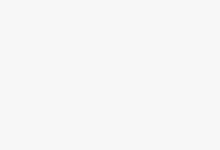
Canadian leather retailers use RFID technology to ensure inventory transparency
[ad_1]
Canadian luxury leather brand Daniel tested an RFID solution for its three retail stores in Toronto. The solution can accurately count retail store inventory and remind staff to replenish goods in time when the goods are insufficient, which greatly reduces inventory inventory time. Improve work efficiency. Two of these retail stores will be deployed this summer, and another one will be deployed in September. Through the test system, it is found that the solution can reduce the inventory counting time from 15 hours to less than 1 hour. In addition, the greater benefit of this solution is to improve the efficiency and accuracy of replenishment in retail stores. The application of this solution is mainly concentrated on high-quality jackets, wallets, briefcases and other commodities.
Danier includes a total of 90 retail stores. As each retail store conducts inventory checks on a regular basis, the inventory shrinkage rate is low, and the traditional inventory check is time-consuming, laborious, and inefficient, and retail stores cannot replenish in time. With the implementation of the Truecount system, you will receive a replenishment notice immediately after the product is sold, so that the staff can be notified to replenish the goods in time. The program includes ultra-high frequency (UHF) EPC Gen 2 passive RFID tags and handheld and fixed RFID readers attached to the goods.
In view of the successful implementation of the pilot in Mississauga and Toronto, the system was tested in Burlington a month ago. The Smartrac UPM MiniWeb label is used in the scheme, which is embedded in the price tag of the product. When the product arrives at the retail store, it uses Motorola’s MC3190-Z RFID handheld read-write unit to read the unique ID code of the tag and send the code to the back-end database. (The tag tag code is associated with the stock-keeping unit (SKU) stored in the independent Truecount data software in the background.) Then, the system updates the data and puts the goods into the warehouse.
When goods are moved from inventory to retail stations, they pass through a fixed RFID reader (Motorola FX7400). The reader reads the tag code and sends it to the back-end database via a wired connection to collect statistics on the goods shipped to the retail station.
In addition, a fixed FX7400 RFID reader is also installed under the retail counter to read the tag information of the goods on the counter. After the product is sold, the label information cannot be read, and the database is updated. According to the information of the read label, when the quantity of goods on the counter drops to a certain level, the system sends out a replenishment notice. After adopting the RFID-based solution, the inventory counting time has been reduced from the original 15 hours to less than 1 hour.
In the next few weeks, Danier will use Motorola’s MC9808 RFID barcode scanner to scan labels and barcodes at the same time. Through the test of the system, the time for staff to take inventory is greatly reduced. If the installation of the system has a higher return on investment (ROI), the company will install the solution in all stores.
[ad_2]