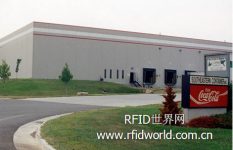
Coca-Cola beverage bottle manufacturer uses RFID to accurately understand the number of times the shipping container is used
[ad_1]
Southeastern Container is a large plastic products company in the United States, responsible for the production of 70% of Coca-Cola’s local bottle production. After the company successfully tested the use of an RFID system to count the usage times of about 6,000 plastic containers at its injection molding plant in North Carolina, it is now extending the system to two other plants. Southeastern Container plans to track up to 40,000 plastic containers (used to transport preform plastic tubes produced by injection molding plants) to Southeastern Container’s blow molding plant. There the preforms are blown into bottles.
Southeastern Container is a large plastic products company in the United States.
Responsible for the production of 70% of Coca-Cola’s local bottle production.
Previously, Southeastern Container used cardboard boxes to ship products. When the company switched to specialized, reusable plastic containers, the company decided to test the RFID system to track the number of times the plastic containers were used.
The design of the old cardboard box is not suitable for the company’s cargo trailer, said John Underwood, engineering manager of Southeastern Containe. Cardboard boxes also take up a large area of the warehouse. He added, “The plastic containers we currently use provide us with significant economic advantages.” Underwood explained, “The new containers can maximize the capacity of the trailer when shipping products. , Because the container is easy to disassemble (for storage), we can maximize the number of containers returned by the trailer. In addition, the reusable plastic container has a longer life cycle.”
However, plastic containers themselves cost more, so Southeastern Container hopes that their use time will reach the manufacturer’s promise, making them worth the money. “We need to know exactly how many times each container is used,” Underwood said, “confirm that the container manufacturer’s commitment is in line with the actual situation.” Since Southeastern Container does not want to hire specialized personnel to count the number of times each container is used, the company uses EPC Gen 2 tags, readers and antennas.
In cooperation with DecisionPoint Systems, a consulting services and system integration company, Southeastern Container started a proof-of-concept project a year ago. The system was officially launched at the beginning of last summer. The company installed Alien Technology’s EPC Gen 2 label M-Tag on the side of the existing plastic container at its Enka injection molding plant. The M-Tag label contains an adhesive on the back, and the label is attached when the surface of the container is heated by a small flame device. The label has been adhered to the box throughout its life cycle.
A single container can hold 20,000 preforms, Underwood says, depending on their size. When a labeling container is filled with preforms, a bar code label is affixed to identify the type of preforms in the box. Then, the container moves through an entrance and exit containing a Motorola XR440 industrial-grade RFID reader and an AN400 RFID antenna. After the reader reads the ID code of the RFID tag of the container, an employee uses a Motorola MC9090-G mobile computer to scan the bar. The Oat asset tracking middleware of OATSystems corresponds the ID code of the container label to the product category identified by the barcode, and provides a web service window connected to the Southeastern Container ERP system. In this way, the ID code of the label and its corresponding products can be entered into the company’s ERP system for tracking warehouse and inventory operations.
The container is then transported to a warehouse, and then transported from the warehouse to the blow molding plant. When a container is emptied, the employee scans the barcode and deletes the corresponding record of the RFID number of the container and the product in the container in the ERP system.
According to Underwood, after several small changes to the antenna position and adjustments to the reader power settings, Southeastern Container has achieved a stable and accurate tag reading rate. The label costs less than $1, and the container can be read from any direction.
According to Underwood, in order to provide this “plug and play” system to Southeaster Container, DecisionPoint reviewed all the RFID devices currently on the market and also tested several readers and tags. At present, there are almost no flaws in the work of this system.
Now, Southeastern Container is also launching RFID systems in two other injection molding plants. The company expects to achieve a return on investment within two years.
In addition, Southeastern Container also plans to launch other applications that can take advantage of RFID tags and readers, including tracking outbound containers, transportation processes, and receiving, emptying, and returning containers from blow molding plants.
[ad_2]