led the German market to adopt this smart solution. Because they are helping retailers increase sales. RFID technology has brought significant advantages in terms of, profit and customer service. RFID technology has developed rapidly all over the world.”
RFID does not require sight or physical contact for data collection, so Avery Danny é solutions will enable Gerry Weber Group to significantly improve its inventory management and logistics processes, achieve faster and more accurate goods receipt, improve inventory control and transparency And simplify inventory counting.
Dr. David Frink, Director of Logistics at Gerry Weber, said: “This technology allows us to improve the accuracy of retail store inventory, and therefore improve the supply of goods. For example, time-consuming survival inventory work will no longer exist.”
RFID tags (also from Avery Danny é) are embedded in the ironing instructions label, which can be cleaned in water temperatures up to 140 degrees Fahrenheit (60 degrees Celsius) and can also be dry cleaned. This realizes the whole process of clothing from production to shelf, even in the process of washing or dry cleaning, it can be tracked.
The new RFID system has been successfully tested in Gerry Weber stores, and Gerry Weber will roll out this solution to more than 150 branches next year.
Avery Danny E is a leader in RFID technology in the apparel industry. Now, more than 90% of RFID tags in the textile industry come from Avery Danny.
2.3 American Apparel uses RFID tags to implement single product labeling and clothing tracking
American Apparel has always been known for breaking the conventions of the clothing retail industry. In the United States, a country where 96% of its clothing is imported, American Apparel does the opposite. The company has sewing, design and dyeing factories in Los Angeles, and all products are produced in Benshi. In addition, although the product does not have the company logo printed, and no celebrities are invited to promote it, young people, hippies and urbanites all recognize the brand very much. American Apparel has 180 stores in 13 countries. Now the company has decided to use RFID tags for item-level labeling and product tracking, and is confident in the company’s RFID applications.
American Apparel representatives first contacted RFID manufacturer Vue Technology at the RFID Journal Apparel and Footwear Summit in New York last August. At that time, the company had had discussions with RFID hardware providers Motorola and Avery Danny Retail Information Services.
After that, American Apparel started a pilot project with Vue, Motorola à and Avery Danny é in a store at Columbia University in New York in October last year. American Apparel uses Vue’s TrueVue software platform to manage electronic product codes and inventory data, uses Motorola à reader to collect data, and Avery Danny é tags to achieve product tracking. Vue is the main integrator for this pilot project, said Gordon Adam, Vue’s senior vice director of sales.
American Apparel uses RFID tags to implement single product labeling and clothing tracking. It plans to implement the RFID system in 17 New York stores within 3 months. The main goal of American Apparel’s RFID system is to improve the accuracy of inventory and better store clothes on the sales floor. After adopting this system, the company quickly saw the benefits: zero stocks in the sales floor and faster inventory of all clothing in the store. The inventory of the store used to take 4 workers 8 hours to complete, now it only takes 2 workers to complete it in 2 hours, so that employees have more time to help customers shopping and complete other tasks.
Based on the good results of the pilot project, American Apparel believes that RFID technology will also have a positive effect on other aspects of its business process, and has decided to formally adopt the RFID system in the pilot store and 16 other stores in New York. The company plans to complete the installation of the New York store within 3 months, and then install the system in 128 other North American branches.
American Apparel’s products are very simple, including T-shirts, sweatshirts, underwear, etc., all of which are basic, but the colors are extremely rich. American Apparel’s approach to clothing inventory is different from other clothing retail stores. Adams explained that there are many sizes and colors of every piece of clothing in American Apparel; only one piece of clothing of a certain color and size will be displayed on the sales floor, but make sure that all types of clothing are in Exhibited on the sales floor. This means that once you buy a piece of clothing, you will not find exactly the same clothes on the sales floor. In order to replenish goods in time, employees must regularly obtain sales lists from the cash register and take out the missing clothes from the warehouse.
In the pilot store, a reader installed at the cash register reads the RFID tag of each piece of clothing sold and transmits the data to the Vue software, which triggers an alarm on a computer screen in the inventory room. The staff then took out the clothes that were sold. When the clothing is brought to the sales place, the reader antenna installed between the stock room and the sales floor reads the tag, sends the information to the software, and the software then updates the location of the goods.
During the pilot project, employees in the Columbia University store have adopted a batch of Avery Danny’s AD-220 EPC Gen 2 passive tags and pasted them on the clothes shipped from the Los Angeles manufacturing center. But as the company decides to formally adopt this system, the company plans to complete the labeling work at the manufacturing site.
When the goods leave the distribution center, the Motorola à XR440 fixed reader installed on the warehouse door will read the hand-pasted EPC Gen 2 shipping label on the outside of each box and compare it with the EPC code of all clothing labels in the box. correspond. All these data-the EPC code of the container and the clothing, the reading event (including the time and the position of the reader)-will be sent to the TrueVue software platform.
When the retail store receives the labelled box, another Motorola XR440 fixed reader will collect the EPC data and send the data to the store’s Vue software. The software corresponds to the received goods and the factory delivery order in advance. Then, the Vue software added the goods to the store inventory, and the employees used Motorola à MC9090-G RFID handsets to regularly check all the goods in the sales venue.
The signs posted on the store let customers understand the application of RFID tags and the purpose of inventory tracking. Currently, tags are recycled and reused at the cashier. However, once retailers start to install this system in other stores, RFID tags will still remain on the clothes.
So far, Adams stated that American Apparel has placed an order for 1 million RFID tags from Avery Danny, which will be used in 17 stores in New York. “These tags are estimated to only last for 6 months,” he said. “The company is expanding the number of branches every year, which means that the number of orders for tags in the future is very substantial.”
2.4 RFID application case of Santa Fe glasses store
In recent years, the American Santa Fe Optical Store has deployed an RFID security system in its store in Austin, Texas. Before the installation of the system, the store lost as much as $12,000 per year due to theft. After the application of the system, the store reduced the loss to zero. Currently, Santa Fe is adding an RFID-based inventory management system to its existing system.
The system used by the Santa Fe Optical Store includes a 915 MHz EPC Gen 2 RFID tag purchased from Avery Danny’s Printer Systems Division. The label is designed by Avery Danny E in the shape of an hourglass and can be attached to the temples of the glasses with adhesive. The hardware and integration services of the system, including handheld RFID readers and antennas, are provided by Electronic Inventory Solutions (EIS). EIS was established in 2003 and is located in Carrollton, Texas. It specializes in providing RFID system solutions for high-value markets. Its business includes designing and manufacturing RFID hardware, software and system integration services for retailers. EIS products mainly include RFID security systems and handheld verification systems, all of which can be used to improve the visibility of customer assets.
When the Santa Fe Optical Store opened its third store in Austin a year ago, there were frequent thefts in the store, and the loss caused by each theft was as high as $5,000. To this end, Bob Ross, an optometrist at the shop, began to look for a security system and required that the system label should not be as big as the label used in the electronic article surveillance system (EAS). Because if a label as big as an EAS label is used (RF bulletin: EAS label size is 1.5×2 inches long; 1 inch wide; 1/8 inch thick), customers will have a lot of difficulties when trying out the frame. Darryl Hubbard, president of EIS, pointed out that one of the attractions of RFID tags is their small size. Almost a year ago, Rose found and cooperated with EIS and installed a set of RFID-based access control system, in which the antenna device was connected to the alarm. After installing this system, employees will first put RFID tags on the temples before entering the warehouse. These labels are as thin as paper before being pasted, and their dimensions are 1.75 x 1.25 inches. When attached to the temple of the glasses, the label will be folded in half again. Each label is printed with a code, which is the same as the code on the RFID chip in the label. At the same time, employees manually input RFID tag codes and other information such as frame manufacturer, receipt date, and price into the stock database of the optical shop.
When selling a pair of glasses, the employee will tear off the RFID tag on the temple. If the label is moved without being torn off, and the customer tries to pass through the door and the store entrance, an alarm will be triggered. Hubbard said that RFID tags have been proven to be very reliable, and every tag provided by Avery Danny E can operate normally. This security system has been tested very successfully, and Santa Fe has decided to extend the RFID system to the entire inventory process. In the past, the inventory process was usually manual and recorded with pen and paper. EIS is currently installing an RFID system in this process, and employees can use handheld RFID readers to automatically count the entire store. This closed-loop RFID system is currently being integrated into the Santa Fe glasses store’s inventory database. According to Hubbard, the inventory management system will be launched in two months.
The working principle of the system is as follows: In the optical shop, the designer or manufacturer will display the glasses in cabinets. Once the inventory management system is in place, employees can download the inventory serial number associated with a specific counter to the handheld reader, and then use the handheld reader to walk around the counter. At this time, a list of glasses inventory numbers will appear on the small screen of the reader. After the reader reads the RFID tags on the glasses frame, these numbers will disappear from the screen. If there are any numbers on the screen, employees can walk to other counters in the store to find the corresponding frame.
Hubbard said that the use of RFID systems will help Santa Fe optical shops reduce inventory count time by 80%. Using handheld readers, employees only need 40 minutes to complete the inventory count, and if not using RFID technology, it would take at least eight hours. Once the optical shop officially implements the inventory system, Santa Fe will deploy two systems in the other two stores, including an RFID security system and an RFID inventory management system.
RFID application cases in the medical industry
Pharmaceutical retailer Walgreens installed an RFID system for the company’s 600,000-square-foot distribution center in Ende City. The system sends out when an employee loads goods onto the wrong truck (delivered to various retail stores in the southeastern United States) Alerts help companies reduce cargo loading errors and eliminate paper records.
This system, implemented by RFID equipment company Blue Vector, enables Walgreens’ warehouse management system to automatically send pre-shipment notifications when products leave the center. The system includes 170,000 plastic containers with EPC Gen 2 passive RFID tags, some labelled trolleys, and 45 Blue Vector RFID door readers installed in the warehouse door and elsewhere in the center.
Walgreens tried this RFID system a year ago, and it worked well. Now the retailer has installed the same system in its Connecticut distribution center.
The distribution center in Ande City was completed and put into use in 2007. Nearly half of the employees in the center have physical or intellectual defects. One of Walgreen’s original intentions for adopting the RFID system was to make it easier for employees’ daily work, said John Beans, deputy director of marketing at Blue Vector. The company’s ultimate goal is to reduce the delivery error rate of all distribution centers and eliminate paper records.
When a cargo box is delivered to the wrong shipping door, or the cargo box is loaded onto the truck in the wrong order, the system will issue an alarm notification. A truck often transports multiple goods to different stores, and the goods must be loaded onto the truck in the order of delivery.
Walgreens uses a plastic container with a size of approximately 2 feet * 18 inches * 12 inches. When the center receives an order, the employee puts the required goods in the container, puts it on a trolley with other containers, and then pushes it through the warehouse door.
In the past, the staff read the delivery list of the goods, and then used the scanner to read the barcode label of the container, log in to the warehouse management system on the computer, log off the delivery of the goods, and ensure the correct loading sequence of the containers. The truck loading process of the old system is very troublesome and error-prone, especially when more than a dozen trucks destined for different destinations are loaded at the same time, Beans said.
After adopting the Blue Vector system, Avery Dennison’s RFID tags are installed on the sides of all cargo boxes. Empty containers waiting to be loaded are stacked in a storage area. When an order list is sent to the center, the warehouse management system automatically shares it with Blue Vector’s system server. When the employee puts the container full of goods on a conveyor belt and sends it to the trolley, a Blue Vector door reader reads the ID number of the container label and corresponds it to the order. In this way, the system knows the cargo in the container.
The full cargo box is then placed in a trolley (the trolley is also labeled), and when it is pushed to the warehouse door, it passes through a Blue Vector RFID door reader. The reader is 7 feet high and includes a Motorola RFID reader and an LED screen. The LED screen displays data related to the cargo boxes, including the location where they will be loaded.
The cart then passes the correct door, and another Blue Vector door reader scans the ID number of each container and the cart label. If a batch of cargo boxes pass the wrong door, or the batch of goods is wrong Load sequentially, and the system issues an alarm.
Once the boxes are loaded into the correct truck in the correct order, the Blue Vector portal reader sends a notification to the warehouse management system via a wired connection, and the system then forwards the notification to the receiving store. After the empty container is sent back to the distribution center, the reader reads the label, and the staff cleans the empty container and scans the label again. The damaged container or the container whose label cannot be read shall be sent to the repair shop for repair or replacement.
This system includes 45 door readers, one installed at every other warehouse door. The reader includes Blue Vector’s edgemanager software, which can match the ID number of the container label with the shipping data and identify errors. All readers installed on the warehouse doors or conveyor belts are managed by 65 edgemanagers. The software receives information from the readers and analyzes the position of the cargo box based on those read data. Then, edgemanager shares relevant data with BlueVector network.
According to Beans, the system was tested in 2007 when only a few RFID readers were used. When the distribution center was completed, Walgreens fully activated the system. The distribution center transported approximately 80,000 labeled containers to more than 700 stores every day.
3 Avery Danny e Future RFID Trends
3.1 HF RFID tags
The HF RFID market usually includes three major parts: media management, healthcare, and asset tracking. Avery Danny é initially set foot in this technology to address this market segment through a product portfolio. Avery Danny’s RFID department will release three new high-frequency tags at the RFID magazine event held in Orlando in April this year. The three new products are AD-709, AD-714 and AD-720. It is reported that they will also provide A variety of configurations to meet application requirements.
Jack Farrell, Vice President and Head of the RFID Division of Avery Dennison, said: “Our continuous expansion of our product portfolio into the high-frequency RFID field is to provide our best products to a wider range of market applications. When we serve our customers When providing a wider range of industry-leading ultra-high frequency (UHF) label products, many customers have indicated that they also have high-frequency label needs. The new HF product line is successfully developed for customers based on years of accumulated experience. RFID solutions coming out.”
3.2 Application of RFID in petrochemical industry
Extremely high oil prices and high global demand have prompted the oil and gas industry to seek RFID technology as a means to gain insight into the industry. From streamlining product procurement to improving the safety and reliability of field equipment, all of this can be automated or improved through RFID technology.
To this end, the Oil and Gas RFID Solutions Group was established. This group is a problem expert alliance formed by RFID academic research and technology suppliers, including Avery Danny E and Merlin Concept Technology Company.
Konrad Konarski, vice president of Merlin, said that one of the goals of this working group is to provide concise guidance for the adoption of RFID technology in the oil market. This requires the determination of the best plan, operation process, data model and application architecture, and on this basis can we provide clear opinions and suggestions for the oil industry to deploy RFID systems to improve operations.
Currently, this multidisciplinary team of experts is helping exploration, drilling and production companies to identify, define, develop, and deploy RFID systems to solve fundamental problems inherent in their respective fields. Maggie Bidlingmaier, Marketing Director of Avery Danny e said, “The company is honored to join this expert group. Avery’s goal is to continue to innovate RFID solutions and use its expertise to provide the best labeling and testing services for the petroleum industry.”
The system used by the Santa Fe Optical Store includes a 915 MHz EPC Gen 2 RFID tag purchased from Avery Dennison’s Printer Systems Division. The label is designed by Avery Dennison into an hourglass shape and can be attached to the temples of the glasses through an adhesive. The hardware and integration services of the system, including handheld RFID readers and antennas, are provided by Electronic Inventory Solutions (EIS). EIS was established in 2003 and is located in Carrollton, Texas. It specializes in providing RFID system solutions for high-value markets. Its business includes designing and manufacturing RFID hardware, software and system integration services for retailers. EIS products mainly include RFID security systems and handheld verification systems, all of which can be used to improve the visibility of customer assets.
[ad_2]